Introduction
When it comes to industrial flooring solutions, GRP moulded grating has emerged as a leading choice for many industries—outperforming traditional materials like steel, aluminum, and wood in numerous ways. Whether you’re looking to enhance safety, reduce maintenance costs, or improve corrosion resistance, GRP moulded grating offers a comprehensive solution. In this article, we will explore why GRP moulded grating outperforms conventional alternatives, along with real-world benefits that reinforce its growing popularity.
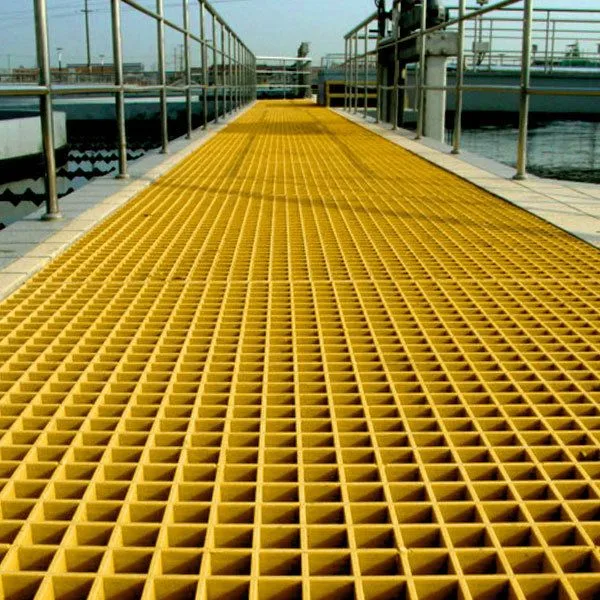
grp moulded grating
Understanding GRP Moulded Grating
What Is GRP Moulded Grating?
GRP (Glass Reinforced Plastic) moulded grating is a high-strength composite material made by combining glass fibers with thermosetting resins. This manufacturing process ensures a uniform structure that delivers excellent load distribution, resulting in a strong yet lightweight flooring solution. Because of its robust construction, GRP grating is sometimes referred to as fiberglass or FRP (Fiber Reinforced Polymer) grating.
Key characteristics of GRP moulded grating include:
- Corrosion Resistance: Does not rust or deteriorate when exposed to chemicals or moisture.
- Lightweight Design: Offers easy handling and reduces transportation and installation costs.
- Non-Conductive Properties: Enhances safety in electrical environments.
- Low Maintenance: Requires minimal cleaning and upkeep.
Common Applications Across Industries
Due to its versatile properties, GRP moulded grating is used in a variety of settings:
- Marine and Offshore: Provides reliable decking on ships and oil platforms due to resistance to saltwater corrosion.
- Chemical Processing: Endures harsh chemical exposures and prevents surface damage.
- Food and Beverage: Offers sanitary, slip-resistant walkways in processing plants.
- Water Treatment Facilities: Withstands exposure to constant moisture and corrosive chemicals.
According to a study by the Composites Market Forecast (an independent industry analysis group), the global demand for composite gratings—including GRP moulded grating—has increased by approximately 20% in the last five years, owing to their ability to meet the stringent safety and durability standards across multiple sectors.
Key Advantages Over Traditional Materials
Corrosion Resistance
One of the most significant advantages of GRP moulded grating is its built-in corrosion resistance. Unlike steel, which can rust without proper coatings, or wood, which can rot over time, GRP moulded grating remains structurally sound in environments where exposure to water, chemicals, or salt is a constant challenge. This characteristic is especially crucial in:
- Marine Docks and Piers
- Wastewater Treatment Plants
- Chemical Storage Areas
Lightweight Yet Durable
While steel can provide similar levels of strength, it’s heavier and more difficult to install. In contrast, GRP moulded grating strikes a remarkable balance between weight and durability:
- Transport Efficiency: Reduced shipping costs and easier manual handling.
- Lower Installation Time: Faster setup means less downtime and labor expenses.
Cost-Effective and Low Maintenance
Traditional materials often carry hidden costs such as painting, coating, and frequent repairs. GRP moulded grating, however, requires minimal upkeep. A simple rinse or mild detergent wash usually keeps it clean, meaning:
- Fewer Maintenance Intervals: Leads to lower long-term operational expenses.
- Greater ROI: With proper care, GRP grating can last decades, often outliving steel and wood counterparts.
Safety and Ergonomics
GRP moulded grating can be manufactured with anti-slip surfaces, significantly reducing the risk of workplace accidents. It also stays cooler under direct sunlight compared to metal, contributing to a safer, more comfortable environment. In industries where employee health and safety are top priorities, these features offer a compelling reason to switch to GRP.
How GRP Moulded Grating Outperforms Steel, Aluminum, and Wood
Enhanced Strength-to-Weight Ratio
Steel might have a high load-bearing capacity, but its weight can be impractical for certain applications. Wood is lighter but lacks the resilience needed in many industrial settings. GRP moulded grating provides a sweet spot by offering:
- High Tensile Strength: Equal or superior to many metals on a weight-to-strength basis.
- Lower Overall Weight: Makes it easier to handle, cut, and customize on-site.
Extended Lifespan in Harsh Environments
Wood is particularly vulnerable to moisture, pests, and rot, while metals can weaken over time due to rust or chemical exposure. By contrast, GRP moulded grating remains largely unaffected by extreme temperatures, UV rays, and chemical spills:
- Long-Lasting Performance: Ideal for outdoor setups exposed to variable weather.
- Consistent Quality: Maintains structural integrity even under constant stress.
Reduced Risk of Slips and Falls
GRP moulded grating can be manufactured with integral grit surfaces, offering extra traction. This slip-resistant design is a critical safety feature, especially in slippery or wet conditions often found in industrial and marine environments. Its non-conductive properties also add an extra layer of safety around electrical installations.
Factors to Consider When Choosing GRP Moulded Grating
Load-Bearing Capacity
Although GRP moulded grating can support substantial loads, it’s essential to confirm specific weight ratings to match your application. Different grating thicknesses and designs cater to different needs, so consult manufacturer datasheets or engineering guidelines to ensure you select the right product.
Key questions to ask:
- What is the maximum load requirement?
- Is there a specific load distribution pattern (point load vs. uniform load)?
Installation and Customization Options
GRP moulded grating comes in a variety of panel sizes and resin systems, and can be easily cut to fit unique floor plans or architectural designs. Consider:
- Panel Size and Thickness: Matches your workspace dimensions for seamless installation.
- Surface Grit Options: Optimize slip-resistance for high-traffic areas.
- Colors and Resin Types: Some formulations are specifically engineered for fire resistance or enhanced chemical protection.
Conclusion and Call to Action
As industries continue to prioritize safety, cost-effectiveness, and sustainability, GRP moulded grating stands out as a superior alternative to steel, aluminum, and wood. From its corrosion resistance and lightweight design to its long lifespan and slip-resistant surface, GRP moulded grating addresses the most pressing challenges of modern industrial environments.
If you’re ready to take advantage of its benefits, start by evaluating your specific load requirements and exploring available customization options. Interested in learning more? Leave a comment below with your questions or experiences, and share this article with your network to help them discover why GRP moulded grating outperforms traditional materials. Let’s continue the conversation and drive innovation in safer, more efficient industrial flooring solutions.