Fiberglass molded grating is made of glass fiber-reinforced plastics, resins, pigments, and related materials. This article gives detailed answers to the application and process of fiberglass molded grating.
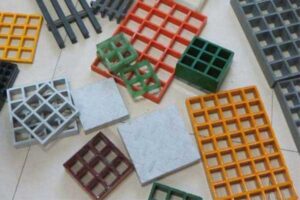
Technology and application of glass fiber molded grating
Material of fiberglass molded grille
Glass fiber molded grating is a kind of plate-shaped material with many spaces, which is made of glass fiber as reinforcing material, unsaturated polyester resin as matrix, and compounded by special processing. It is also generally called fiberglass molded grating, FRP grating, or FRP grating. The main component of glass fiber molded grating is silicon oxide, which is an inorganic material, its physical and chemical properties are very stable, and it has high strength, high modulus, high wear resistance, excellent cold resistance, and no long-term creep change; good thermal stability; network structure to interlock and limit the aggregate; improve the load-bearing capacity of asphalt mixture. Because the surface is coated with special modified asphalt, it has double composite properties, greatly improving the wear resistance and shearing capacity of the glass fiber molded grating.
The process of fiberglass molded grille
The process of glass fiber molded grating mainly adopts the molding process, which is a commonly used and highly creative molding method in the production of composite materials: first, add a certain amount of premix or prepreg into the metal pair mold, and after heating, Solidification after pressurization.
The main advantages of the compression molding process:
1. High production efficiency, easy-to-realize specialized and automatic production;
2. The product has high dimensional accuracy and good repeatability;
3. The surface is smooth and clean, with no need for secondary modification;
4. It can form products with complex structures at one time;
5. Because of mass production, the price is relatively low.
The disadvantages of compression molding are mainly that mold manufacturing is complicated, the investment is large, and the press limits it, so it is most suitable for mass production of small and medium-sized composite products.
With the continuous improvement and development of metal processing technology, the press manufacturing level and synthetic resin process performance, the tonnage of the press and the size of the table are increasing, and the molding temperature and pressure of the molding material are relatively reduced, making the size of the molded product gradually. Large-scale development is currently widely used in the market.
Application of fiberglass molded grating
FRP grating can be used as a structural material, with corrosion resistance and flame retardant, non-magnetic insulation, no need for paint, no maintenance, long service life, can be used for fifteen to twenty years, lightweight, very convenient for opening and cutting, and bright colors, There are a variety of styles and forms to choose from. The upper layer of FRP grating is composed of an FRP grid, and the lower layer is the ground of the building matrix. The operator walks on the surface of the grid, and the finished product can be placed on the surface of the grid, while the waste liquid and slag can be discharged to the ground of the lower base. After the operation is completed, the piles on the ground can be washed away with a powerful water sprayer, which is convenient for the operators and managers to go to the site for inspection. For mobile operating platforms, it is more suitable to use lightweight fiberglass grids.
Water treatment: maintenance walkways, gutter covers, large containers, cleaners, trash racks, flow tanks, hangers for biochemical water treatment pools, ventilation windows, stairs, cooling tower operating table pavement
Chemical plants: stair slabs, operating platforms, guardrails, double floors, trench covers, gratings
Petroleum Industry: Offshore Oil Platforms
Textile factory: replace the metal grille, and wooden platform and cover the concrete floor, next to the bleaching and dyeing vat, floor, near the valve, etc.
Power plant: chemical water workshop trench cover, waste water pool, etc.
Metal surface treatment: pickling solution places, replacing wooden floors around machines, around highly corrosive containers, plating line walkways, double floors
Marine food processing plants: harsh environments such as slippery surfaces, ships
Transportation industry: platforms, ship decks, walkways, military minesweepers, stair treads
Beverage industry: stair slabs, replacing expensive stainless steel, loaded floors
Pulp and processing plants: Stairs and floors, floor walkways, places with high humidity
Electronics industry: trench cover, pickling workshop, anti-static (anti-static grid), and high cleanliness workshop
Meat processing plants: corrosive floors, stairs, slippery floors, workbenches, and stair treads
Car wash room/car beauty shop: car wash room drainage board, parking space, car wash room trench cover
Crane: on the aisle of a 3-meter or 6-meter-long crane
In addition, fiberglass molded grilles are used in other scenarios, such as corrosion-resistant shelves, decoration, square fountains, scaffolding, civil building facilities, breeding fences, double-layer floors, etc.
The above is about the process and application of glass fiber molded grating. If you want to know about the process and application of glass fiber molded grating, please contact us by email, such as glass fiber molded grating customization, glass fiber molded grating quotation, We will give you serious and detailed answers to the production standards of fiberglass molded gratings and other content!