In the world of construction, where strength and durability are paramount, the choice of reinforcement material plays a critical role. For decades, steel rebar has been the go-to option, providing the necessary support to concrete structures. However, with advancements in technology and a growing emphasis on sustainability, fiberglass rebar has emerged as a compelling alternative. Offering a unique combination of strength and flexibility, American fiberglass rebar is reshaping the construction landscape.
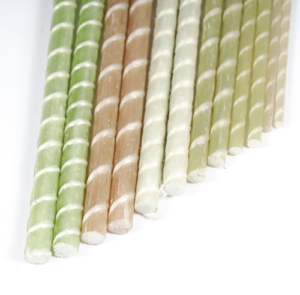
american fiberglass rebar
1. Introduction
Construction projects rely heavily on rebar for reinforcing concrete structures, ensuring their stability and longevity. Traditionally, steel rebar has been used for this purpose due to its high tensile strength. However, steel rebar is not without its limitations, as it is susceptible to corrosion and can be challenging to handle and transport.
The introduction of fiberglass rebar has revolutionized the construction industry. Made from a composite material consisting of glass fibers and a polymer matrix, fiberglass rebar overcomes many of the drawbacks associated with steel rebar. This article Unicomposite pultruded profiles explores the strengths and flexibility of American fiberglass rebar and highlights its numerous advantages over traditional reinforcement materials.
2. What is Fiberglass Rebar?
Fiberglass rebar, also known as GFRP (Glass Fiber Reinforced Polymer) rebar, is a versatile construction material that offers superior performance in various applications. It is composed of high-strength glass fibers embedded in a polymer resin matrix, resulting in a lightweight and durable product. Compared to steel rebar, fiberglass rebar exhibits unique properties that make it an excellent choice for modern construction projects.
3. Strengths of Fiberglass Rebar
3.1 High Tensile Strength
Despite its lightweight nature, fiberglass rebar boasts impressive tensile strength. It has a tensile modulus that is several times higher than that of steel rebar, enabling it to withstand heavy loads and resist cracking. This exceptional strength makes fiberglass rebar an ideal choice for projects where high structural integrity is required.
3.2 Corrosion Resistance
One of the most significant drawbacks of steel rebar is its vulnerability to corrosion, which can lead to structural degradation and costly repairs. In contrast, fiberglass rebar is inherently corrosion-resistant. It does not rust or deteriorate when exposed to moisture or chemicals, ensuring the longevity and durability of reinforced structures, even in harsh environments.
3.3 Lightweight and Easy Handling
Transporting and handling steel rebar can be a labor-intensive task due to its weight and bulkiness. Fiberglass rebar, on the other hand, is significantly lighter, making it easier to transport and maneuver on construction sites. This lightweight characteristic not only reduces installation time but also minimizes the risk of injuries associated with heavy lifting.
3.4 Non-Magnetic Properties
Fiberglass rebar is non-magnetic, which makes it ideal for projects that require non-conductive or non-magnetic properties. It is widely used in sensitive areas where electromagnetic interference must be minimized, such as MRI rooms, power plants, and high-tech facilities.
4. Flexibility of Fiberglass Rebar
In addition to its remarkable strength, American fiberglass rebar offers unparalleled flexibility, allowing it to adapt to various construction requirements. Its flexible properties provide several benefits in terms of structural design, expansion, and maintenance.
4.1 Flexural Strength
The flexural strength of fiberglass rebar allows it to withstand bending and flexing without losing its structural integrity. This property makes it an excellent choice for applications where the reinforcement material needs to conform to curved or irregular shapes. It enables engineers and architects to push the boundaries of design, creating innovative and aesthetically pleasing structures.
4.2 Thermal Expansion and Contraction
Traditional steel rebar is susceptible to thermal expansion and contraction, which can cause cracks and structural instability in concrete. Fiberglass rebar, with its low thermal expansion coefficient, mitigates these issues by reducing the risk of cracking due to temperature fluctuations. This characteristic is particularly beneficial in regions with extreme climates.
4.3 Adaptability to Various Construction Projects
The flexibility of fiberglass rebar allows it to be easily customized and tailored to specific project requirements. It can be manufactured in various shapes, sizes, and configurations to accommodate unique construction needs. This adaptability makes fiberglass rebar suitable for a wide range of applications, including bridges, highways, marine structures, and concrete reinforcement.
5. Applications of Fiberglass Rebar
The versatility and reliability of American fiberglass rebar have resulted in its widespread adoption across various construction projects. Here are some key applications where fiberglass rebar has proven its effectiveness:
5.1 Bridges and Highways
Bridges and highways are subjected to heavy loads and constant exposure to environmental factors. Fiberglass rebar’s corrosion resistance and high tensile strength make it an ideal choice for reinforcing these critical infrastructure elements. It offers long-term durability, reducing maintenance and repair costs while ensuring the safety and integrity of the structures.
5.2 Marine Structures
In marine environments, where corrosion is a major concern, fiberglass rebar outshines traditional steel rebar. It withstands the harsh conditions of saltwater, moisture, and chemicals without compromising its structural integrity. Whether it’s seawalls, docks, or offshore platforms, fiberglass rebar provides a reliable and long-lasting reinforcement solution.
5.3 Concrete Reinforcement
Concrete is the backbone of modern construction, and fiberglass rebar offers a superior alternative to steel reinforcement within concrete structures. It enhances the crack resistance and load-bearing capacity of concrete while eliminating the risk of corrosion. Fiberglass rebar is particularly beneficial in structures exposed to aggressive chemicals, such as wastewater treatment plants and industrial facilities.
5.4 Industrial and Commercial Buildings
From warehouses to high-rise buildings, fiberglass rebar finds extensive application in industrial and commercial construction. Its lightweight nature simplifies the construction process and reduces overall project timelines. Additionally, its non-magnetic properties make it suitable for projects where electromagnetic interference needs to be minimized, such as data centers or research facilities.
6. Installation and Maintenance
Proper installation and maintenance are crucial for the optimal performance of fiberglass rebar. While the installation process is similar to that of steel rebar, there are specific considerations to ensure its effectiveness:
6.1 Cutting and Handling Techniques
Fiberglass rebar can be easily cut using standard tools such as saws or abrasive wheels. However, it is essential to use appropriate safety equipment, such as goggles and masks, to protect against any potential fiber release during cutting. Proper handling techniques should be followed to prevent damage and maintain the integrity of the rebar.
6.2 Splicing and Connecting
Splicing and connecting fiberglass rebar require special attention to ensure structural integrity. Manufacturers provide guidelines and approved methods for splicing, which should be followed meticulously. Proper connections guarantee the continuous reinforcement of concrete structures, eliminating potential weak points.
6.3 Longevity and Durability
Fiberglass rebar has a long service life, often exceeding that of traditional steel rebar. Its corrosion resistance and ability to withstand environmental elements contribute to its durability. Regular inspections and maintenance can help identify any signs of wear or damage, allowing for timely repairs or replacements, if necessary.
7. Cost Considerations
The cost implications of using fiberglass rebar compared to traditional steel rebar extend beyond the initial investment. While fiberglass rebar may have a higher upfront cost, it offers significant long-term savings:
7.1 Initial Investment vs. Long-Term Savings
Although the initial cost of fiberglass rebar may be higher than that of steel rebar, its superior durability and corrosion resistance result in reduced maintenance and repair expenses over time. This can lead to substantial cost savings throughout the lifespan of a structure.
7.2 Reduction in Maintenance and Repair Expenses
Corrosion in steel rebar often leads to costly repairs and replacements. Fiberglass rebar eliminates these expenses, as it is impervious to corrosion. The long-term cost benefits associated with reduced maintenance and repair make fiberglass rebar an attractive option for construction projects.
7.3 Impact on Overall Project Costs
While the upfront cost of fiberglass rebar may increase the overall project cost marginally, the long-term savings, coupled with enhanced structural performance, justify the investment. Contractors and project owners recognize the value in choosing a reinforcement material that offers durability, longevity, and reduced maintenance expenses.
8. Case Studies and Success Stories
The effectiveness of American fiberglass rebar can be witnessed through numerous successful projects and case studies. Here are some examples that highlight its practical application and positive outcomes:
- Case Study 1: Bridge Rehabilitation Project
A deteriorating bridge in a coastal area required reinforcement to ensure its structural integrity. Fiberglass rebar was chosen as the reinforcement material due to its corrosion resistance. The project was completed efficiently, reducing construction time and minimizing disruptions to traffic. The fiberglass rebar provided long-term durability, protecting the bridge from the corrosive effects of the marine environment. - Case Study 2: Industrial Facility Construction
During the construction of a large industrial facility, the use of fiberglass rebar significantly expedited the process. The lightweight nature of fiberglass rebar allowed for easy handling and installation, resulting in faster project completion. Additionally, the absence of corrosion in the reinforced concrete eliminated the need for costly repairs and maintenance, saving both time and money.
These case studies demonstrate the successful integration of fiberglass rebar in real-world construction projects, showcasing its advantages over traditional reinforcement materials.
9. Environmental Benefits
The construction industry is increasingly focusing on sustainable practices, and fiberglass rebar aligns with these objectives. Here are some notable environmental benefits associated with its usage:
- Sustainability and Eco-friendliness: Fiberglass rebar is manufactured using recycled materials and requires less energy to produce compared to steel rebar. By reducing reliance on non-renewable resources and promoting recycling, fiberglass rebar contributes to a more sustainable construction industry.
- Lower Carbon Footprint: The production and transportation of fiberglass rebar result in lower carbon emissions compared to steel rebar. Its lightweight nature reduces fuel consumption during transportation, further minimizing environmental impact.
- Recycling and Reusability: At the end of a structure’s life cycle, fiberglass rebar can be recycled and repurposed, reducing waste and conserving resources. This recyclability ensures a circular approach to construction, aligning with the principles of a circular economy.
10. Challenges and Limitations
While fiberglass rebar offers numerous benefits, there are challenges and limitations that need to be considered:
- Code Compliance and Regulations: Building codes and regulations governing the use of fiberglass rebar may vary across regions. It is essential for project teams to ensure compliance with local codes and obtain necessary approvals before incorporating fiberglass rebar in construction projects.
- Education and Awareness: The adoption of fiberglass rebar requires education and awareness among architects, engineers, contractors, and other stakeholders. Enhancing knowledge about its properties, installation techniques, and long-term benefits will drive wider acceptance and usage.
- Availability and Accessibility: In some areas, the availability of fiberglass rebar may be limited compared to steel rebar. Ensuring a consistent supply chain and accessibility to quality fiberglass rebar products is crucial for its widespread adoption.
11. Future Prospects
The future of fiberglass rebar in construction looks promising. Ongoing research and development efforts aim to further enhance its properties and expand its range of applications. Advancements in manufacturing processes, such as pultrusion technology, are improving the quality and cost-effectiveness of fiberglass rebar. With the growing demand for sustainable and durable construction materials, fiberglass rebar is expected to witness increased adoption in the coming years.
Conclusion
American fiberglass rebar has emerged as a strong and flexible alternative to traditional steel rebar in construction. Its unique combination of strength, durability, corrosion resistance, and sustainability makes it an attractive choice for various projects. By embracing fiberglass rebar, construction professionals can optimize structural performance, reduce maintenance costs, and contribute to a more sustainable built environment.
FAQs
FAQ 1: Can fiberglass rebar replace steel rebar entirely?
While fiberglass rebar offers numerous advantages, its usage may not be suitable for all applications. Factors such as project requirements, structural design, and local regulations play a crucial role in determining whether fiberglass rebar can replace steel rebar completely. Consulting with structural engineers and adhering to local building codes is essential.
FAQ 2: Does fiberglass rebar require special installation techniques?
The installation of fiberglass rebar follows similar techniques to steel rebar. However, specific considerations such as proper handling, cutting techniques, and approved splicing methods are necessary to maintain its integrity. It is recommended to refer to manufacturer guidelines and consult with experts for proper installation procedures.
FAQ 3: Is fiberglass rebar more expensive than steel rebar?
Fiberglass rebar generally has a higher upfront cost compared to steel rebar. However, when considering long-term savings in terms of reduced maintenance, repairs, and increased durability, the overall cost benefits of fiberglass rebar become apparent.
FAQ 4: Can fiberglass rebar be used in extreme climates?
Yes, fiberglass rebar’s low thermal expansion coefficient makes it suitable for use in extreme climates. It can withstand temperature fluctuations without compromising the integrity of the reinforced concrete.
FAQ 5: Where can I get fiberglass rebar for my construction project?
Fiberglass rebar can be sourced from reputable manufacturers and suppliers specializing in construction materials. It is advisable to conduct research, compare product quality and prices, and engage with experienced suppliers to ensure the availability of reliable fiberglass rebar for your specific project needs.
In conclusion, embracing American fiberglass rebar in construction provides the industry with a reliable, durable, and sustainable reinforcement solution. Its exceptional strength, flexibility, and resistance to corrosion make it a valuable choice for a wide range of applications. By utilizing fiberglass rebar, construction professionals can enhance structural performance, reduce maintenance costs, and contribute to the development of a more sustainable built environment.