Introduction
Fiberglass plastic round tubes have become a go-to choice for industries seeking a light yet strong alternative to traditional materials like metal or PVC. Whether you’re designing a project that requires high mechanical strength, corrosion resistance, or simply a material that can withstand harsh conditions, fiberglass plastic round tubes can offer the perfect blend of reliability and affordability. In this guide, we’ll walk you through the key factors to consider so that you can choose the best fiberglass plastic round tubes for your unique needs.
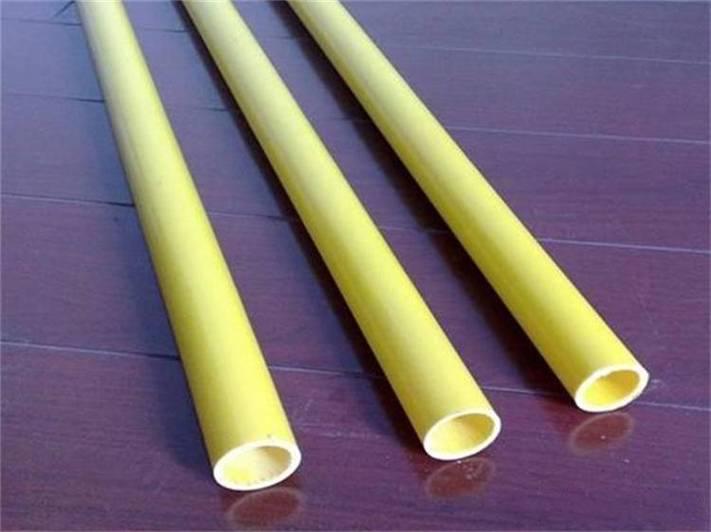
fiberglass plastic round tubes
Understanding Fiberglass Plastic Round Tubes
Basic Composition and Properties
Fiberglass plastic round tubes are typically made by combining fine glass fibers with resin, resulting in a composite material that exhibits impressive tensile strength and stiffness. These tubes can handle significant stress without bending or breaking, making them ideal for structural and mechanical applications. According to a market analysis by Global Market Insights, the fiberglass market size is expected to grow significantly in the coming years, fueled by the demand for high-performance, cost-effective materials.
- Lightweight: Because they’re made of glass fibers and resin rather than metal, fiberglass tubes weigh much less while retaining similar strength levels.
- Non-Conductive: Fiberglass inherently does not conduct electricity, an important safety feature for electrical applications.
- Corrosion Resistant: Fiberglass will not rust, a major advantage for outdoor structures exposed to moisture.
Common Uses and Industry Applications
Due to these beneficial properties, fiberglass plastic round tubes are used in various sectors:
- Construction: Ideal for handrails, ladders, and structural reinforcements.
- Marine and Boating: Resistant to saltwater corrosion, perfect for boat railings and masts.
- Electrical and Telecommunications: Non-conductive qualities make them suitable for cable supports and antenna structures.
- Sports Equipment: Commonly used in poles, rods, and handles for their lightweight and durable nature.
Factors to Consider When Choosing Fiberglass Plastic Round Tubes
Material Grade and Quality
Not all fiberglass plastic round tubes are created equal. Manufacturers often use different resin systems—such as polyester, vinyl ester, or epoxy—to achieve specific performance characteristics.
- Polyester Resin: Generally the most budget-friendly and works well for general-purpose applications.
- Vinyl Ester Resin: Offers better chemical resistance and tensile strength, suitable for harsher environments.
- Epoxy Resin: Delivers excellent mechanical strength and adhesion, often used in high-performance applications such as aerospace components.
When selecting tubes, make sure you know the resin system used and confirm it aligns with the demands of your project.
Size and Dimensional Accuracy
Fiberglass tubes come in various diameters and wall thicknesses. Ensure you have precise measurements to match your design specifications:
- Outer Diameter (OD) and Inner Diameter (ID) must accommodate the loads and fit any inserts or couplings you plan to use.
- Wall thickness should be adequate for the required load-bearing capacity.
- Tolerances on both diameter and length can affect the overall integrity of your final product or structure.
Strength and Durability Requirements
Consider the tensile strength, flexural strength, and impact resistance needed for your application. A simple hobby project may only need moderate strength, but industrial uses—like scaffolding or structural reinforcements—often demand high load-bearing capabilities. Look for tubes that include published data sheets or test results to confirm their mechanical properties.
Environmental Conditions and Chemical Resistance
Fiberglass excels in environments where metals would corrode. However, the level of chemical resistance can still vary based on the resin formulation.
- Outdoor Exposure: UV-resistant resins help maintain structural integrity even under prolonged sunlight.
- Extreme Temperatures: Epoxy-based tubes typically withstand higher temperatures compared to polyester-based ones.
- Chemicals and Solvents: If your application involves acids or harsh chemicals, choose tubes specifically formulated to handle those conditions.
Comparing Fiberglass Plastic Round Tubes to Other Materials
Fiberglass vs. PVC
PVC is another popular option for lightweight pipe-like structures. However, PVC can become brittle under extreme temperatures and typically offers lower strength compared to fiberglass. While PVC might be sufficient for low-stress applications like simple plumbing, fiberglass plastic round tubes provide superior rigidity and can handle more demanding environments.
Fiberglass vs. Metal
Metal tubes—especially steel—can handle very heavy loads but are prone to corrosion, significantly adding to maintenance costs. Fiberglass tubes do not rust, making them more durable in long-term outdoor or marine applications. Additionally, metal tubes tend to be heavier, which can affect portability and installation costs. If you’re seeking a balance between strength, weight, and resistance to environmental factors, fiberglass is often the more practical choice.
Best Practices for Selecting a Reliable Supplier
Certifications and Quality Control
When looking for a reputable supplier of fiberglass plastic round tubes, check if they have certifications like ISO 9001, which indicates strong quality management systems. A supplier that follows standardized production processes will likely offer more consistent products.
Customer Support and Warranty
Quality tubes come with reliable after-sales support. Before finalizing your purchase, ask about:
- Product Testing and Guarantees: Ensure the tubes meet industry standards and come with a warranty.
- Technical Assistance: Some suppliers provide consultation to help you choose the right grade, size, and finish.
- Delivery and Logistics: Timely shipping and clear packaging details can prevent damage during transit.
Conclusion
Choosing the best fiberglass plastic round tubes comes down to understanding your project’s needs—from strength and size requirements to chemical and UV resistance. Always verify the material grade, consult with suppliers on quality standards, and weigh how fiberglass compares to alternate materials like PVC or metal. By doing your homework, you can ensure that your final selection meets both performance and budgetary goals.
Call to Action: If you found this guide helpful, share your thoughts in the comments below or reach out with any questions you have. Don’t forget to subscribe to our newsletter for more in-depth articles on fiberglass materials and other practical solutions for your next project!