Introduction
Choosing the right composite material can make or break your project’s budget, performance, and longevity. Pultruded fiberglass vs FRP is a frequent debate among engineers, purchasing managers, and contractors. This guide demystifies both options, comparing cost, strength, durability, and practical installation factors so you can specify with confidence.
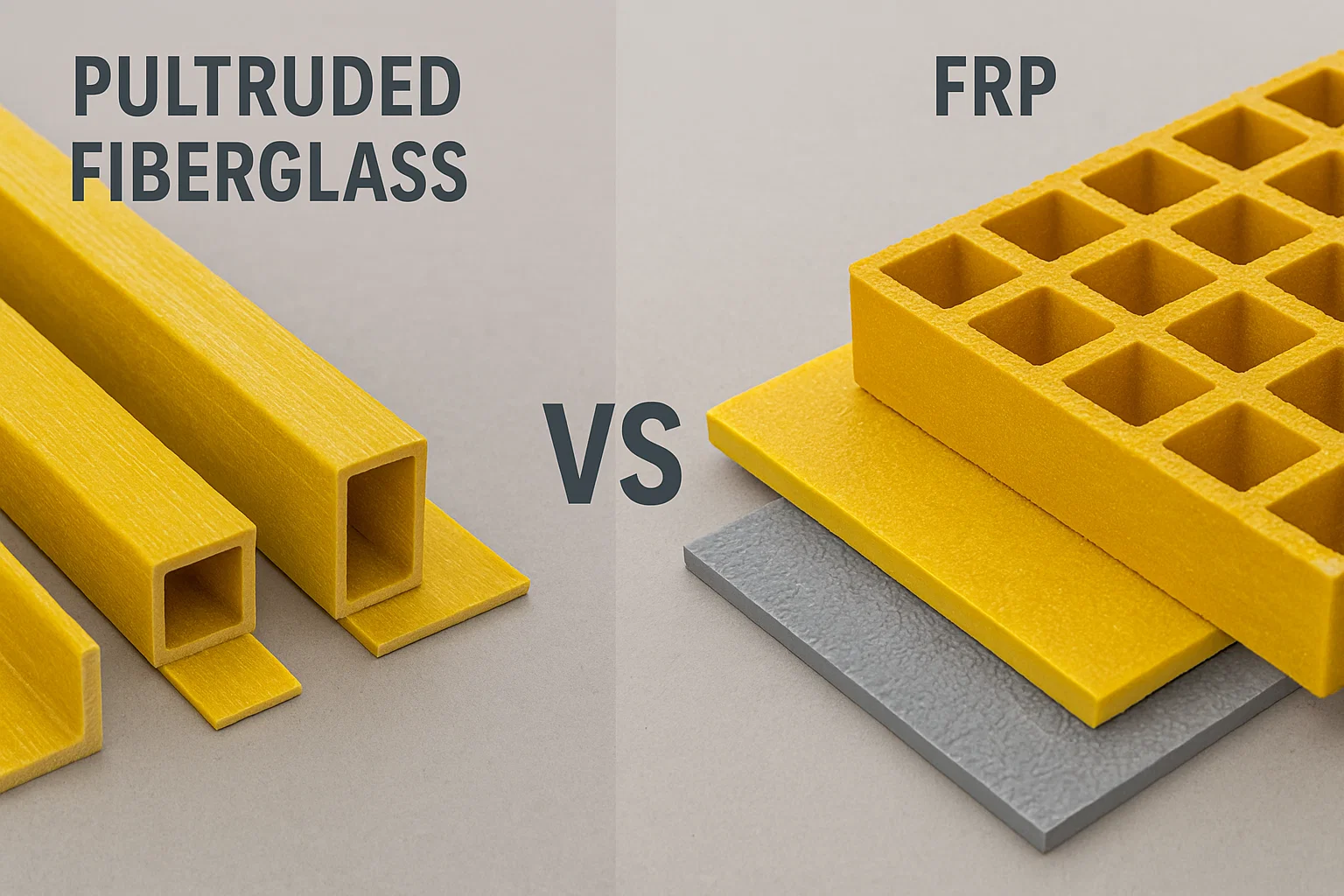
pultruded fiberglass vs frp
What Are Pultruded Fiberglass and FRP?
Defining FRP
Fiber-reinforced polymer (FRP) is a broad category of composites made by combining glass, carbon, or aramid fibers with a thermoset resin such as polyester, vinyl ester, or epoxy. Typical manufacturing methods include hand-lay-up, spray-up, filament winding, and vacuum infusion. FRP panels and molded gratings are common end products.
The Pultrusion Process
Pultrusion is a continuous, automated process in which roving strands of fiberglass are pulled through a resin bath and heated die to create straight, constant-profile shapes—think I-beams, angles, and tubes. The result: pultruded fiberglass profiles with precise fiber alignment and consistent resin content, delivering high mechanical properties in long lengths.
“Pultrusion provides unmatched consistency because every linear inch sees the same resin content and fiber alignment,” notes Dr. Jane Smith, composites researcher at Oak Ridge National Laboratory.
Cost Comparison: Initial Price vs Lifecycle Value
Cost Factor | Pultruded Fiberglass | Conventional FRP Panels |
---|---|---|
Initial material price | Slightly higher per pound | Moderate |
Fabrication waste | Minimal (continuous process) | Higher (trim & off-cuts) |
Installation labor | 15–25 % faster due to precise dimensions | Variable |
Maintenance | Low; profiles retain shape | Depends on environment |
A 2024 study by the American Composites Manufacturers Association found that pultruded profiles trimmed total installed cost by up to 35 % on pedestrian bridges longer than 6 m thanks to lower labor and minimal rework.
Strength & Mechanical Performance
Tensile & Flexural Properties
Pultruded fiberglass: tensile strength 70–100 ksi; flexural modulus 2.6–3.1 Msi.
Hand-lay-up FRP panels: tensile strength 30–60 ksi; flexural modulus 1.5–2.4 Msi.
The continuous fiber alignment in pultrusion creates a higher strength-to-weight ratio, ideal for load-bearing beams, ladders, and structural platforms.
Impact & Fatigue Resistance
While molded FRP gratings excel in multidirectional impact, pultruded shapes handle cyclic bending better, showing 2–3× the fatigue life in ASTM D3479 tests.
Durability & Environmental Resistance
Corrosion & Chemical Exposure
Both materials resist acids, salts, and moisture far better than steel or aluminum. However, pultruded profiles offer resin-rich veils on all sides, adding an extra barrier against chemical attack in wastewater plants or coastal infrastructure.
UV & Temperature Stability
UV Resistance: Additives such as UV-stabilized veils and surface coats give pultruded fiberglass a 20-year color-retention record in outdoor guardrails.
Thermal Limits: Continuous service up to 150 °C for vinyl ester pultrusions versus 120 °C for many open-mold FRP parts.
Installation & Maintenance Considerations
Dimensional Tolerance – Pultruded pieces stay within ±0.8 mm over 12 m, reducing field shimming.
Fastening – Self-tapping screws and adhesive bonding work for both; pultruded webs accept drilled holes without splintering.
Machinability – Carbon-tipped blades cut cleanly; dust extraction required.
Inspection & Repair – Routine visual checks suffice. Damaged areas can be scarf-sanded and patched with a wet-lay-up kit.
When to Choose Pultruded Fiberglass vs FRP Panels
Choose Pultruded Fiberglass When… | Choose Conventional FRP Panels When… |
---|---|
You need long, straight load-bearing members (beams, handrails, ladders). | Complex curves or one-off shapes dominate the design. |
Tight tolerances and repeatability are critical. | Large flat surfaces (tank linings, wall panels) are required. |
Installation speed and minimal trimming are priorities. | Cost sensitivity outweighs structural demands. |
Conclusion & Next Steps
Pultruded fiberglass and conventional FRP both outperform metals in corrosion resistance and weight savings, yet their differences matter:
Pultruded fiberglass wins on structural strength, dimensional accuracy, and long-term lifecycle value.
Standard FRP panels are better for intricate geometries and budget-sensitive, non-load-bearing applications.
Ready to specify the optimal composite?
Compare your span lengths, load requirements, and fabrication capabilities against the factors above. If pultrusion fits, request mechanical datasheets and cost estimates from certified pultruders. Still unsure? Drop your questions in the comments, share this guide with your design team, and subscribe for future deep-dives into advanced composites.