Introduction
Fiberglass floor grating has become a staple in various industries due to its durability, corrosion resistance, and versatility. In particular, wholesale fiberglass floor grating provides a cost-effective solution for large-scale projects that demand high-quality materials without breaking the budget. In this article, we’ll explore every facet of wholesale fiberglass floor grating, from its composition and benefits to installation tips and long-term maintenance strategies.
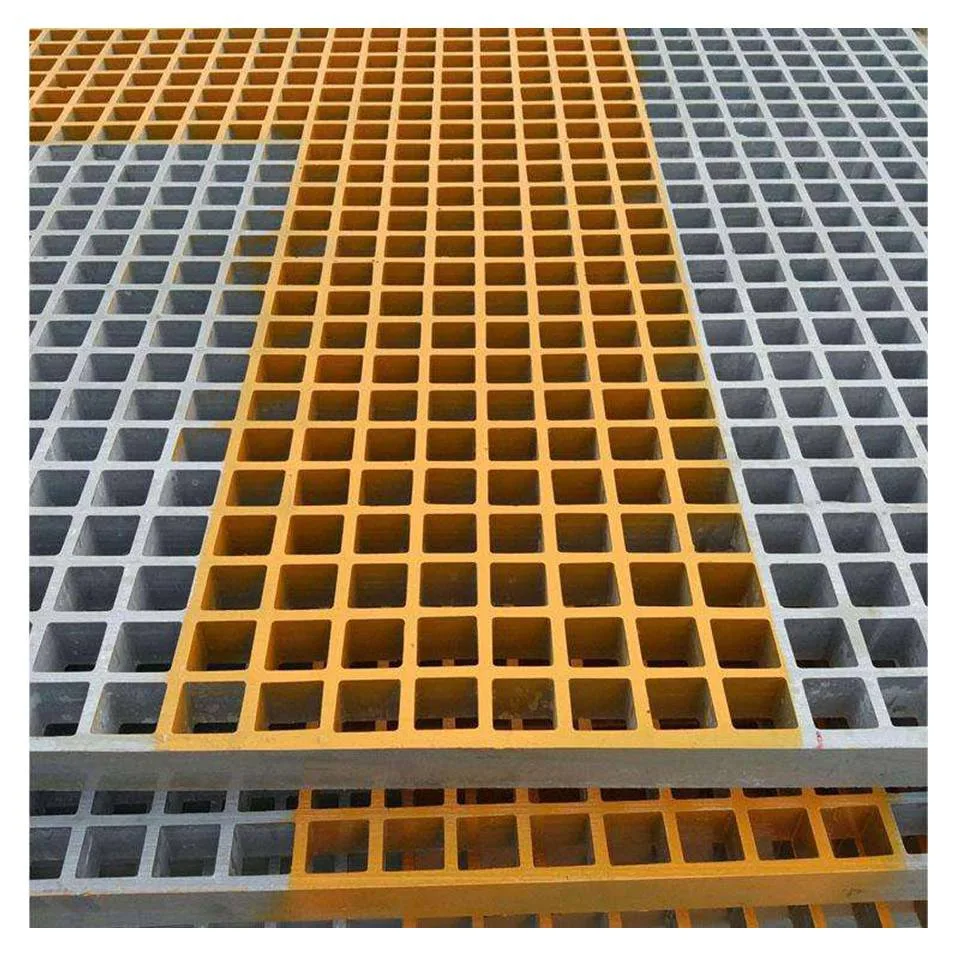
wholesale fiberglass floor grating
Understanding Wholesale Fiberglass Floor Grating
Composition and Manufacturing
Fiberglass floor grating, often referred to as FRP (Fiber Reinforced Plastic) grating, is a composite material made by combining glass fibers with a resin matrix. This process results in a lightweight yet robust structure that can withstand heavy loads and harsh environmental conditions. When you purchase wholesale fiberglass floor grating, manufacturers typically produce it in larger quantities, making it more cost-effective. Here’s how it’s usually made:
- Fiber Reinforcement: Layers of glass fibers are laid out in a mold.
- Resin Infusion: A resin solution (commonly polyester, vinyl ester, or epoxy) is poured over these fibers.
- Curing: The material is then heated or left to cure, forming a solid, rigid grating panel.
Key Benefits
Fiberglass floor grating stands out for several reasons:
- Corrosion Resistance: Unlike metal grates, fiberglass doesn’t rust or corrode, making it ideal for environments with chemicals, saltwater, or extreme humidity.
- Lightweight Strength: Despite weighing significantly less than steel, fiberglass grating maintains impressive load-bearing capacity.
- Electric Non-Conductivity: Fiberglass is non-conductive, reducing electrical hazards in sensitive or high-voltage areas.
- Low Maintenance: Its robust composition means fewer replacements and minimal upkeep over time.
According to a recent market study, the global fiberglass grating market is projected to grow at an annual rate of about 4–5% in the next five years, highlighting its increasing adoption across industries such as marine, oil and gas, and wastewater treatment.
Common Uses
Fiberglass floor grating is commonly deployed in:
- Chemical Plants and Refineries: Where corrosive elements are prevalent.
- Maritime and Offshore Platforms: Where materials must resist seawater and salt spray.
- Food and Beverage Processing Plants: Maintaining hygienic standards due to ease of cleaning and corrosion-free structure.
- Public Access Areas: Such as walkways, footbridges, and stairs for enhanced traction and safety.
Choosing the Right Fiberglass Floor Grating
Material Quality
Not all fiberglass grating is created equal. When buying wholesale fiberglass floor grating, ensure that the resin type (e.g., vinyl ester, polyester) matches your application needs. Vinyl ester resins, for instance, offer superior chemical resistance and are recommended for highly corrosive environments. Look for reputable suppliers with proven track records and ask for product certifications or test results that verify quality standards.
Load Capacity and Safety
- Load Ratings: Each panel has a rated load capacity; verify that the grating can bear the expected traffic and weight loads.
- Fire Retardance: For settings where fire safety is critical, opt for fiberglass grating formulated with fire-retardant additives.
- Slip Resistance: A grit top surface can enhance traction, reducing slip-and-fall incidents, which are a leading cause of workplace injuries.
Surface Types
Fiberglass floor grating comes in different surface finishes:
- Gritted Surface: Offers excellent slip resistance, suitable for wet or oily conditions.
- Concave Surface: Provides moderate traction for relatively dry, low-risk areas.
- Covered or Solid Top: Ideal for environments that require a closed surface to prevent spillage or protect underlying space.
Installation Best Practices
Proper Planning
Before purchasing wholesale fiberglass floor grating, assess the site’s structural requirements. Take accurate measurements and account for any obstacles like pipes, drains, or equipment that might affect panel placement. Planning ahead can save you time and money by avoiding material waste.
Tools and Techniques
- Measuring and Cutting: Standard cutting tools (such as a circular saw with a diamond blade) can easily trim fiberglass grating to fit specific areas.
- Support Structure: Ensure support beams or frames are sturdy enough to handle the load, spacing the supports according to manufacturer recommendations.
- Fasteners and Clips: Use corrosion-resistant clips and bolts to keep gratings securely in place while maintaining easy removal when necessary.
Here’s a quick checklist for installation:
- Double-check all measurements for accuracy.
- Mark cutting lines clearly on the grating before slicing.
- Wear safety goggles and masks, as fiberglass dust can be irritating.
- Verify alignment and levelness after each panel is placed.
Common Pitfalls
- Overlooking Safety Gear: Protective equipment is crucial when cutting or handling fiberglass.
- Ignoring Manufacturer Guidelines: Each grating type has specific spacing and installation instructions. Failing to follow them can compromise structural integrity.
- Inadequate Ventilation: Fiberglass dust can become airborne; ensure proper ventilation or work outdoors.
Maintenance and Longevity
Cleaning
One of the main advantages of wholesale fiberglass floor grating is its low-maintenance nature. Still, occasional cleaning helps maintain a professional appearance and peak performance:
- Regular Hosing or Pressure Washing: Removes debris and prevents buildup.
- Mild Detergent Solutions: For stubborn grime or oil stains.
Repairs and Replacements
Fiberglass grating is highly durable, but accidents can happen. If you notice cracks or significant damage:
- Sectional Repairs: Small damaged areas can sometimes be cut out and replaced with new material.
- Entire Panel Replacement: If a large portion of the grating is compromised, swapping out the panel might be the safer long-term solution.
Dealing with Environmental Factors
- UV Exposure: Some fiberglass grating is UV-stabilized, but ongoing exposure to direct sunlight can eventually cause discoloration. Choose UV-resistant resin if prolonged sun exposure is expected.
- Extreme Temperatures: Fiberglass can handle a wide temperature range, but always confirm the product’s thermal limits with your supplier for best results.
Conclusion
Wholesale fiberglass floor grating offers an affordable, durable, and versatile solution for various industrial, commercial, and even public applications. By understanding its composition, benefits, and essential selection criteria, you can make an informed decision tailored to your specific needs. Proper installation and routine maintenance further extend its lifespan, providing a high return on investment.
Call to Action: Ready to explore options for your next project? Share your thoughts and questions in the comments below. Don’t forget to subscribe to our newsletter for the latest insights on industrial materials, expert tips, and exclusive product deals!