There are some problems during pultrusion production, such as mold blockage, profiles bend and color difference, today we’ll introduce measures of those problems.
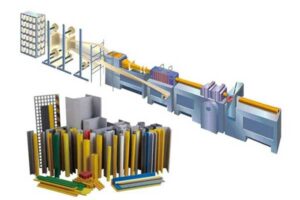
Pultrusion production
Mold Blockage
The pultrusion mold is blocked by the fiberglass roving will cause the parts in the mold break out
Measure:
Reduce the temperature of the mold, and the pre – curing at the entrance of the mold can cause the blockage
Roving goes through each plastic guide evenly, and in shaping guiding no fiber breakage or distorted occurred. Only in this way, it can be made acceptable preshaped reduced to strengthen the level. In a given position, only a limited number of fibers can be placed. If you pull out multiple cavities, please check to make sure that all ends are in the correct cavity.
Check the surface of mold. The cut in the inner mold will eventually lead to the part break out. Even though such situation may be in the form of a plug, but in fact, it will lead to the failure of the component. Too rough (worn) mold surfaces may cause the same problem.
Bend
Fiberglass profiles bend after pultrusion process from the mold because of cooling
Measure:
Check whether the symmetric reinforcement mode was used, especially in the case of a liner, uneven distribution of glass fiber, to strengthen the adjustment to offset part bending twisting.
Check whether the symmetrical heat model was used; the uneven heating leads to uneven curing rate, and results in different shrinkage rate.
Check component design. Some asymmetric designs may cause bending. If this is the reason, it may be necessary to use cooling device.
Color Difference
Heating points will lead to uneven shrinkage and the color difference (also known as color transfer)
Measure:
Check the heater to make sure it is in the right place so that it will not result in uneven temperature in the mold. Check the resin mixture to ensure that the filler and / or pigment will not settle or separate(FRP profiles color difference).