Unicomposite can supply two kinds of fiberglass grating, FRP Molded Grating and FRP Pultruded Grating.
Molded Grating is made from polyester resin and continuous fiberglass roving, heat cured in a mold, in a hand-crafted layer-by-layer operation to produce the desired thickness and panel size. Grating produced using this technique have 30-35% (total weight) glass fiber reinforcement. The one-piece interwoven mesh construction of the molded grating produces a product with optimal corrosion resistance and bi-directional strength. Since the grating is “cast” in one piece, there is no mechanical joint between bearing bars, unlike pultruded grating where the glued joints can give way in heavy continuous traffic or after prologged service.
The high percentage of resin (65%) in molded grating provides superior corrosion resistance and optimal impact resistance. Molded fiberglass gratings with a square mesh pattern offer increased load capacity and panel utilization due to its bi-directional nature.
And for different application, the surface can be chosed from smooth, concave, gritted or solid-top.
Pultruded Grating is manufactured by pultrusion process, where continuous fiberglass rovings and mats are drawn through rails, resin baths and pre-formers, then wrapped with a synthetic veil and pulled through a heated die. Fiberglass pultruded grating is uni-directional in strength and provides increased load capacity and very good levels of corrosion resistance. Large span area always need safe solution which could provide enough loading for various scenes. That’s why we produce kinds of pultruded gratings. Higher fiber volume and better unidirectional machinery properties than molded grating can make it work well under same clear span. Meanwhile, pultruded grating has all the advantages which molded grating has.
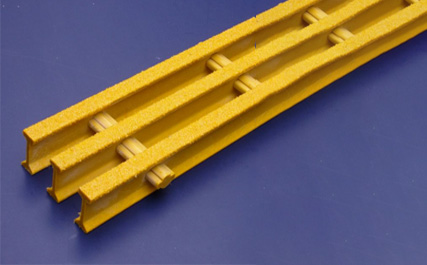
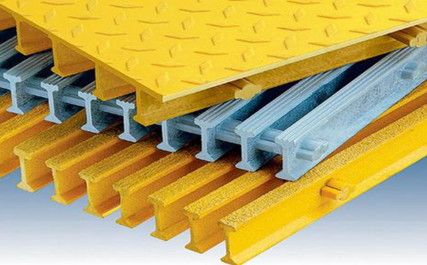
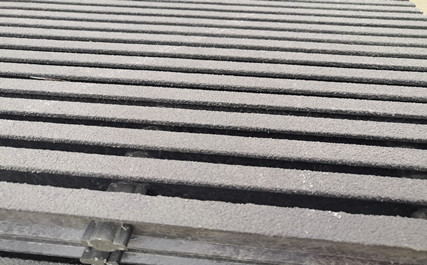
Features of our fiberglass gratings:
- High Strength
- Light Weight
- Fire Retardant
- Corrosion Resistant
- UV Resistance and Anti-aging
- High Impact and Fatigue Strength
- Non Conductive, Low Thermal Conductivity
- Cost Effective, Easy to Install and Maintenance
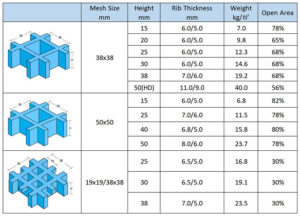
Application
FRP gratings are usually used as floor grating, marina walkway, roof walkway, catwalk grating, work platforms, offshore platforms, decks, stair treads, fencing, tree guard, drain channel cover, ditch covers, etc.
And they are widely used in petroleum, water conservancy, textile printing and dyeing, food processing, electronics industry, sewage treatment, shipbuilding, civil construction, power engineering, power substations, and chemical industries.
To find the specification and more detailed properties of our FRP grating, please feel free to contact us.

Fiberglass Gratings Equipment
Fiberglass gratings equipment is mainly composed of four parts: the molded grating device, heating system, cooling system and ancillary equipment.
FRP molded grating devices can be adjusted according to product size and different specifications, but little change in the overall structure. It is composed of the following components: the cavity part, the roof system, cooling and heating system and basic part.
Heating is necessary to guarantee gratings shape. Unsaturated resin only cures polymerization under certain temperature and humidity, at the same time heating system can ensure the quality of the gratings. The system is composed of a heating pipe and connecting components, and the heating device consists of the external heating curing system.
Cooling is necessary to ensure the production of high speed, specific principles and similar to the heating system.
The heating system consists of heater, temperature controller, rehydration, pipeline, valve and pump system. The function of heating system is to provide heat
Cooling system consists of pipelines, valve and other components, the main role of equipment is to take the heat energy.



Anti-slip Surface Fiberglass Molded Grating
Four Types Fiberglass Gratings
FRP Gratings Connecting And Maintenance