Fiberglass molding is an invaluable skill for creating durable, custom shapes and products—from automotive components to boat repairs and craft projects. Whether you’re a DIY enthusiast or a beginner looking to expand your crafting skills, understanding how to fiberglass mold can significantly enhance your projects. This comprehensive, step-by-step guide breaks down the process clearly, enabling beginners to create professional-quality molds confidently.
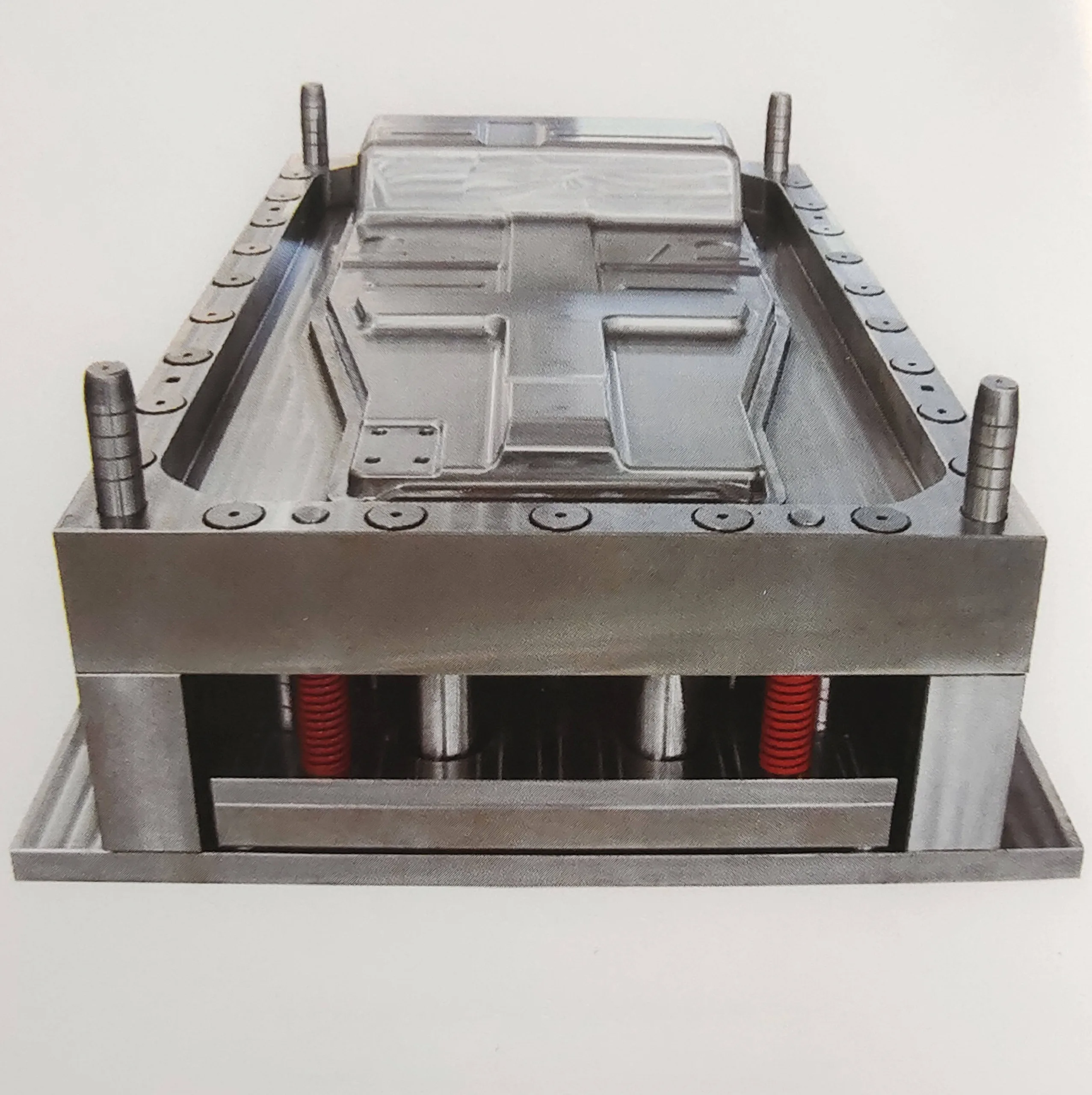
how to fiberglass mold
Introduction to Fiberglass Molding
Fiberglass molding is the process of forming fiberglass-reinforced plastic (FRP) into precise shapes using molds. Popular for its strength, durability, and lightweight properties, fiberglass molding is widely utilized in automotive, marine, aerospace, and artistic applications. Mastering this technique not only empowers your creativity but also saves money by reducing reliance on expensive custom-made products.
Let’s dive into the step-by-step process to get you started quickly and safely.
Materials and Tools Needed for Fiberglass Molding
Before starting, ensure you have the following essential materials and tools:
Fiberglass cloth or mat
Polyester or epoxy resin
Hardener (catalyst)
Mold release wax or spray
Gelcoat (optional, for surface finishing)
Mixing containers and stirring sticks
Gloves and safety goggles
Respirator mask
Paintbrushes and rollers
Sandpaper (medium and fine grit)
Scissors or utility knife
Measuring tape
Step-by-Step Guide to Fiberglass Molding
Step 1: Prepare Your Mold
Proper preparation of your mold is crucial for smooth removal and professional-looking results:
Clean the mold thoroughly, removing dust, debris, and any imperfections.
Apply mold release wax or spray evenly, then buff it after drying to ensure the fiberglass does not stick.
Step 2: Apply Gelcoat (Optional but Recommended)
A gelcoat layer creates a smooth, durable finish and protects the fiberglass surface from UV damage:
Mix gelcoat according to the manufacturer’s instructions.
Use a brush or sprayer to apply an even, thin coat onto the mold surface.
Allow it to cure partially until tacky (usually 1–2 hours).
Step 3: Cut and Prepare Fiberglass Material
Preparation saves time and improves accuracy during application:
Measure and cut your fiberglass cloth or mat slightly larger than the mold dimensions.
Lay out the pieces in advance to ensure proper coverage and overlap edges by about an inch.
Step 4: Mix Resin and Hardener
Accurate mixing is crucial for strength and curing:
Follow the resin manufacturer’s recommended ratio carefully.
Stir the mixture thoroughly, scraping the sides of the container until homogeneous.
Only mix small amounts at a time to avoid premature curing.
Step 5: Apply Resin and Fiberglass to the Mold
Now, it’s time to create your mold:
Using a paintbrush, apply a thin coat of resin directly over the mold surface (or gelcoat layer).
Place the fiberglass cloth or mat gently onto the wet resin.
Carefully apply another resin layer over the fiberglass, saturating it thoroughly.
Use a roller or brush to eliminate air bubbles and smooth wrinkles.
Repeat layering (resin–fiberglass–resin) until achieving the desired thickness, typically 2–4 layers.
Step 6: Allow the Mold to Cure
Proper curing ensures durability and structural integrity:
Allow the fiberglass mold to cure fully—typically 24–48 hours, depending on your resin type and environmental conditions.
Maintain good ventilation and consistent temperature for optimal results.
Step 7: Demolding and Finishing
Removing your fiberglass mold carefully and finishing properly ensures a professional-quality end product:
Gently separate the fiberglass mold from your form. Use wooden or plastic wedges to assist if needed.
Inspect for defects like bubbles or rough areas and sand lightly with medium then fine grit sandpaper for smoothness.
Trim excess fiberglass edges with a utility knife or scissors.
Tips for Successful Fiberglass Molding
To enhance your results and safety, consider these expert tips:
Safety First: Always use gloves, safety glasses, and a respirator mask. Fiberglass materials and resin fumes can be harmful.
Temperature Control: Maintain a consistent temperature of around 70–80°F (20–27°C) for proper resin curing.
Work Fast but Thoroughly: Resin cures quickly; work efficiently to apply evenly and remove air pockets.
Start Small: Begin with simple molds before progressing to complex shapes to gain confidence and technique.
According to research by Markets and Markets, the fiberglass market is projected to grow significantly, driven by its versatility and durability across industries. Developing skills in fiberglass molding could open various practical and entrepreneurial opportunities.
Common Mistakes Beginners Make and How to Avoid Them
Awareness of common pitfalls can help you avoid costly errors:
Improper Resin Mixing: Always measure resin and hardener accurately. Miscalculations lead to weak molds or incomplete curing.
Skipping Mold Release: Never skip applying mold release wax; this step is vital for easy demolding.
Rushing the Process: Allowing adequate curing time ensures structural integrity and longevity of your mold.
Neglecting Safety Equipment: Exposure to fiberglass or resin fumes can lead to serious health issues. Protective gear is non-negotiable.
Conclusion and Next Steps
Fiberglass molding is a rewarding skill, offering endless possibilities in crafting customized, durable items. By carefully following each step, from preparing the mold to applying and finishing the fiberglass, beginners can achieve impressive results on their first attempt.
Remember:
Proper mold preparation and precise resin mixing are key.
Safety precautions are crucial.
Patience and attention to detail pay off in professional results.
Now it’s your turn! Share your first fiberglass mold experience below or connect with our community to ask questions and exchange tips. Don’t forget to subscribe for more expert DIY guides and crafting ideas!