Introduction
When it comes to industrial flooring solutions, the decision between industrial GRP grating and traditional metal grating can significantly impact safety, maintenance costs, and overall efficiency. Industrial GRP grating, also known as glass-reinforced plastic or fiberglass-reinforced plastic (FRP) grating, is engineered to offer a combination of corrosion resistance, strength, and durability. Metal grating, on the other hand, has been a long-standing choice due to its familiarity and robust load-bearing capacity. In this article, we’ll compare these two options in depth to help you determine the best fit for your facility.
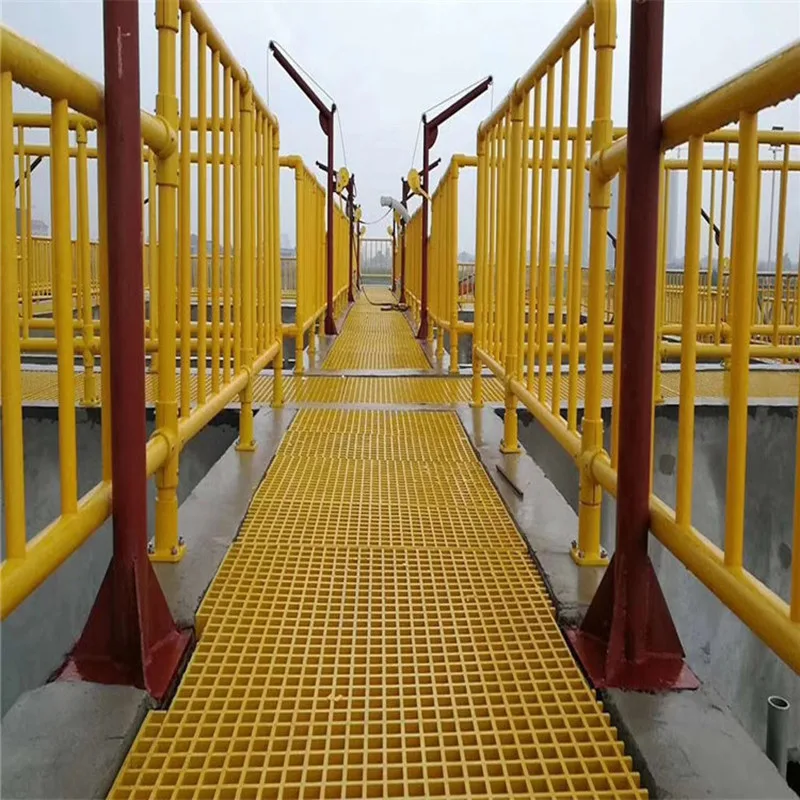
industrial grp grating
What Is Industrial GRP Grating?
Composition and Features
Industrial GRP grating is made by combining glass fibers with a polymer resin, resulting in a strong, lightweight, and corrosion-resistant flooring solution. This composite material is designed to withstand harsh chemicals, extreme weather conditions, and intense industrial wear. Notable features include:
- High Corrosion Resistance: Ideal for environments exposed to moisture, chemicals, or saltwater.
- Non-Conductive: A safer option for workplaces that handle electrical equipment.
- Lightweight Construction: Easier to transport, handle, and install compared to metal grating.
Brief History and Usage
While metal grating has been around for decades, industrial GRP grating emerged as a modern solution to common problems such as rust and high maintenance costs. Over the years, improvements in composite technology have led to better load-bearing capacity and greater resilience. Today, GRP grating is found in a wide range of applications, including walkways, platforms, and stair treads in chemical plants, food processing facilities, and marine settings.
Traditional Metal Grating: An Overview
Common Types of Metal Grating
Metal grating is typically made from materials like steel, aluminum, or stainless steel. Some common forms include:
- Welded Steel Grating: The most common form, created by welding steel bars together.
- Press-Locked Grating: Made by press-fitting slotted bars together.
- Swage-Locked Aluminum Grating: An alternative to steel, offering lighter weight and corrosion resistance.
Typical Applications in Industry
Industries have relied on metal grating for its load-bearing capabilities and durability. You’ll often see metal grating in heavy-duty environments such as:
- Oil refineries and petrochemical plants
- Mining operations
- Construction sites
- Manufacturing facilities
Despite its strengths, metal grating is susceptible to corrosion and rust in wet or chemically exposed environments, often leading to more frequent maintenance and potential safety hazards.
Key Comparison Factors
Strength and Durability
- Industrial GRP Grating: Thanks to the composite structure, GRP grating can handle significant loads without bending or breaking. Its resilience to impact makes it suitable for areas with heavy foot traffic or regular equipment movement.
- Metal Grating: Steel and other metals have a proven track record for strength. However, repeated exposure to harsh conditions can compromise structural integrity unless regularly treated or coated.
Corrosion Resistance
- Industrial GRP Grating: One of GRP’s major selling points is its exceptional resistance to chemicals, moisture, and salt spray. It doesn’t rust or degrade easily, making it a go-to choice in corrosive or marine environments.
- Metal Grating: While stainless steel and coated steel grating can hold up against rust better than regular steel, they can still corrode over time if not properly maintained.
Maintenance and Lifecycle Cost
- Industrial GRP Grating: Although it might have a higher upfront cost, GRP requires minimal upkeep. It doesn’t need painting or frequent replacement due to rust or corrosion. Over time, this can result in lower lifecycle costs.
- Metal Grating: Metal generally costs less initially, but maintenance expenses—such as rust prevention, painting, and potential replacements—add up quickly. For industries with significant exposure to harsh elements, these recurring costs can be substantial.
Safety and Slip Resistance
- Industrial GRP Grating: Often manufactured with an anti-slip surface, GRP reduces the risk of slips and falls. According to the National Safety Council, slips, trips, and falls account for a significant portion of workplace injuries, making slip resistance a critical factor.
- Metal Grating: Metal surfaces can become slippery, especially when wet or oily. Many metal gratings are also available with serrated or textured surfaces, but the risk of corrosion can degrade these features over time.
Advantages of Industrial GRP Grating
Lightweight and Easy Installation
Industrial GRP grating weighs significantly less than steel, making it easier to transport, handle, and install. A lighter weight also reduces the need for heavy lifting equipment and can speed up project timelines.
Customization Options
Manufacturers offer GRP grating in various panel sizes, thicknesses, and mesh configurations. This versatility allows you to customize the grating to your facility’s specific needs, such as load-bearing requirements, color-coded safety zones, or specialized anti-slip surfaces.
Compliance with Industry Standards
Many industrial GRP grating products are tested and certified to meet specific safety standards. For instance, certain GRP gratings comply with the Occupational Safety and Health Administration (OSHA) guidelines and international building codes, ensuring your facility meets strict safety requirements.
Potential Drawbacks of Industrial GRP Grating
Higher Initial Cost
While you may save in the long run on maintenance and replacements, the upfront investment for industrial GRP grating can be more than for traditional metal grating. This cost difference can be a deterrent for small operations with limited budgets.
Heat Resistance Considerations
GRP has a lower melting point compared to metals. In extremely high-temperature environments, metal grating may be more suitable. Facilities handling molten metal or extremely high heat processes should evaluate the temperature tolerance of GRP carefully.
Making the Right Choice for Your Facility
Assessing Environmental Conditions
Consider factors like exposure to chemicals, saltwater, or extreme temperatures. If corrosion is your biggest concern, industrial GRP grating likely offers a better ROI and enhanced safety.
Budgeting for Long-Term ROI
Beyond the initial purchase price, factor in future maintenance costs. If the environment demands frequent upkeep for metal surfaces, GRP’s higher upfront cost might pay off in the long run through reduced repairs and replacements.
Seeking Professional Guidance
Each facility has unique demands, from load requirements to safety specifications. Consult with flooring specialists or engineers who have experience with both metal and industrial GRP grating solutions. Their insights will help you weigh the pros and cons based on actual usage and environmental conditions.
Conclusion
Choosing between industrial GRP grating and traditional metal grating ultimately depends on your facility’s specific needs and conditions. While metal grating remains a robust and budget-friendly option for many, industrial GRP grating stands out in environments where corrosion resistance, low maintenance, and slip prevention are paramount. By considering factors like environmental exposure, long-term maintenance costs, and safety requirements, you can make an informed decision that best supports productivity and worker well-being.
Ready to pick the perfect grating solution for your facility? Share your experiences or questions in the comments below, and don’t forget to subscribe to our newsletter for more in-depth insights on industrial flooring and safety solutions.