Introduction
When it comes to construction, the materials used are vital for ensuring the longevity and durability of the structure. Traditional steel rebar has been the standard choice for reinforcement, but in recent years, fiberglass rebar has emerged as a compelling alternative. In this comprehensive guide, Unicomposite composite profiles will delve into Kodiak fiberglass rebar, exploring its numerous benefits, various applications, and essential installation tips.
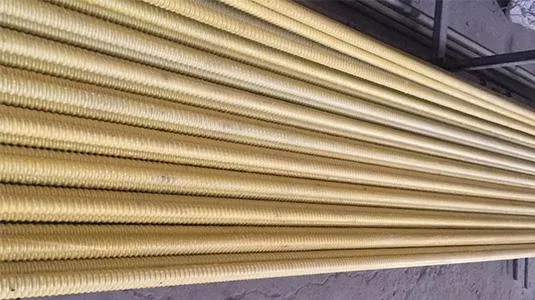
liteform fiberglass rebar
1. What is Kodiak Fiberglass Rebar?
Kodiak fiberglass rebar is a high-strength, lightweight composite material made from glass fibers and a resin matrix. It is designed to replace traditional steel rebar in reinforced concrete applications, providing superior performance in various environmental conditions.
2. The Advantages of Kodiak Fiberglass Rebar
- Corrosion Resistance: Unlike steel rebar, Kodiak fiberglass rebar does not rust or corrode, making it an ideal choice for marine and coastal structures.
- High Strength-to-Weight Ratio: Despite being lightweight, fiberglass rebar offers exceptional strength, making it easier to handle during installation while providing robust reinforcement.
- Non-Conductive: Fiberglass rebar is non-conductive, making it a safer option in areas with electrical considerations.
- Dimensional Stability: Kodiak fiberglass rebar exhibits minimal thermal expansion and contraction, ensuring the stability of the reinforced concrete structure over time.
- Chemical Resistance: It is highly resistant to chemicals and alkalis, making it suitable for use in aggressive environments.
- Low Maintenance: Structures reinforced with fiberglass rebar require less maintenance over their lifetime, reducing long-term costs.
3. Applications of Kodiak Fiberglass Rebar
Kodiak fiberglass rebar finds applications in various construction projects, including:
- Transport Infrastructure: Bridges, highways, and tunnels benefit from the corrosion resistance of fiberglass rebar, especially in regions with harsh weather conditions and de-icing salts.
- Marine Structures: Wharfs, piers, and seawalls benefit from the non-corrosive properties of Kodiak fiberglass rebar in saltwater environments.
- Buildings and Foundations: Fiberglass rebar is used in commercial and residential buildings, providing durability and longevity to concrete structures.
- Water Treatment Facilities: Chemical resistance makes it suitable for wastewater treatment plants and water reservoirs.
- Mining and Tunneling: In mining operations and tunnel construction, fiberglass rebar proves valuable due to its non-magnetic and non-corrosive nature.
4. Preparing for Kodiak Fiberglass Rebar Installation
Before commencing the installation process, certain preparatory steps are essential:
- Engineering Design: Collaborate with structural engineers to determine the appropriate diameter and spacing of the fiberglass rebar for the specific project requirements.
- Surface Preparation: Ensure the concrete surface is clean, free from debris, and adequately compacted before placing the fiberglass rebar.
- Storage and Handling: Store the fiberglass rebar in a dry, covered area and handle it with care to avoid damage.
5. Installation Process Step-by-Step
The installation of Kodiak fiberglass rebar follows these general steps:
- Placement: Lay the fiberglass rebar according to the engineering design, securing it in the correct position within the formwork.
- Tying and Overlapping: Use ties and overlaps as specified in the design to create a continuous and interconnected reinforcement network.
- Pouring Concrete: Once the rebar is in place, pour the concrete into the formwork, ensuring it completely covers and encases the fiberglass rebar.
6. Tips for Successful Installation
- Avoid Sharp Bends: Minimize sharp bends in the fiberglass rebar to prevent stress concentration points.
- Use Proper Cutting Tools: Employ appropriate tools to cut fiberglass rebar, ensuring clean edges without fraying.
- Maintain Concrete Quality: Use high-quality concrete with the right mix design to ensure optimal bonding with the fiberglass rebar.
7. Comparing Kodiak Fiberglass Rebar to Traditional Steel Rebar
- Weight: Kodiak fiberglass rebar is significantly lighter than steel rebar, making it easier to transport and handle on construction sites.
- Corrosion Resistance: Unlike steel, fiberglass rebar does not corrode, enhancing the longevity and durability of the reinforced concrete.
- Electrical Conductivity: Fiberglass rebar is non-conductive, making it a safer choice in electrical-sensitive applications.
- Thermal Conductivity: Steel rebar has higher thermal conductivity, making it more susceptible to temperature-induced expansion and contraction.
8. Environmental Impact of Kodiak Fiberglass Rebar
Kodiak fiberglass rebar is an eco-friendly alternative to traditional steel rebar:
- Lower Carbon Footprint: The production of fiberglass rebar results in lower carbon emissions compared to steel rebar.
- Recyclability: Fiberglass rebar can be recycled, further reducing its environmental impact.
9. Maintaining Structures Reinforced with Kodiak Fiberglass Rebar
Maintaining structures reinforced with fiberglass rebar is relatively straightforward:
- Regular Inspections: Periodically inspect the reinforced concrete for any signs of damage or deterioration.
- Prompt Repairs: Address any issues promptly to prevent minor damages from escalating.
10. Addressing Common Concerns about Kodiak Fiberglass Rebar
- Is Kodiak fiberglass rebar more expensive than steel rebar?
- Initially, fiberglass rebar may have a higher upfront cost, but its long-term benefits can offset the initial investment.
- Can Kodiak fiberglass rebar replace steel rebar entirely?
- While it is an excellent alternative, in certain applications, steel rebar may still be preferred due to specific project requirements.
- Does fiberglass rebar weaken over time?
- No, Kodiak fiberglass rebar maintains its strength and integrity over time.
- Can fiberglass rebar be used in seismic-prone regions?
- Yes, fiberglass rebar has been successfully used in seismic zones due to its high strength and durability.
- Is Kodiak fiberglass rebar resistant to UV rays?
- Yes, fiberglass rebar is UV-resistant, making it suitable for outdoor applications.
Conclusion
Kodiak fiberglass rebar is revolutionizing the construction industry with its remarkable properties and advantages over traditional steel rebar. Its corrosion resistance, high strength-to-weight ratio, and non-conductive nature make it a preferred choice for a wide range of applications.