What Are Fiberglass Septic Tanks?
Fiberglass (FRP) septic tanks are tank products, mainly used to treat domestic sewage. Due to its good anti-corrosion and aging resistance, fiberglass septic tanks have been applied in many places.
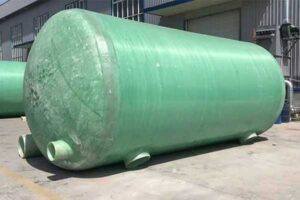
Fiberglass Septic Tanks
There are many methods for making FRP septic tanks, but some processes have obvious defects. Generally, the FRP septic tanks we often use are made by winding and molding. Here are all the methods for making FRP septic tanks.
Hand Lay-Up Process
The hand lay-up process is more suitable for small-batch production. Its production condition is to make the mold of the product and master the technical essentials of the hand lay-up process. Relatively speaking, the hand lay-up process is more suitable for making some products with complex structures.
One characteristic of the FRP hand lay-up process is that tank products need to be produced in sections.
Spray Molding Process
It is a method of manual lamination with the aid of jet machines. Compared with manual hand lay-up, it has higher efficiency and faster production speed and can produce many products with more complex structures. However, the production cost is high, and the requirements for manual operation are very high. To a certain extent, the quality of the finished product depends on the production skills of the workers, and the quality stability is average.
Compression molding process
FRP septic tanks are very suitable for production by the molding process. Before production, resin, stone powder, glass fiber, and other materials need to be made into premixed materials in advance. Then add it to the corresponding mold for extrusion production
Pultrusion process
As mentioned in FRP pultrusion profiles, the pultrusion process is only suitable for making some thin and long profile products, such as FRP square tubes, round tubes, I-beams, channel steel, and other products. For FRP septic tanks, it is not impossible to use the pultrusion process, but the process is more complicated.
winding process
As mentioned above, molding and winding are the two most suitable methods for making FRP septic tanks, but the molding process is only suitable for making some smaller septic tanks. The main reason is that the molding process needs to be opened according to the specifications and models of the product. If the size of the septic tank is too large, it is not suitable to use molding for production.
The winding process is different. The conventional winding process can produce tanks with a diameter of up to 4m. For example, large-scale FRP exhaust gas towers are made using the winding process.