Introduction
When it comes to industrial and commercial applications, the right choice of flooring and platform materials can make all the difference. GRP (Glass Reinforced Plastic) grating has become a popular solution due to its many advantages, including corrosion resistance, lightweight properties, and ease of installation. But with so many options available, how do you choose the right GRP grating for your specific project? Understanding GRP grating specifications is crucial for making an informed decision that will ensure optimal performance and safety.
What is GRP Grating?
GRP grating is a strong, durable material composed of fiberglass and resin, making it resistant to many of the harsh conditions typically faced by industrial surfaces. Unlike traditional materials such as steel or aluminum, GRP grating offers a unique combination of strength and flexibility, with superior resistance to corrosion, UV damage, and chemicals.
GRP gratings are commonly used in sectors like oil and gas, wastewater treatment, chemical processing, and even marine applications. Their high strength-to-weight ratio and excellent resistance to environmental factors make them ideal for platforms, walkways, drainage covers, and other applications.
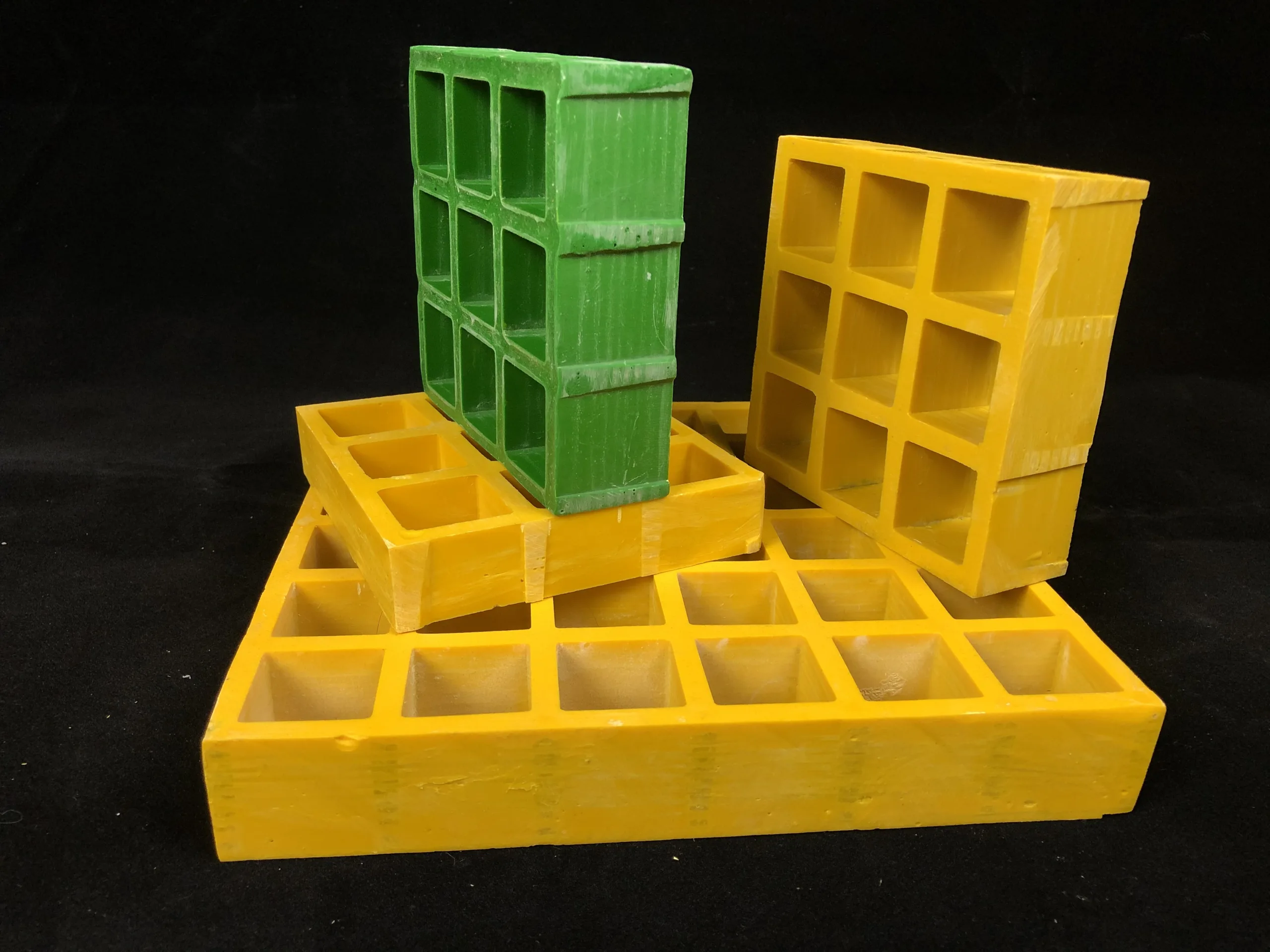
grp grating specification
Key GRP Grating Specifications to Consider
1. Load-Bearing Capacity
One of the most important specifications to consider when selecting GRP grating is its load-bearing capacity. Depending on the intended use, you may need grating that can handle light foot traffic or heavy-duty industrial equipment. Each type of GRP grating is rated for specific load requirements, and selecting the correct one is crucial for ensuring safety and long-term performance.
- Light-duty gratings are typically used in areas with minimal load, such as pedestrian walkways.
- Heavy-duty gratings are designed for high-load environments, such as industrial machinery platforms or high-traffic areas.
2. Size and Dimensions
The size and dimensions of the GRP grating will largely depend on your project’s layout and requirements. GRP gratings are available in standard sizes but can also be custom-made to suit specific needs.
- Standard grating sizes typically range from 1-meter by 1-meter panels to larger custom sizes.
- Custom dimensions are ideal for applications that require tailored fitments or unusual shapes.
3. Surface Finish and Non-Slip Properties
Safety is a top priority in many industrial environments, and one of the key safety features of GRP grating is its non-slip surface. Most GRP gratings come with textured or grooved surfaces designed to reduce the risk of slips, especially in wet or oily conditions.
- Anti-slip properties can be further enhanced by selecting gratings with additional surface coatings or grids.
- For applications exposed to wet conditions (like walkways on ships or platforms in chemical plants), ensuring a high degree of slip resistance is essential.
4. Chemical Resistance and Durability
One of the standout features of GRP grating is its excellent resistance to chemicals and extreme environmental conditions. GRP grating is resistant to corrosion, making it an excellent choice for applications in industries such as wastewater treatment, food processing, or chemical manufacturing.
- GRP grating is resistant to a wide range of chemicals, including acids, alkalis, and solvents.
- It also resists UV degradation, making it ideal for outdoor applications where prolonged exposure to the sun is a concern.
Choosing the Right GRP Grating for Your Project
Selecting the correct GRP grating for your project is not just about specifications—it’s about matching those specifications to your project’s unique needs. Here are some factors to keep in mind:
- Environmental Conditions: Will the grating be used outdoors or in an area exposed to chemicals? Choose a type that can withstand the specific conditions of your site.
- Load Requirements: Assess the amount of traffic or equipment weight the grating will need to support. This is especially important in industrial or commercial environments.
- Budget: While GRP grating offers long-term value, it’s important to balance quality and cost. Customization options may add to the price, so assess your project’s needs carefully.
Benefits of GRP Grating
Choosing GRP grating over traditional materials like steel or aluminum offers numerous benefits. Its corrosion resistance makes it an excellent choice for industries that deal with harsh chemicals, moisture, or salty air. Furthermore, GRP grating is lightweight and easy to install, reducing labor costs and time on site.
- Corrosion Resistance: Ideal for industries such as chemical processing, marine, and wastewater management.
- Lightweight: Easier and faster to transport and install, saving on costs.
- Low Maintenance: Unlike metal gratings that may require frequent maintenance due to rust and corrosion, GRP grating requires minimal upkeep.
Conclusion
Understanding GRP grating specifications is the key to selecting the right material for your project. From load-bearing capacity and surface finishes to chemical resistance and durability, every specification plays a critical role in the overall performance of the grating. By considering these factors, you can ensure your project has the right GRP grating solution that meets both safety and functional requirements.
If you need assistance in choosing the right GRP grating for your next project, feel free to reach out for expert guidance and custom solutions tailored to your needs.