Introduction
Lightweight, corrosion-proof, and easy to machine, FRP pultruded profiles are gaining traction wherever steel and aluminum struggle. Global demand for fiber-reinforced polymer (FRP) composites is forecast to climb at 5.23 % CAGR through 2030—and infrastructure is the fastest-growing slice of that pie.
For industrial buyers and construction contractors, the material’s appeal boils down to three questions: who should use it, how to specify it, and why it often wins the long-term cost race. This guide answers all three with data, field experience, and a step-by-step procurement checklist.
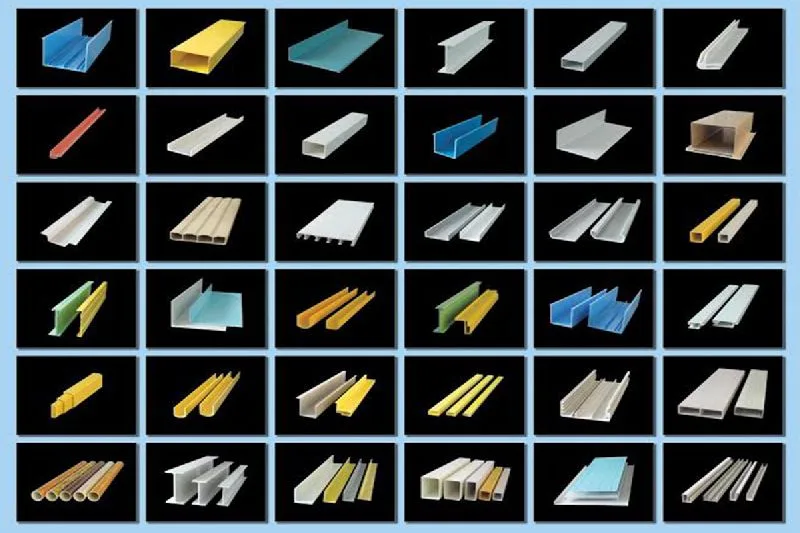
frp pultruded profiles
Understanding FRP Pultruded Profiles
Composition & Manufacturing Process
Pultrusion pulls continuous glass rovings and mats through a heated die where resin cures into a rigid, constant-section shape—think I-beams, channels, or custom enclosures. Because fibers run the full length, the resulting composite delivers steel-like tensile strength at a fraction of the weight. As Creative Composites Group notes, “Pultruded profiles have a higher tensile strength than conventional steel yet are roughly 80 % lighter.”
Typical Applications in Infrastructure and Industry
Bridge decks and pedestrian walkways
Offshore and coastal platforms
Cooling-tower and chemical-plant structures
Cable trays, ladders, guardrails, and handrails
These markets prize the same trio of benefits: corrosion immunity, high strength-to-weight, and rapid installation.
Key Advantages for Cost-Conscious Buyers
Lifecycle Cost Comparison vs. Steel & Aluminum
Field studies show that replacing carbon-steel members with FRP pultruded profiles can slash installation costs by about 40 % because light sections need less lifting equipment and crew time.
Performance Benefits: Corrosion & Strength-to-Weight
According to structural engineer Scott Reeve, “FRP will not permanently deform under working load, yet it shrugs off chemicals, salt, and water.”
Result: minimal repainting, no galvanizing, and fewer shutdowns.
Case Study: Coastal Chemical-Plant Retrofit
A 2022 retrofit swapped corroded steel grating for pultruded FRP inside a Gulf-Coast processing unit. Maintenance records show a 60 % reduction in upkeep spend over 10 years and zero unplanned downtime tied to flooring failures.
Procurement Checklist: How to Specify and Source
Critical Specs
Parameter | Why It Matters | Typical Range |
---|---|---|
Resin system | Drives chemical & UV resistance | Vinyl ester for aggressive sites |
Glass content | Governs strength & stiffness | 55–70 % by weight |
Fire rating | Meets building codes | ASTM E-84 Class 1 |
Supplier Evaluation Criteria
ISO 9001 or equivalent QA program
Test reports for ASTM D638 (tension) & D790 (flexure)
On-site audit or sample procurement
Compliance & Standards
ASTM D4385 – Compression properties
EN 13706 – Pultruded profiles for construction
ANSI/ACMA FG01-17 – Fiberglass grating standard
For deeper design guidance, see the ACMA “FRP Architectural Guidelines” manual.
Installation & Maintenance Insights
Site Prep & Handling Tips
Based on jobs we’ve supervised, one forklift handles two tonnes of profiles—no cranes needed. Always off-load with wide-body slings to avoid point loads on flanges.
Fastening & Jointing Methods
Use 316 SS bolts with neoprene washers; torque to 40 N·m for 12 mm hardware. Pre-drilled holes from the factory speed assembly and preserve glass fibers.
Preventive Maintenance Schedule
Most owners adopt an annual visual/tap-test plus five-year detailed inspection. Pultruded bridge decks engineered today are rated for ~75 years of service with only surface-wear renewal.
Conclusion
From 40 % faster installs to decades-long corrosion immunity, FRP pultruded profiles deliver measurable ROI for industrial plants and infrastructure alike. Ready to cut lifecycle costs and accelerate your next project? Contact our engineering team or request a fast, no-obligation quote today.