Introduction
Choosing between fiber-reinforced plastic (FRP) and traditional fiberglass can feel like splitting hairs—both are composites and both rely on fibers for strength. Yet the differences are crucial when you’re chasing lighter structures, longer service life, or tougher corrosion resistance. In the next few minutes, you’ll see how FRP vs fiberglass stack up across seven categories that matter on real-world jobsites, so you can spec with confidence and avoid costly rework later.
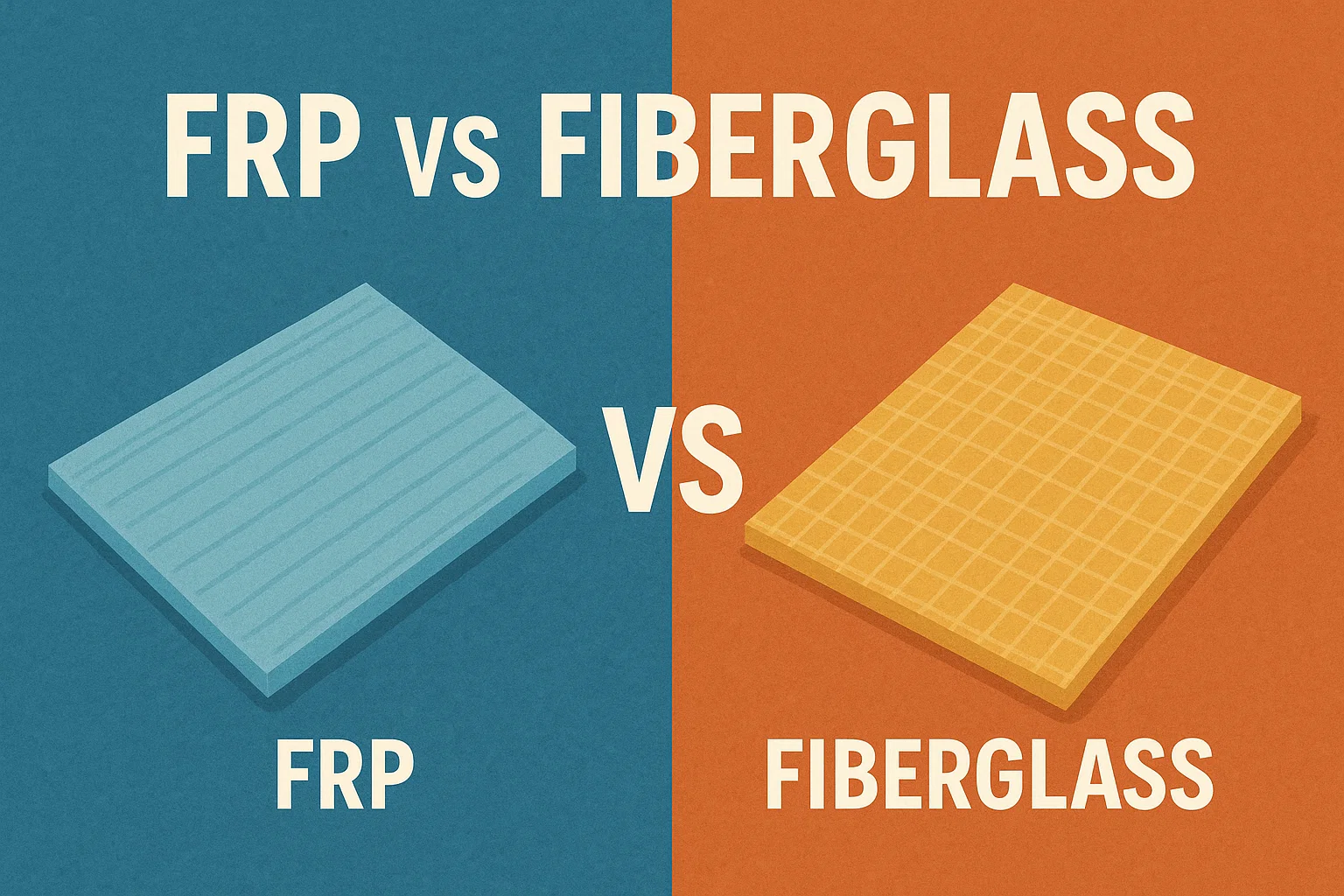
frp vs fiberglass
Composition and Manufacturing
Raw Materials Matter
Fiberglass is always glass fibers in a polymer matrix—no exceptions.
FRP is broader: the “fiber” can be glass, carbon, aramid, basalt, or a hybrid blend, giving engineers a menu of stiffness, weight, and cost profiles.
Because fiberglass is essentially a subset of FRP, every fiberglass panel is FRP, but not every FRP panel is fiberglass.
Processing Techniques
Process | Typical for Fiberglass | Typical for Advanced FRP | What It Means for You |
---|---|---|---|
Hand lay-up & spray-up | ✔ | Limited | Low tooling cost, but slower cycles |
Pultrusion | ✔ | ✔ | Continuous profiles, tight tolerances |
Filament winding | Limited | ✔ | High axial strength—great for tanks & pipes |
Resin transfer molding (RTM) | Limited | ✔ | Smooth finishes, repeatability |
Actionable tip: If your design needs carbon-glass hybrids for localized stiffening (e.g., ladder side-rails with rigid rungs), verify your vendor runs RTM or filament winding that can place multiple fiber types in one pass.
Mechanical Strength and Weight
Tensile & Flexural Strength
A 2024 meta-analysis of 790 tests found that carbon-rich FRP laminates routinely hit 800–1 200 MPa tensile strength, while standard E-glass fiberglass averaged 350–600 MPa.The bottom-line: FRP lets you dial in higher safety factors without a weight penalty.
Weight-to-Strength Ratio
Typical FRP structural shapes weigh about 1.5–2 lb/ft², roughly 35 % lighter than comparable fiberglass laminates of equal thickness.That translates to:
Smaller cranes or even manual lifts on site.
Lower transport costs—especially valuable for remote or offshore builds.
Corrosion and Chemical Resistance
Glass fibers handle moisture well, but the real enemy is the resin. Premium FRP systems use vinyl-ester or epoxy matrices formulated for aggressive acids, alkalis, and chloride brines. If your structure faces pH < 2 or continuous saltwater splash, step up to an FRP grade with a resin rating of C- or better in ASTM C581 immersion charts. Fiberglass boat hulls handle brackish water fine, yet they show osmotic blistering faster than corrosion-grade FRP gratings.
Quick checklist
Chemical plants → vinyl-ester FRP
Pulp-and-paper bleach lines → fluoropolymer-lined FRP
Architectural façades → polyester fiberglass is usually adequate
Thermal and Fire Performance
Fiberglass melts around 815 °C, but its polymer burns first. FRP systems combat this with:
Intumescent additives that char and insulate.
Phosphorus-based flame retardants for self-extinguishing performance (ASTM E84 Class A).
For continuous exposure above 120 °C, look for high-temperature epoxy FRP or silica-rich fiberglass with ceramic fillers.
Installation and Maintenance
Cutting & drilling: Carbide tooling works for both, but FRP with carbon tends to blunt bits faster—budget extra blades.
Joining: Mechanical fasteners, bonded joints, or integrated inserts. FRP often arrives with molded-in connection points, trimming site labor.
Upkeep: Both are paint-free and resist rot; however, UV clear-coat on exterior fiberglass panels should be refreshed every 5–7 years, whereas UV-stable FRP gelcoats can last a decade.
Cost and Lifecycle Economics
Metric | Fiberglass | FRP (Glass) | FRP (Carbon Blend) |
---|---|---|---|
Material $/kg | Low | Moderate | High |
Install labor | Medium | Low | Low |
30-year maintenance | Medium | Low | Low |
When you annualize costs over 30 years, FRP often wins—especially where downtime is expensive (cooling-tower walkways, chemical sumps). Use a net-present-value calculator to justify the upgrade in your bid package.
Sustainability and Environmental Impact
Thermoplastic FRP can be reheated and recycled, diverting waste from landfills; thermoset fiberglass cannot. Re-meltable matrices also accept reclaimed fibers, cutting embodied carbon by up to 25 %. If green-building credits (LEED, BREEAM) matter, specify thermoplastic FRP with ≥30 % recycled content and request an Environmental Product Declaration (EPD) from suppliers.
Conclusion & Next Steps
FRP vs fiberglass isn’t just semantics—it’s seven decisive factors that shape weight, strength, durability, budget, and even environmental credentials. Remember: fiberglass is your cost-effective workhorse, but modern FRP opens the door to lighter lifts, tougher chem-resistance, and cleaner lifecycle numbers.
Ready to pick a winner? Drop your project details in the comments, share this guide with your engineering team, or subscribe for our upcoming case-study series on FRP retrofits. Your next build deserves the right composite—make the choice count!