Introduction
Skimming a fiberglass grating catalog can feel like paging through a phone book written in engineering jargon. Yet making the wrong choice risks costly downtime, safety hazards, and replacement expenses. This guide walks you step-by-step through every catalog detail—so you can pinpoint the exact grating that matches your facility’s loads, chemicals, and compliance rules without wasting a cent.
Quick stat: The global FRP (fiberglass-reinforced plastic) grating market is projected to surpass US $1.1 billion by 2030, driven by industries seeking lighter, longer-lasting alternatives to steel (Grand View Research, 2024).
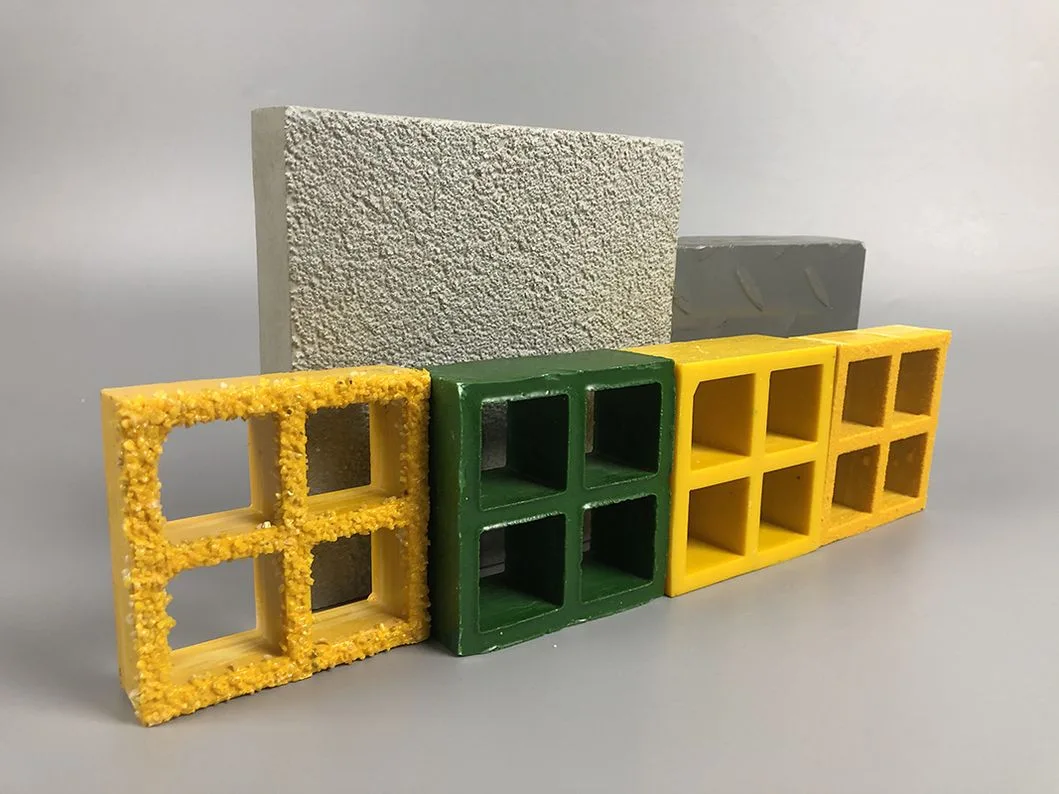
fiberglass grating catalog
1. Define Your Application Environment
Before opening the catalog, list the real-world conditions your grating must survive.
Chemical exposure: acids, alkalis, salt spray, oils
Moisture & temperature swings: indoor wash-down, offshore platforms, frigid warehouses
Traffic type: pedestrian, rolling carts, forklifts, heavy trucks
Safety priorities: slip resistance, fire retardancy, electrical insulation
Having this checklist lets you filter catalog pages quickly—anything that fails on environment goes straight to the “no” pile.
2. Decode Core Specifications
Every fiberglass grating catalog leads with specs. Here’s what each really means for performance:
Spec in Catalog | What It Tells You | Why It Matters |
---|---|---|
Load rating (psf or kN/m²) | Maximum uniform load the panel supports at listed span | Confirms the grating won’t sag or crack under everyday traffic |
Span chart | Recommended distances between supports | Helps design framing and avoids guesswork |
Resin system (polyester, vinyl ester, phenolic) | Chemical resistance profile | Choose vinyl ester for aggressive chemicals; phenolic for low-smoke offshore safety |
Glass content (%) | Strength vs. corrosion balance | Higher glass means stronger but slightly less corrosion-resistant |
Surface finish (meniscus, grit, concave) | Slip resistance rating (COF) | Grit tops usually hit ≥0.6 COF, beating OSHA’s wet-surface guideline |
Open area (%) | Drainage, airflow, light transmission | More open area = lighter weight, but lower load capacity |
Pro tip: Highlight your non-negotiables (e.g., “load ≥ 500 psf, vinyl ester resin, 70 % open area”). Then search the catalog’s product matrix—often a single table shows which SKUs clear these hurdles in one glance.
3. Read Load Tables and Span Charts Like a Pro
Load tables list deflection (sag) at given spans. The industry rule of thumb is L/200 deflection—meaning a 2.4 m panel may deflect up to 12 mm under full load. In the span chart:
Find your target load (uniform or concentrated).
Slide horizontally until deflection ≤ L/200.
Read the maximum span allowed—never exceed it in design.
If you need longer spans than the chart allows, step up to a thicker bar height or switch to molded over pultruded grating.
4. Balance Cost Against Lifecycle Value
Up-front price per square meter can mislead. Vinyl ester panels might cost 15 % more than general-purpose polyester, but last twice as long in corrosive splash zones—cutting replacement labor and plant shutdowns.
Use this simple Lifecycle Value Equation:
Choose the SKU with the lowest annual cost—even if the catalog shows a higher sticker price.
5. Verify Compliance and Certifications
Industrial auditors increasingly demand documentation. A credible fiberglass grating catalog should reference:
ASTM F3059 (load testing & labeling)
ISO 9001 (quality systems)
DNV, ABS, Lloyd’s Register approvals for marine/offshore use
UL 94 V-0 or ASTM E84 Class 1 flame-spread ratings for fire-critical zones
If the catalog omits certifications, request third-party test reports before you buy.
Industry quote: “Spec sheets printed without independent test data are just marketing brochures.” — Elaine Foster, P.E., Senior Materials Engineer, Composite Structures Institute
6. Assess Supplier Support and Customization
Even a perfect catalog spec won’t help if lead times or cut-to-size services fall short.
Fabrication options: CNC-routed cutouts, stair treads, kick-plates, cover plates
Stock vs. custom colors: OSHA safety yellow for egress routes, dark gray to hide dirt
Shipping & crate design: Seaworthy packaging prevents bar end damage—ask to see a crate photo.
Field support: On-site measuring or install training can cut days off shutdowns.
Experienced suppliers highlight these services prominently; if buried in footnotes, dig deeper.
Conclusion
Navigating a fiberglass grating catalog isn’t about memorizing specs—it’s about matching real-world demands to the numbers on the page. Define your environment, focus on the critical specs, run the load-span check, compare lifecycle value, confirm compliance, and vet supplier support. Follow these steps and you’ll land the perfect industrial fit—one that keeps workers safe, auditors satisfied, and budgets intact.
Ready to get started? Leave a comment with your toughest grating scenario, share this guide with your maintenance team, or subscribe to our newsletter for monthly FRP insights. Your next project deserves a catalog-powered head start!