Introduction
When it comes to industrial flooring, molded fiberglass grating stands out as a popular choice due to its strength, durability, and corrosion resistance. But to ensure that you’re choosing the right product for your specific needs, understanding the molded fiberglass grating specification is crucial. This article will provide an in-depth look at the various specifications of molded fiberglass grating, helping you make informed decisions for your next project.
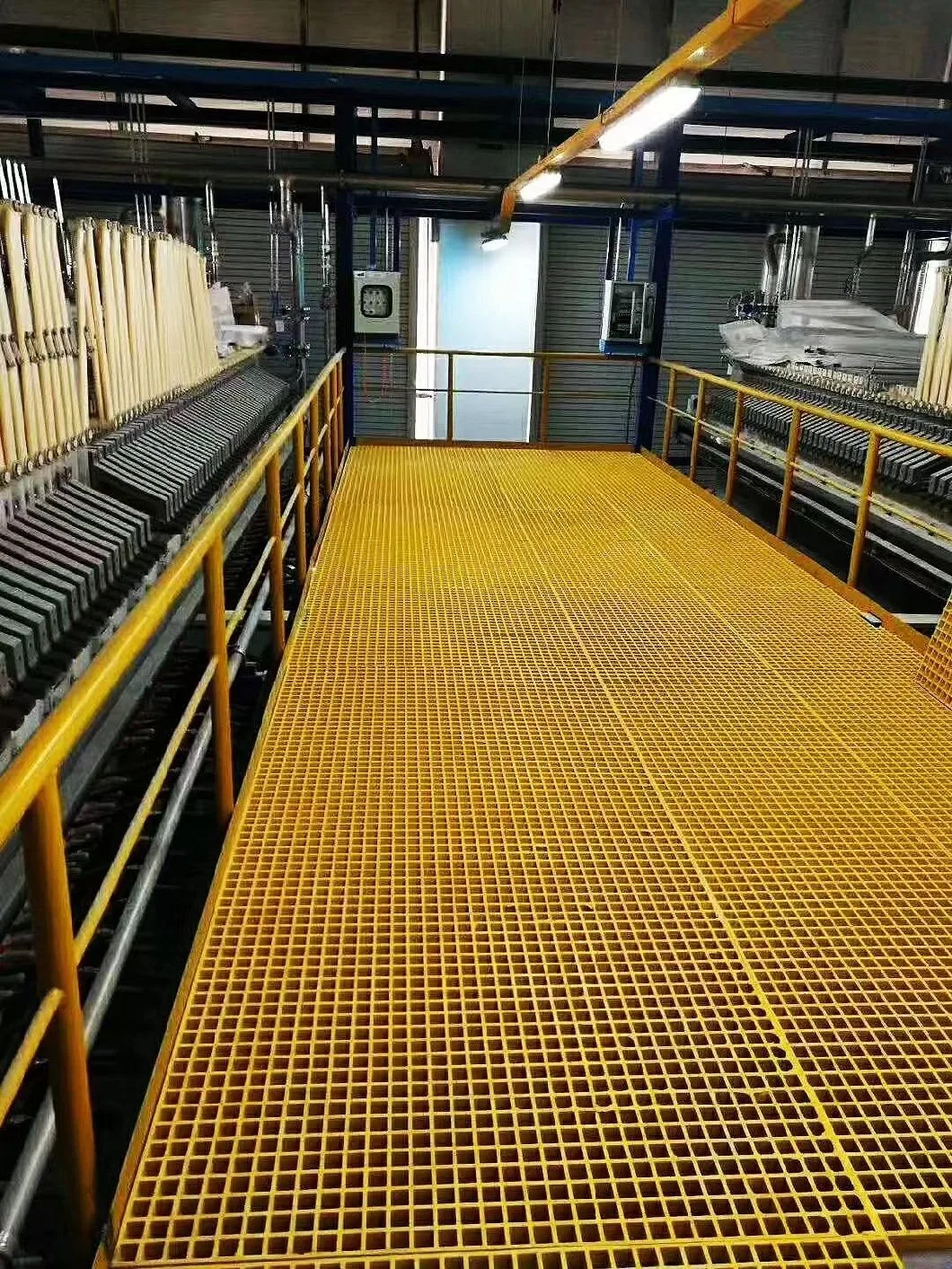
molded fiberglass grating specification
What is Molded Fiberglass Grating?
Molded fiberglass grating is a type of grid flooring made from a matrix of glass fibers and resin. This material is molded to create a strong, lightweight structure that offers high durability and corrosion resistance. Commonly used in industries such as chemical processing, food and beverage, and wastewater treatment, molded fiberglass grating is ideal for environments where exposure to chemicals, moisture, or extreme temperatures is frequent.
Key Specifications of Molded Fiberglass Grating
- Material Composition: Molded fiberglass grating is typically made from a combination of resin (such as polyester, vinyl ester, or phenolic) and fiberglass. The type of resin used can significantly affect the grating’s resistance to various chemicals and environmental conditions. Polyester resins are commonly used for general-purpose applications, while vinyl ester resins provide enhanced chemical resistance, particularly against acids and solvents. Phenolic resins are known for their exceptional fire resistance and low smoke generation.
- Load-Bearing Capacity: One of the most critical specifications is the grating’s load-bearing capacity, which is measured in pounds per square foot (PSF). Depending on the thickness and the design, molded fiberglass grating can support different loads, from pedestrian traffic to heavy equipment. For example, gratings with thicker panels and closer mesh patterns provide greater strength and load-bearing capacity, making them suitable for heavy industrial environments.
- Corrosion and Chemical Resistance: The specific resin used in the grating affects its resistance to chemicals and corrosion. Vinyl ester resins, for example, offer superior resistance to a wide range of harsh chemicals, making them ideal for chemical plants and environments with high exposure to corrosive substances. Polyester resins, while less resistant than vinyl esters, still provide adequate protection in less aggressive environments, such as wastewater treatment facilities or food processing plants.
- Fire Resistance Ratings: Molded fiberglass grating can be engineered to meet specific fire resistance ratings. Some products are manufactured to meet ASTM E-84 Class 1 flame spread ratings, which indicates a lower flame spread in case of fire, making them suitable for use in environments where fire safety is a priority. The choice of resin, such as phenolic, can enhance the grating’s fire resistance, ensuring compliance with safety standards in high-risk environments.
- Size, Thickness, and Mesh Pattern Options: Molded fiberglass grating comes in various sizes, thicknesses, and mesh patterns. Standard panel sizes may include 3’x10’, 4’x8’, and 4’x12’, while mesh patterns can range from square to rectangular configurations. The choice of size and pattern depends on the specific requirements of the installation area. Thicker gratings with smaller mesh openings are typically used in heavy load areas, while thinner gratings with larger openings are suitable for pedestrian traffic or areas where drainage is necessary.
Benefits of Understanding Molded Fiberglass Grating Specifications
- Enhanced Safety and Compliance: By understanding the specifications, you can ensure that the selected grating meets all safety standards and compliance regulations for your industry. This knowledge helps prevent accidents, reduces liability, and ensures that the installation adheres to both local and international safety codes.
- Cost Efficiency and Longevity: Selecting the right specification means choosing a product that will last longer, reducing the need for frequent replacements and repairs, thereby lowering overall costs. For instance, choosing a grating with the appropriate corrosion resistance for a specific environment ensures that the product remains functional and intact over time, even under harsh conditions.
- Customization to Suit Specific Needs: Understanding the different specifications allows you to customize the grating according to specific project requirements, ensuring optimal performance. Whether you need a particular size, color, or surface texture for slip resistance, having a clear grasp of the specifications allows for a more tailored solution that fits your unique needs.
How to Choose the Right Molded Fiberglass Grating for Your Project
When choosing molded fiberglass grating, consider the following factors:
- Environment: Determine the exposure to chemicals, moisture, and other corrosive elements. If the environment is highly corrosive, opt for gratings made with vinyl ester resins for superior protection.
- Load Requirements: Evaluate the load-bearing needs based on the type of traffic (foot traffic, light machinery, or heavy equipment). For areas with heavy machinery, select gratings with higher thickness and smaller mesh patterns for added strength.
- Safety Standards: Ensure that the grating meets all relevant fire safety and industry-specific regulations. If the installation area is prone to fire hazards, choose gratings with high fire resistance ratings, such as those made with phenolic resins.
Tips for Selecting the Best Specifications:
- Opt for grating with high corrosion resistance for chemical environments to extend the product’s lifespan.
- Choose thicker grating with a smaller mesh pattern for areas with heavy equipment to ensure structural integrity and safety.
- Consider fire-resistant ratings if the grating will be installed in areas with high fire risks, ensuring compliance with local building codes and regulations.
Conclusion
Understanding the various molded fiberglass grating specifications is essential for selecting the right product for your project. By considering factors like material composition, load-bearing capacity, and environmental conditions, you can ensure enhanced safety, compliance, and cost efficiency. Ready to choose the perfect molded fiberglass grating for your needs? Contact a specialist today to get expert advice and a quote tailored to your specifications.