Introduction
Molded fiberglass reinforced plastic grating—often referred to simply as molded FRP grating—is a modern solution that addresses many of the shortcomings found in traditional metal or wood alternatives. Whether you’re looking for a platform material in a chemical plant or a slip-resistant walkway in a marine environment, molded FRP grating is gaining popularity for its durability, corrosion resistance, and low maintenance requirements. In this article, we’ll answer some of the top questions about molded fiberglass reinforced plastic grating, helping you make an informed decision for your next project.
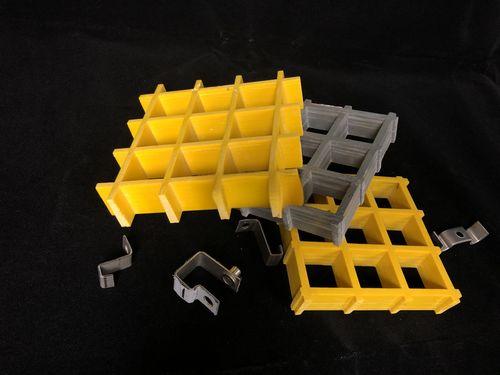
molded fiberglass reinforced plastic grating
What Is Molded Fiberglass Reinforced Plastic Grating?
Composition and Manufacturing
Molded FRP grating consists of a matrix of fiberglass strands and a thermoset resin, typically polyester or vinyl ester. During the manufacturing process, fiberglass is layered in a mold, and resin is poured to form a single, solid panel. This creates a seamless, square or rectangular mesh pattern that offers a uniform load distribution.
- Fiberglass Strands: Provide the structural backbone and tensile strength.
- Resin: Offers chemical resistance and binds the fiberglass together for overall rigidity.
- Molded Structure: Unlike pultruded grating, molded FRP grating is created in a single piece, resulting in a solid, corrosion-resistant panel.
Key Advantages
- High Strength-to-Weight Ratio: Lighter than metal, yet capable of supporting considerable loads.
- Non-Conductive Surface: Enhances safety in electrical or high-voltage areas.
- Slip Resistance: The gritted top surface reduces the risk of slips and falls.
A study by the American Composites Manufacturers Association (ACMA) found that fiberglass-reinforced plastics can outperform traditional materials in terms of corrosion resistance, making them ideal for challenging environments.
Why Choose Molded Fiberglass Reinforced Plastic Grating Over Other Materials?
Corrosion Resistance and Durability
One of the primary reasons to opt for molded fiberglass reinforced plastic grating is its exceptional resistance to corrosion. Metal grates often rust over time, especially in environments exposed to saltwater or chemical agents. In contrast, molded FRP grating resists corrosion, rotting, and warping, making it a long-lasting choice even in harsh settings.
- Saltwater and Coastal Environments: The resin used in molded FRP can withstand ongoing exposure to saline conditions without deteriorating.
- Chemical Facilities: Ideal for acid tanks, wastewater treatment plants, and chemical-processing units due to their capacity to handle corrosive fumes and spills.
Cost-Effectiveness and Maintenance
While the initial cost of molded FRP grating can sometimes be higher than a basic steel solution, the lifecycle savings are significant:
- Reduced Replacement Costs: Longer service life cuts down on frequent replacements.
- Minimal Upkeep: Cleaning typically involves simple pressure washing or rinsing with water.
- Lower Man-Hour Costs: No painting, galvanizing, or specialized labor needed after installation.
When you factor in the reduced downtime, labor, and replacement expenses, molded FRP grating often proves more economical over the life of the product compared to steel or wood alternatives.
Top Applications Across Industries
Industrial Settings
Molded fiberglass reinforced plastic grating is widely used in facilities such as:
- Chemical Plants: Platforms and walkways that require non-corrosive, slip-resistant surfaces.
- Food and Beverage Processing: Areas needing hygienic and easy-to-clean flooring solutions.
- Oil and Gas Rigs: Decking that can endure exposure to harsh chemicals and salt spray.
Marine and Coastal Areas
Due to its superior performance against saltwater and humidity, molded FRP grating is an excellent choice for:
- Marinas and Docks: Safe, slip-resistant walkways for boaters.
- Boardwalks: Long-lasting, corrosion-resistant paths in oceanfront parks or beaches.
- Offshore Platforms: Durable, lightweight grating for utility platforms in demanding ocean environments.
Public Infrastructure and Commercial Spaces
Municipalities and commercial property owners are increasingly turning to molded FRP grating for:
- Pedestrian Bridges: Lighter construction material that reduces load on supporting structures.
- Stormwater Management Systems: Corrosion-proof covers for drains and channels.
- Aesthetic Walkways: Vibrant, color-stable options that maintain visual appeal.
Frequently Asked Questions
How Does Molded FRP Grating Differ from Pultruded FRP Grating?
- Manufacturing Method: Molded FRP is created in a single-step molding process, whereas pultruded grating involves pulling continuous fiberglass strands through a resin bath and then curing them.
- Structural Layout: Molded FRP has an evenly distributed mesh for multi-directional strength, while pultruded grating typically has load bars oriented in one primary direction.
- Applications: Molded FRP grating excels in high-corrosion areas needing multi-directional load support, whereas pultruded grating is often preferred where higher load capacity along one direction is crucial.
What Is the Expected Lifespan of Molded FRP Grating?
When properly installed and maintained, molded FRP grating can last for decades—20 years or more is common. Its rust-resistant and non-degrading properties make it an investment that pays off in reduced repair and replacement costs over time. For instance, a facility study by a major chemical plant reported that molded FRP grating installed in a highly corrosive environment was still functional and structurally sound after 25 years.
How Do I Ensure Proper Installation?
- Accurate Measurements: Verify that all support structures are in the correct positions.
- Use Recommended Fasteners: Stainless steel or FRP clips designed for molded grating are recommended.
- Follow Manufacturer Guidelines: Reference specific load deflection charts to ensure you’re spacing supports correctly.
Proper installation not only prevents potential accidents but also maximizes the grating’s life expectancy.
What Is the Best Way to Clean and Maintain Molded FRP Grating?
- Routine Rinsing: Simple water spraying to remove dirt, debris, or chemical residues.
- Mild Detergents: Gentle cleaning agents help eliminate grease or grime build-up.
- Visual Checks: Inspect for any signs of damage, especially around edges, and address them promptly.
Because molded FRP grating doesn’t require painting or special coatings, regular inspection and basic cleaning are generally all that’s needed.
Conclusion
Molded fiberglass reinforced plastic grating stands out as a versatile, long-lasting, and low-maintenance solution for modern building and infrastructure needs. From harsh chemical environments to coastal boardwalks, its corrosion resistance, lightweight design, and slip-resistant surface make it a worthwhile investment in any application. Understanding its composition, benefits, and maintenance ensures you’ll get the most value for your money—whether you’re replacing aging steel grates or constructing a new facility from the ground up.
Call to Action (CTA)
Have any experiences or questions about molded fiberglass reinforced plastic grating? Join the conversation by commenting below! If you found this article helpful, please share it with others who might benefit. For more insights and tips on selecting the right grating solutions, subscribe to our newsletter and never miss an update.