Creating fiberglass molds is an essential skill in manufacturing and crafting processes, widely used in automotive, marine, construction, and art industries. However, beginners often face common pitfalls that result in poor mold quality or structural weaknesses. Understanding and avoiding these mistakes can significantly enhance your mold-making skills, save costs, and yield better-quality results. In this article, we’ll discuss the most common errors encountered when creating fiberglass molds and provide practical solutions to avoid them.
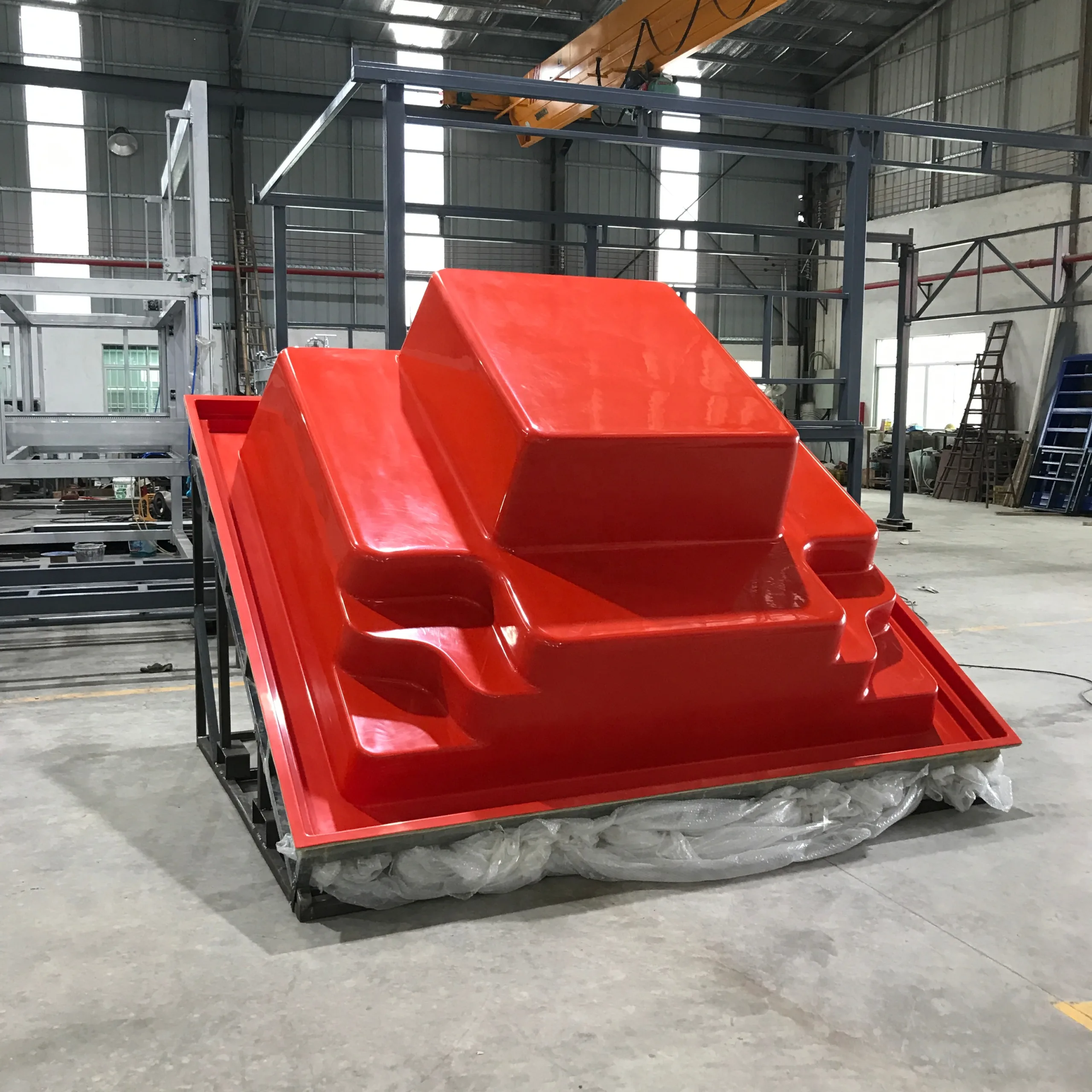
how to create fiberglass molds
Mistake 1: Poor Surface Preparation
Surface preparation is the foundation of creating durable fiberglass molds. An inadequately prepared surface can lead to mold imperfections, causing defects in your final product.
How to Avoid:
Clean Thoroughly:
Before applying any fiberglass material, meticulously clean the surface using acetone or a specialized cleaning agent to remove dust, grease, and contaminants.Smooth the Surface:
Sand the original object (plug) progressively using fine grit sandpaper (e.g., 220 to 600 grit). Achieve a polished surface finish to prevent imperfections.Apply Release Agents:
Use high-quality mold-release agents evenly and adequately. Applying multiple thin coats is better than one thick coat, ensuring easy separation later.
Mistake 2: Incorrect Use of Gelcoat
The gelcoat is crucial as it provides the mold’s glossy finish and protects the mold from abrasion and chemical damage. Incorrect gelcoat application often leads to uneven coverage, sagging, or premature degradation of the mold.
How to Avoid:
Correct Mixing Ratios:
Always measure and mix the gelcoat and catalyst according to the manufacturer’s recommended ratios. Usually, gelcoats require 1.5-2% catalyst.Application Thickness:
Apply the gelcoat at a recommended thickness of approximately 18-25 mils (0.45 to 0.65 mm). Too thin, and the mold becomes fragile; too thick, and it risks cracking or sagging.Curing Time:
Allow the gelcoat ample curing time (typically 1-3 hours at room temperature, depending on the product) before proceeding to fiberglass layering.
Mistake 3: Improper Resin and Fiberglass Application
Using the wrong resin type or incorrectly laying fiberglass materials often results in weak, brittle, or uneven molds.
How to Avoid:
Choose the Right Resin:
Select an appropriate resin type (polyester, epoxy, or vinyl ester) based on your project’s specific requirements. Polyester is popular due to its cost-efficiency and ease of use; epoxy is known for superior strength and durability.Proper Layering Technique:
Start with a thin, uniform resin layer applied evenly across the surface, followed by a fiberglass mat or woven cloth. Use rollers to ensure even saturation and eliminate air pockets.Avoid Air Entrapment:
Regularly check and eliminate air bubbles using rollers or brushes. Air pockets weaken molds significantly.
Mistake 4: Inadequate Curing Process
Rushing or neglecting the curing process results in incomplete curing, warping, and structural instability of molds.
How to Avoid:
Follow Manufacturer Guidelines:
Strictly adhere to resin curing times and environmental conditions provided by the manufacturer.Control Temperature and Humidity:
Optimal curing typically requires temperatures between 65°F–80°F (18°C–27°C) and humidity below 70%. Ensure your workspace maintains these conditions consistently.Allow Full Cure:
Even if the mold feels hard to the touch, complete curing usually takes 24–72 hours. Avoid early demolding to preserve mold integrity.
Mistake 5: Ignoring Safety and Health Precautions
Working with fiberglass materials poses safety hazards such as skin irritation, inhalation of toxic fumes, and chemical burns.
How to Avoid:
Protective Equipment:
Wear gloves, safety goggles, respirators (rated for fumes and dust), and protective clothing during the entire mold-making process.Proper Ventilation:
Operate in well-ventilated areas or use exhaust fans to reduce fume inhalation.Safe Material Handling:
Store chemicals safely according to guidelines and immediately dispose of contaminated materials.
Mistake 6: Poor Mold Reinforcement
Neglecting reinforcement leads to molds prone to distortion or cracking over repeated uses.
How to Avoid:
Add Reinforcement Ribs:
Incorporate strategically placed reinforcement ribs or braces to support mold stability, especially for larger molds.Use Proper Thickness:
Build up sufficient thickness (typically 3-6 mm) of fiberglass layers to ensure structural strength without excess weight or material wastage.Allow Additional Curing for Reinforcements:
Reinforcements and ribs should be fully cured to achieve optimal structural integrity.
Mistake 7: Neglecting Mold Maintenance and Storage
Improper mold maintenance drastically shortens mold lifespan and diminishes quality over time.
How to Avoid:
Regular Inspection:
Regularly inspect molds for signs of wear, cracking, or degradation. Immediate repairs prolong mold life significantly.Proper Cleaning and Storage:
Clean molds after each use with recommended cleaners, and store molds carefully in dry, controlled conditions away from direct sunlight or moisture.
Conclusion: Achieving Consistent Quality in Fiberglass Molds
Creating fiberglass molds effectively requires attention to detail, careful preparation, and proper handling of materials. By recognizing and avoiding common mistakes such as poor surface preparation, incorrect gelcoat application, improper resin use, inadequate curing, ignoring safety precautions, insufficient mold reinforcement, and neglecting maintenance, you will significantly improve your mold-making skills and results.
Ready to master fiberglass mold-making? Share your mold-making experiences or ask questions in the comments below. If you found this guide useful, don’t hesitate to share it on social media and subscribe for more practical tips on fiberglass crafting!