1. Introduction to the pultrusion process
The pultrusion process refers to a method of continuous production of FRP products through dipping, extrusion molding, heating and curing, and fixed-length cutting of prepreg tapes, fibers, or fabrics under external traction.
It is characterized in that the prepreg tape, dipped fiber, or fabric is drawn by an external force, and then extruded through the heating mold to form and solidify to form an FRP wire profile, which is used to produce composite products with a fixed cross-sectional shape.
Advantage:
- The mechanical properties of the product are excellent, especially the longitudinal strength.
- The technological process is automatically controlled and the quality is stable.
- There is no corner waste, and the effective utilization rate of raw materials is high.
- Continuous production, unlimited product length.
- Resin-impregnated areas can be enclosed to limit volatile emissions.
Shortcoming:
- limited to constant sections.
- The cost of mold and heating is relatively high, and it is difficult to recover the cost due to less output.
2. Reinforcing material
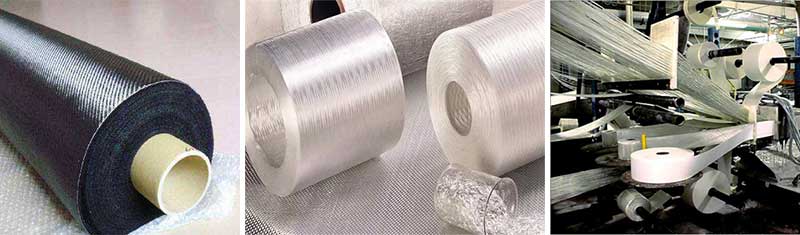
Prepreg tape Fiber and Fabric
Prepreg tape:
- Carbon fiber prepreg tape
- Glass fiber prepreg tape
Fiber:
- Carbon Fiber: 12K, 24K, 48K
- Glass fiber (usually direct yarn): 1200Tex, 2400Tex, 4800Tex, 9600Tex…
Fabric:
- Chopped strand mat
- Stitched felt
- Fiber cloth
- Surface felt
3. Matrix material
Common resins:
- Epoxy resin
- Epoxy vinyl ester resin
- Unsaturated polyester resin
- Polyurethane resin
The role of the base material:
The reinforcing material is bonded into a whole, which plays the role of transmitting and balancing the load. Endow composite materials with basic properties:
- Tensile properties: depends on the reinforcing material;
- Bending, compressive properties: partly depends on the base material;
- Interlaminar shear performance: depends on the matrix material;
- Functionality such as heat resistance, corrosion resistance, flame retardancy, weather resistance, electrical properties, biological properties, and light transmission: depends on the base material.
Basic requirements for base material:
- Low viscosity: below 1000mPa·s in the production environment, the resin should have good fluidity and wettability.
- Longer gel time, shorter cure time, high activity, and low exotherm.
- Low cure shrinkage: Fillers can be introduced into the formulation to reduce the cure shrinkage and at the same time reduce costs.
- It has good adhesion and certain toughness and is not prone to cracks during molding.
4. Curing System
Epoxy curing system
Epoxy-curing agents are mainly acid anhydrides
The supplier provides (A+B) two-component or (A+B+C) three-component formula material, no need for a third party to provide it.
Polyurethane curing system
Suppliers provide A+B two-component formulations without the need for a third party to provide them.
Epoxy vinyl ester resin, unsaturated polyester resin
Usually, two or three initiators are added
5. Demoulding system
- Epoxy: INT-1846N INT-1890M
- Epoxy vinyl ester resin, unsaturated polyester resin: INT-PS125 INT-PUL524M Zinc stearate (commonly used)
- Amount of release agent added: Initial addition amount: 1%, Effective dosage: 0.75-2%.
6. Fillers and Additives
Inorganic fillers:
- Purpose: Reduce cost, reduce shrinkage, improve flame retardancy
- Commonly used: calcium carbonate, aluminum hydroxide
- Particle size: 150-1200 mesh
- Addition amount: 10%-50% of resin
Organic Fillers: color paste, toner, thinner, etc.
Auxiliary: toughening agent, etc.
7. Mold system
Pre-forming mold: The function is to gradually form a pre-formed body similar to the shape and size of the molding cavity according to the configuration of the profile section, and then enter the molding mold, which can ensure that the yarn content of the product section is uniform.
Forming mold:
- Die length: 500~1500 mm
- Mold material: mold steel
- Mold form: integral, combined
- Heating device: electric hot plate, electric wave heating, hot oil circulation
8. About Unicomposite
Unicomposite builds its own professional team including engineers, designers, and QC to make sure that we can provide the standard fiberglass pultrusion profiles as well as design, consult and produce custom products or provide solutions for FRP projects. Also, Unicomposite provides technical guidance on FRP industries for those customers who want to set up their own pultrusion production lines.