Introduction
When it comes to reinforced concrete, choosing the right material for reinforcement is crucial. Traditional steel reinforcement has long been the standard, but there is a modern alternative that offers numerous advantages: fiberglass rebar. In this article, Unicomposite composite profiles will explore why Hughes Brothers Fiberglass Rebar is the ideal choice for reinforced concrete projects.
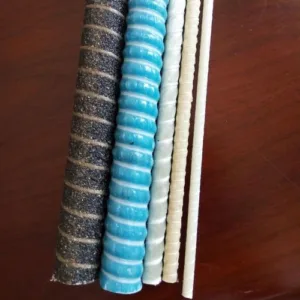
hughes brothers fiberglass rebar
1. The Advantages of Fiberglass Rebar
1.1 Lightweight and Easy to Handle
Fiberglass rebar is significantly lighter than traditional steel rebar, making it easier to transport and install. Its lightweight nature also reduces the strain on workers, improving overall efficiency and safety during construction projects.
1.2 Corrosion-Resistant
One of the most significant advantages of fiberglass rebar is its excellent corrosion resistance. Unlike steel, fiberglass does not rust or corrode when exposed to moisture or harsh chemicals. This property ensures the longevity of the reinforced concrete structure, reducing maintenance and repair costs over time.
1.3 High Strength-to-Weight Ratio
Despite its lightweight nature, fiberglass rebar offers remarkable strength. It has a higher tensile strength than steel rebar, allowing for efficient load transfer and reinforcement of concrete structures. This high strength-to-weight ratio makes it an ideal choice for projects that require durability and structural integrity.
1.4 Electrical Insulation
Another unique feature of fiberglass rebar is its electrical insulation properties. Unlike steel, fiberglass does not conduct electricity. This characteristic makes it an excellent choice for structures that require electrical insulation, such as bridges, marine applications, and structures near power lines.
2. Hughes Brothers Fiberglass Rebar
2.1 Company Overview
Hughes Brothers has been a trusted manufacturer of fiberglass products since 1924. With decades of experience, they have become pioneers in the field of fiberglass rebar production. Their commitment to innovation, quality, and customer satisfaction sets them apart in the industry.
2.2 Manufacturing Process
Hughes Brothers utilizes advanced manufacturing processes to produce high-quality fiberglass rebar. The process involves impregnating continuous glass fibers with a specialized resin system, resulting in a product with exceptional mechanical properties and resistance to environmental factors.
2.3 Quality and Durability
Hughes Brothers Fiberglass Rebar undergoes rigorous quality control measures to ensure superior performance and longevity. It is engineered to withstand extreme conditions, including freeze-thaw cycles, chemical exposure, and high humidity. The durability of their rebar translates into reliable and long-lasting reinforced concrete structures.
2.4 Versatility and Customization Options
Hughes Brothers offers a wide range of fiberglass rebar products to meet diverse project requirements. They provide various diameters, shapes, and configurations, allowing for customization based on specific design needs. This versatility ensures that their rebar can be seamlessly integrated into any reinforced concrete project.
3. Applications of Fiberglass Rebar
3.1 Bridges and Highways
Fiberglass rebar is an excellent choice for bridge and highway construction due to its corrosion resistance and lightweight nature. It reduces the risk of concrete cracking and extends the lifespan of these structures, resulting in significant cost savings over time.
3.2 Marine Structures
In marine environments, where steel rebar is prone to corrosion from saltwater exposure, fiberglass rebar excels. It offers exceptional resistance to saltwater, making it the preferred choice for docks, piers, seawalls, and other marine structures.
3.3 Chemical Plants
Chemical plants often have harsh environments that can accelerate the corrosion of steel rebar. Fiberglass rebar provides a corrosion-resistant alternative, ensuring the structural integrity of chemical plants and reducing the risk of costly maintenance and shutdowns.
3.4 Parking Structures
Due to the constant exposure to moisture and de-icing chemicals, parking structures are susceptible to concrete degradation caused by steel rebar corrosion. Fiberglass rebar’s corrosion resistance and long lifespan make it an ideal solution for parking garages and ramps.
3.5 Rehabilitation Projects
When rehabilitating existing structures, fiberglass rebar offers a lightweight and corrosion-resistant solution. Its compatibility with standard concrete construction practices allows for easy integration into rehabilitation projects, providing enhanced durability and extending the lifespan of the structures.
4. Comparing Fiberglass Rebar to Steel Rebar
4.1 Corrosion Resistance
Steel rebar is susceptible to corrosion, especially in aggressive environments. Fiberglass rebar, on the other hand, is inherently corrosion-resistant, making it an excellent choice for projects where corrosion poses a significant concern.
4.2 Weight and Handling
Fiberglass rebar’s lightweight nature makes it easier to handle and transport compared to steel rebar. It reduces the risk of injuries during construction and simplifies installation, leading to improved project efficiency.
4.3 Electrical and Thermal Conductivity
Unlike steel rebar, fiberglass rebar does not conduct electricity or heat. This characteristic makes it suitable for structures that require electrical insulation or need to mitigate thermal transfer.
4.4 Design Flexibility
Fiberglass rebar offers design flexibility, allowing for creative and innovative construction solutions. It can be easily molded and shaped, enabling architects and engineers to bring their visionary designs to life.
5. Conclusion
Hughes Brothers Fiberglass Rebar is a superior choice for reinforced concrete projects. Its lightweight nature, corrosion resistance, high strength-to-weight ratio, and electrical insulation properties make it a reliable alternative to traditional steel rebar. Hughes Brothers’ commitment to quality, durability, versatility, and customization further solidifies their position as a leading manufacturer in the industry.
FAQs (Frequently Asked Questions)
6.6.1 Is fiberglass rebar more expensive than steel rebar?
No, fiberglass rebar is generally cost-competitive with steel rebar. While the upfront cost may be slightly higher, the long-term cost savings due to reduced maintenance and repair expenses make fiberglass rebar a cost-effective choice.
6.2 Can fiberglass rebar be used in extreme weather conditions?
Yes, fiberglass rebar is suitable for use in extreme weather conditions. It has excellent resistance to temperature variations, freeze-thaw cycles, and exposure to UV radiation, making it highly durable and reliable in harsh environments.
6.3 Is fiberglass rebar compatible with standard concrete construction practices?
Yes, fiberglass rebar is fully compatible with standard concrete construction practices. It can be easily integrated into concrete forms and poured just like steel rebar, making it convenient for contractors and construction teams.
6.4 How long has Hughes Brothers been manufacturing fiberglass rebar?
Hughes Brothers has been manufacturing fiberglass products since 1924, making them pioneers in the industry. With almost a century of experience, they have established a strong reputation for producing high-quality fiberglass rebar.
6.5 Is fiberglass rebar environmentally friendly?
Yes, fiberglass rebar is considered an environmentally friendly alternative to steel rebar. It is non-corrosive, which reduces the need for maintenance and repair, resulting in fewer resources being consumed over the lifespan of a structure. Additionally, fiberglass rebar is non-toxic and does not release harmful substances into the environment.