When choosing materials for construction, manufacturing, or repairs, selecting the right composite is crucial. Fiberglass and FRP (Fiber Reinforced Polymer) are often used interchangeably, leading to confusion. However, each has distinct features, benefits, and limitations. Understanding these differences helps ensure your project’s durability, cost-effectiveness, and performance. This guide will clearly outline when and why you’d prefer fiberglass or FRP for your specific needs.
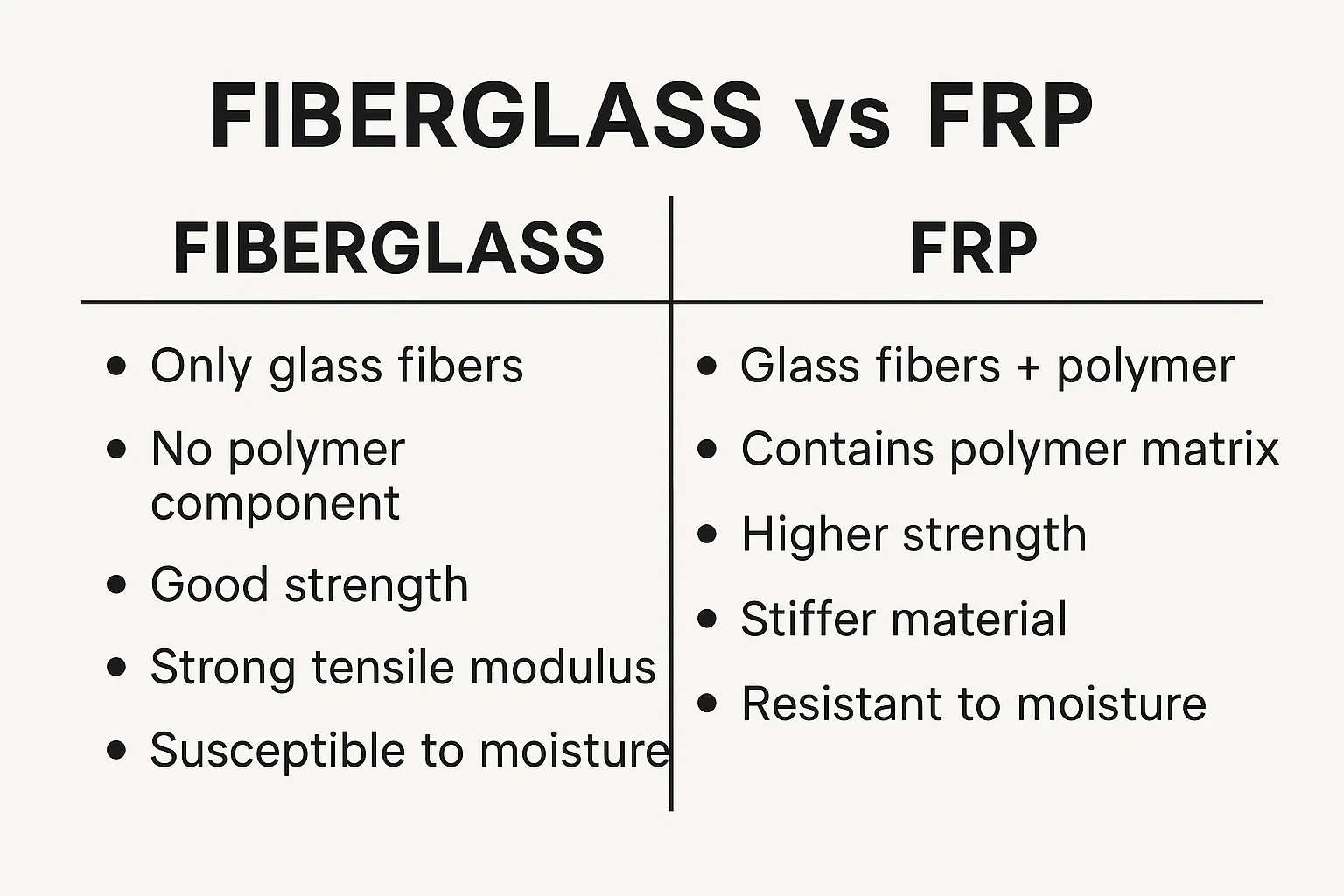
fiberglass vs frp
Understanding the Basics: Fiberglass and FRP
First, let’s clarify the terms:
Fiberglass is a material consisting of fine glass fibers. It’s lightweight, durable, resistant to corrosion, and commonly used in insulation, automotive parts, and marine applications.
FRP (Fiber Reinforced Polymer) is a composite material combining a polymer resin with reinforcing fibers—usually glass, carbon, or aramid. It provides excellent strength-to-weight ratio, durability, and corrosion resistance, suitable for structural reinforcements, construction, infrastructure, and industrial uses.
Key Differences Between Fiberglass and FRP
Composition and Structure
Fiberglass consists exclusively of glass fibers woven into sheets or mats, typically bound by resin. FRP, however, can incorporate a broader range of fibers, including:
Glass fibers (Fiberglass itself)
Carbon fibers
Aramid fibers (e.g., Kevlar)
Thus, fiberglass is essentially a type of FRP, but FRP encompasses a broader variety of composites.
Strength and Performance
Fiberglass:
Good strength and flexibility.
Suitable for applications requiring moderate strength and cost-effectiveness, such as automotive body parts or boat hulls.
FRP:
Superior strength, stiffness, and impact resistance, especially with carbon or aramid reinforcement.
Ideal for structural applications, aerospace components, and demanding engineering projects.
According to the American Composites Manufacturers Association, FRP materials reinforced with carbon fiber can offer up to five times the strength of standard fiberglass, depending on the resin and fiber orientation used.
Cost Considerations
Fiberglass:
Relatively low-cost.
Best suited for budget-sensitive projects where extreme strength isn’t essential.
FRP:
Higher initial costs, particularly when using advanced fibers like carbon.
Cost-effective in long-term applications due to durability and reduced maintenance expenses.
Corrosion Resistance and Durability
Both fiberglass and FRP provide excellent corrosion resistance, but FRP typically offers enhanced long-term durability, particularly in harsh environments:
Fiberglass:
Resistant to chemical corrosion, moisture, and rust.
Commonly used in marine environments, storage tanks, and water treatment plants.
FRP:
Offers higher resistance to extreme environmental conditions and aggressive chemicals.
Often preferred in infrastructure, chemical plants, bridges, and offshore applications.
Ease of Installation and Maintenance
Fiberglass:
Lightweight, easy to handle and install.
Repairable with standard tools and simple methods.
FRP:
Equally lightweight but may require specialized installation techniques for advanced composites (carbon FRP).
Maintenance usually minimal due to its higher durability.
Practical Examples: Which to Choose?
Consider these examples to illustrate when fiberglass or FRP would be the better choice:
Marine Applications (boats, yachts, and small vessels):
Choose Fiberglass: Affordable, flexible, easy to repair.
Structural Reinforcement (bridges, buildings):
Choose FRP: Exceptional strength, durability, minimal maintenance.
Automotive and Lightweight Vehicle Components:
Fiberglass for basic parts (bumpers, panels).
FRP (carbon-based) for performance or racing components due to weight and strength advantages.
Chemical Storage Tanks and Pipes:
Both materials work, but FRP often preferred for more aggressive chemical storage due to higher corrosion resistance.
How to Decide: A Quick Checklist
Before making your choice, consider:
Budget Constraints:
Low-cost → Fiberglass
Higher initial investment with long-term savings → FRP
Strength and Durability Requirements:
Moderate needs → Fiberglass
High structural demands → FRP
Environment and Conditions:
Mild to moderately harsh → Fiberglass
Severe, chemically aggressive → FRP
Installation and Maintenance Complexity:
Simpler and DIY → Fiberglass
More complex or specialized → FRP
Conclusion: Making the Right Choice
Choosing between fiberglass and FRP involves understanding your project’s specific requirements in strength, budget, and environmental exposure. For general-purpose and cost-sensitive applications, fiberglass often suffices. However, when your project demands exceptional performance, strength, or environmental resistance, FRP becomes the superior choice.
To make your final decision confidently:
Identify your critical project priorities (cost, strength, durability).
Assess the environmental conditions your material will face.
Consult with industry experts or suppliers for tailored recommendations.
Ready to get started?
Leave a comment sharing your project details, or share this guide with colleagues to help them make an informed decision!