Creating fiberglass parts without a traditional mold involves a few steps that require precision, patience, and a bit of creativity. The process I’ll describe is akin to creating a “one-off” part, often used for custom projects where creating a permanent mold may not be practical or necessary. Here’s a simplified overview:
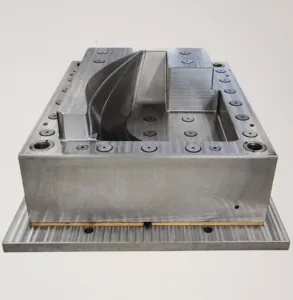
how to make fiberglass parts without a mold
1. Design and Create a Plug
The “plug” is essentially the exact shape you want your final fiberglass part to be. You can make it from a variety of materials, such as wood, foam, or even clay, depending on the complexity and size of the part you’re aiming to create. This plug needs to be finished to a very high standard, as any imperfections will transfer to the final fiberglass piece.
2. Prepare the Surface
Once your plug is ready and perfectly smooth (as any imperfections will transfer to your final part), you’ll need to apply a release agent. This prevents the fiberglass from sticking to the plug. Common release agents include wax-based products or PVA (Polyvinyl Alcohol).
3. Apply Gelcoat (Optional)
Gelcoat is a specialized resin that provides a high-quality finish on the surface of the fiberglass part. It’s applied directly onto the plug’s surface. This step is optional and depends on the required finish for your part.
4. Lay the Fiberglass
Cut fiberglass cloth or mat to cover the plug, allowing for overlap at edges. Resin is then applied to the plug’s surface, and the fiberglass material is laid over it. Use a brush or roller to work the resin into the fiberglass, removing any air bubbles and ensuring the material conforms to the shape of the plug. You may need to apply several layers, allowing each layer to cure slightly before applying the next.
5. Release the Part
Once the fiberglass has fully cured, you can separate it from the plug. This might require gentle prying and tapping. If you’ve applied a good release agent and prepared the surface well, the fiberglass part should come off without too much trouble.
6. Trim and Finish
The final step involves trimming any excess material from the edges of the part and sanding it to achieve the desired finish. Additional finishing operations might include painting or the application of a protective clear coat.
Creating fiberglass parts without a mold is a labor-intensive process that requires a good deal of craftsmanship, especially in the preparation of the plug and the finishing of the final part. However, it allows for a great deal of flexibility and customization in creating parts for prototypes, custom cars, boats, or other projects where a one-off part is needed.