Introduction
Building a canoe with a fiberglass mold opens up endless possibilities for water enthusiasts, allowing them to craft durable, lightweight, and fully customized canoes. Fiberglass canoe molds have revolutionized the canoe-building process, making it more accessible to both professionals and DIY hobbyists. Whether you’re interested in learning the process as a new skill or you’re an experienced builder seeking to refine your techniques, this guide provides you with everything you need to know about using fiberglass molds, from preparation to finishing touches.
This article will delve into the essential steps, materials, and techniques for working with fiberglass canoe molds, offering expert insights to help you achieve a high-quality, professional canoe. Let’s dive in!
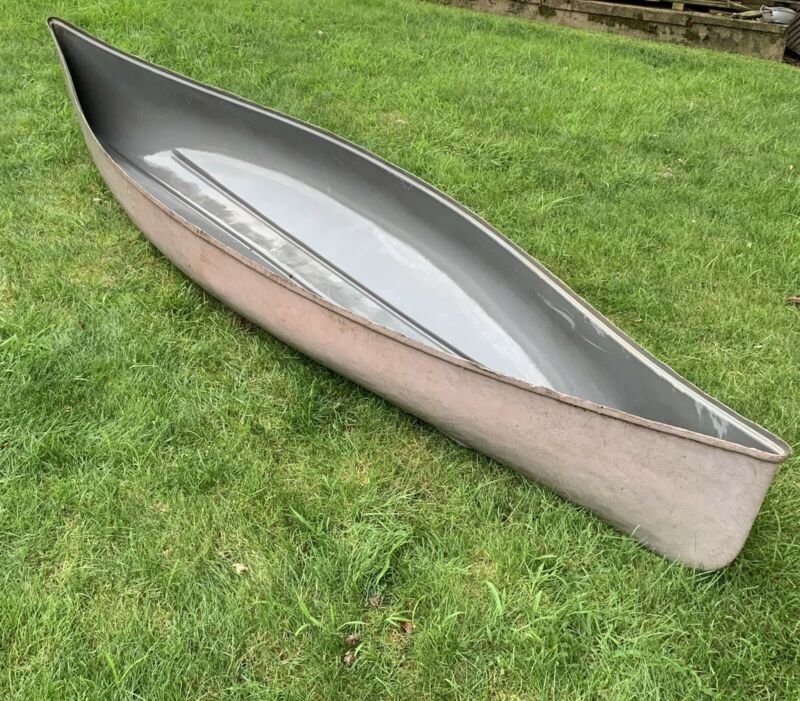
fiberglass canoe mold
What is a Fiberglass Canoe Mold?
Understanding the Basics
A fiberglass canoe mold is a reusable, three-dimensional form that serves as the template for shaping a canoe out of fiberglass layers. These molds are typically designed to match specific canoe shapes and dimensions, enabling builders to replicate a consistent canoe shape each time they build. Unlike wooden or metal canoes, fiberglass canoes offer a unique combination of flexibility, strength, and weight reduction.
Benefits of Using Fiberglass Molds
- Consistency in Shape – Fiberglass molds ensure that each canoe has the same shape, which is especially valuable for uniformity in mass production or consistent DIY results.
- Lightweight Yet Durable – Fiberglass canoes are lighter than metal or wooden canoes, while remaining strong enough for rough waters.
- Sleek and Smooth Finish – Fiberglass molds produce a smooth, streamlined exterior, enhancing water resistance and improving the canoe’s speed and performance.
Types of Fiberglass Molds for Canoes
Fiberglass canoe molds come in various designs, including molds for recreational canoes, racing canoes, and touring canoes. Each type has unique features that affect how it performs on the water. For example:
- Recreational Canoe Molds – Typically wider, stable, and ideal for beginners.
- Touring Canoe Molds – Longer and slimmer, designed for speed and efficiency over long distances.
- Racing Canoe Molds – Streamlined with specific hydrodynamic shapes for speed and agility in competition.
Materials and Tools Needed for Building a Canoe with Fiberglass Molds
Essential Materials
- Fiberglass Cloth – The main structural component, available in different weights and weaves depending on the strength requirements.
- Resin (Epoxy or Polyester) – Used to bind the fiberglass cloth layers together.
- Mold Release Agent – Ensures that the finished canoe easily separates from the mold.
- Gel Coat – The outermost layer that adds durability and a smooth finish.
- Catalyst/Hardener – Speeds up the resin curing process.
Required Tools and Equipment
- Rollers and Brushes – For applying resin and removing air bubbles from the fiberglass layers.
- Mixing Containers and Stirrers – Essential for preparing resin mixtures.
- Sanders and Buffers – Used for finishing and polishing the canoe’s surface.
- Protective Gear – Safety goggles, gloves, and masks are necessary due to the fumes and sharp fiberglass particles.
- Measuring Tools – Calipers, measuring tapes, and rulers to ensure accuracy in layering and application.
Preparing Your Workspace for Mold Fabrication
Choosing the Right Location
Building a canoe with a fiberglass mold requires a well-ventilated, spacious, and clean environment. Look for a workspace where:
- Airflow can prevent fumes from accumulating.
- The temperature is consistent to avoid affecting resin curing.
- Dust and dirt are minimized to prevent flaws in the gel coat.
Setting Up for Safety
Safety is crucial when working with fiberglass and resin due to potential health risks. Key safety steps include:
- Ventilation – Using a fan or open windows to allow fresh air.
- Personal Protection – Wearing protective gloves, goggles, and a mask to avoid inhaling dust or fumes.
- Cleanliness – Keeping tools and surfaces clean to avoid contamination of the fiberglass layers.
Step-by-Step Guide to Using a Fiberglass Canoe Mold
Step 1: Preparing the Mold
Start by thoroughly cleaning the mold to remove dust, dirt, and any previous resin residues. Once cleaned, apply a mold release agent evenly across the surface. This will prevent the finished canoe from sticking, making removal easier after curing.
Step 2: Laying the Gel Coat
The gel coat is applied as the first layer inside the mold to provide a smooth, durable exterior for the canoe. Using a brush or spray gun, apply the gel coat evenly. It should be thick enough to withstand water exposure but thin enough to prevent cracking during curing. Allow it to set until tacky before proceeding.
Step 3: Laying the Fiberglass Layers
- Cutting and Placing the Fiberglass Cloth – Cut pieces of fiberglass cloth to fit the shape of the mold, ensuring enough overlap at seams.
- Applying Resin – Mix and apply resin with a roller or brush, saturating each layer of fiberglass cloth and ensuring all air bubbles are removed.
- Layering for Strength – Add successive layers of fiberglass cloth and resin, allowing each layer to partially cure before adding the next.
Step 4: Finishing Touches
Once the final layer is applied and fully cured, carefully trim excess fiberglass with a fine blade. Sand the surface to achieve a smooth finish, paying special attention to edges and seams. Buff the gel coat to a shine for a professional look.
Common Issues in Fiberglass Canoe Mold Work and How to Fix Them
Bubbles and Air Pockets
Air bubbles can compromise the canoe’s strength and appearance. To prevent bubbles:
- Use a bubble roller to press down the fiberglass layers.
- Work in small sections and apply resin evenly.
Deformations and Warping
Warping often occurs if layers cure unevenly. Ensure:
- Consistent layering and curing times.
- Maintain a stable temperature in your workspace to avoid resin shrinkage.
Uneven Gel Coat Application
If the gel coat is uneven, sand the surface gently and reapply a thin layer. This will correct imperfections and provide a smooth finish.
Tips for Successful Canoe Mold Building
Layering Techniques for Strength
For added durability, consider using a combination of heavy and light fiberglass cloth layers. The heavy cloth adds strength, while the light layers ensure flexibility.
Timing and Curing Tips
Allow each layer of fiberglass and resin to partially cure before adding the next. This technique enhances adhesion and overall strength.
Choosing the Right Resin and Gel Coat
Selecting a high-quality resin and gel coat is essential for durability. Epoxy resins offer excellent strength and water resistance, while polyester resins are more affordable and can work well in milder conditions.
Maintaining Your Fiberglass Canoe Mold
Cleaning and Storing the Mold
After each use, clean the mold thoroughly with soap and water to remove any leftover resin. Avoid harsh chemicals that can wear down the mold surface.
Mold Repair and Maintenance Tips
Inspect the mold regularly for cracks or wear. Small repairs can be made using a mold repair kit, ensuring the mold remains in top condition for future projects.
Cost of Building a Canoe Using a Fiberglass Mold
Material Costs
Fiberglass cloth, resin, and gel coat are typically the largest expenses. These materials vary in price based on quality and quantity, with an average project cost ranging between $200 and $500.
Tool and Equipment Costs
Tools like rollers, sanders, and safety gear add another $100 to $300 to the project budget, depending on whether tools are purchased or rented.
Time and Labor Considerations
Building a fiberglass canoe typically takes several days to a few weeks, depending on skill level and project complexity. Factor in the time for curing and finishing touches to set realistic expectations.
Comparing DIY Fiberglass Canoe Molding to Purchasing a Canoe
Advantages of DIY Canoe Molding
Building a canoe allows for customization in shape, size, and aesthetics. It also provides satisfaction and potentially saves money compared to purchasing a pre-made canoe.
When Buying Might Be a Better Choice
In some cases, buying a canoe may be more practical if you have limited time or access to the required tools and materials.
Frequently Asked Questions About Fiberglass Canoe Molds
Q1: How long does it take for resin to cure?
Most resins cure within 24-48 hours, though some may take longer depending on temperature and humidity.
Q2: Can I use any type of fiberglass cloth?
Different fiberglass weights and weaves suit different canoe parts; choose based on durability and flexibility requirements.
Q3: How do I prevent my canoe from sticking to the mold?
Use a mold release agent, applied evenly before layering resin and fiberglass.
Q4: Is epoxy or polyester resin better for canoe building?
Epoxy is generally more durable and water-resistant, while polyester is affordable and may suit light use.
Q5: How many layers of fiberglass are needed?
Three to five layers are standard, with additional layers in high-stress areas.
Q6: What is the best temperature for curing resin?
Ideal curing temperatures range between 70°F to 85°F to ensure even curing.
Conclusion
Crafting a canoe using a fiberglass mold is a rewarding project that combines skill, patience, and creativity. This process allows for complete customization and produces a durable, sleek canoe perfect for water adventures. With the right materials, careful preparation, and attention to technique, you can build a high-quality fiberglass canoe to enjoy for years. Ready to get started? Dive in and begin your canoe-building journey today!