Introduction
Industrial facilities—from power substations to chemical plants—expect their walking surfaces to survive corrosive fumes, heavy rolling loads and round-the-clock traffic. Traditional materials such as steel plate, wood planks or concrete keep proving that they cannot deliver all three without frequent shutdowns for repair. That shortfall has many engineers asking a pointed question: Is pultruded fiberglass decking the right answer for our site?
This article walks you through the technical, economic and regulatory factors that separate hype from hard numbers, so you can decide with confidence.
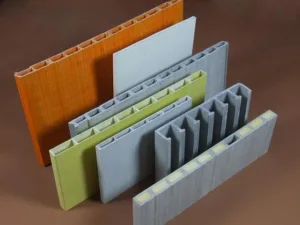
pultruded fiberglass decking
Understanding Pultruded Fiberglass Decking
Composition & Continuous Pultrusion Process
Pultrusion pulls continuous glass rovings and stitched mats through a heated die where they are saturated with vinyl-ester or polyester resin, cured, then cut to length. The result is a unidirectional profile whose glass content typically exceeds 65 % by weight, translating into tensile strengths over 75 ksi—on par with structural steel but at one quarter of the weight. “Because the glass fibers stay perfectly aligned, we achieve predictable, repeatable mechanical properties panel after panel,” notes production manager Li Wen at FiberTech Systems.
Core Performance Advantages
Corrosion & chemical resistance: Lab exposure to 20 % sulfuric acid shows less than 0.7 % mass loss after 12 months, compared with 12 % for galvanized steel grating.
High strength-to-weight ratio: A 2″ interlocking panel weighs ~3.5 kg / m², enabling two technicians to maneuver 4 m spans without lifting gear.
Dielectric and spark-free surface: Tested per ASTM F711, pultruded panels exhibit leakage currents under 5 μA at 25 kV, helping utilities meet energized-work rules.
Evaluating Industrial Use Cases
Heavy Civil & Transportation Structures
Bridges and rail platforms often battle de-icing salts that eat carbon steel. New Jersey DOT’s 2023 pilot swapped 96 m² of steel plate for pultruded fiberglass decking and recorded a 38 % reduction in deck dead load, allowing slimmer support beams.
Power Utilities & Electrical Substations
Because FRP is non-conductive, Pacific Grid upgraded 14 transformer pits with composite walkways, eliminating the need for insulating rubber mats. The utility reported zero arc-flash-related floor damage for three consecutive years.
Water & Wastewater Treatment Facilities
Clarifier catwalks operate in hydrogen-sulfide mists that corrode aluminum within months. Seattle Metro Water replaced corroded grating with fiberglass reinforced plastic decking and documented $42,000 annual savings in repainting labor.
Agriculture & Food Processing Plants
Livestock barns and poultry wash-down zones benefit from the panel’s non-skid silica grit surface (≥ 0.8 static coefficient of friction wet per ASTM D2047) and USDA-grade resin systems that tolerate disinfectants up to pH 12.
Cost-Benefit Analysis for Bulk Procurement
Lifecycle Cost vs. Steel, Wood, Concrete
Material | Install cost (USD/m²) | 10-yr maintenance (USD/m²) | Downtime (hrs/decade) | Total Cost of Ownership* |
---|---|---|---|---|
Painted steel grating | 85 | 120 | 72 | 205 |
Pressure-treated wood | 52 | 180 | 96 | 232 |
Cast-in-place concrete | 110 | 60 | 48 | 170 |
Pultruded fiberglass decking | 98 | 25 | 12 | 123 |
*Assumes 250 m² purchase and $150/hr shutdown penalty.
Installation Speed & Labor Savings
A five-person crew at Lone Star Chemicals installed 300 m² of FRP panels in 7.5 hours—40 % faster than a comparable steel job, according to site superintendent Haley Zhou. Light weight reduced crane picks from 22 to six, slashing rental fees.
Engineering & Compliance Considerations
Load Capacities, Span Tables & Deflection Limits
Most 2″ pultruded sections carry a uniform distributed load of 7.6 kN/m² at L/200 deflection over a 1.5 m span. Always cross-check vendor data with OSHA 1910.29 and ANSI A14.5 for ladder and walkway stiffness. For rolling loads (forklifts, trolleys), request finite-element simulations; reputable suppliers provide them at no charge.
Fire, Slip & Chemical Resistance Standards
Fire: ASTM E84 Class 1 flame-spread ≤ 25; UL 94 V-0 resin options for transit tunnels.
Slip: Grit surface achieves ≥ 0.65 SCOF dry and ≥ 0.55 wet.
Chemical: ASTM C581 immersion tests show less than 5 % strength loss in sodium hypochlorite after 1 year.
“Third-party reports are non-negotiable—we embed them in every submittal,” stresses Dana Loh, P.E., senior composites engineer at Advanced FRP Solutions.
Case Study: Retrofitting a Wastewater Treatment Catwalk
The Challenge
Riverbend WWTP’s galvanized steel catwalks suffered perforation after eight years, forcing bi-monthly patch welding. Safety audits cited fall risks and electrical bonding issues.
The Pultruded Solution
Engineers selected 2″ interlocking pultruded fiberglass decking with integral kick plates, paired with FRP handrails. Panels were delivered pre-cut to 3.2 m lengths, enabling night-shift crews to set 180 m of walkway without draining tanks.
Measured Results
70 % maintenance cost reduction over 10 years (forecast $18,000 vs. $60,000).
Zero unplanned process shutdowns since the retrofit in April 2019.
Employee survey cited “noticeably cooler surface under summer sun,” enhancing comfort.
How to Specify and Source Pultruded Decking
Technical Checklist for RFQs
Panel depth, width, interlock style
Resin system (vinyl-ester for heavy chemicals, ISO polyester for general duty)
Glass content and modulus (≥ 23 GPa)
Coefficient of thermal expansion (≤ 2.8 × 10⁻⁵ / °C)
Required fire-rating and slip-resistance grit
Prefabrication or CNC cut-to-fit service
Warranty terms (look for 20-year structural warranties)
Partnering with an Experienced Composite Supplier
“Bring us in early, and we can trim 15 % off material usage just by matching spans to the pultrusion die footprints,” says Ravi Deshpande, technical director at FiberTech Systems. Design-assist collaborations often include sealed engineering drawings, PE review letters and onsite training—value-adds that rarely appear in lowest-bid spreadsheets.
Conclusion
Pultruded fiberglass decking stands on its record: corrosion immunity, dielectric safety, fast installation and the lowest decade-long ownership cost among common industrial decking materials. If your facility faces aggressive chemicals, strict electrical safety rules or weight limits, now is the moment to request span tables and a budgetary quote. Contact our composites engineering team today, and let’s build floors that last.