Introduction
Choosing the right reinforcement is no longer just a question of strength—it’s a question of total cost over the life of the structure. In 2025, builders face two dominant options: traditional steel rebar and fiberglass (GFRP) rebar. This article unpacks initial purchase prices, hidden lifetime expenses, and real-world project scenarios so you can decide which material truly saves you more money.
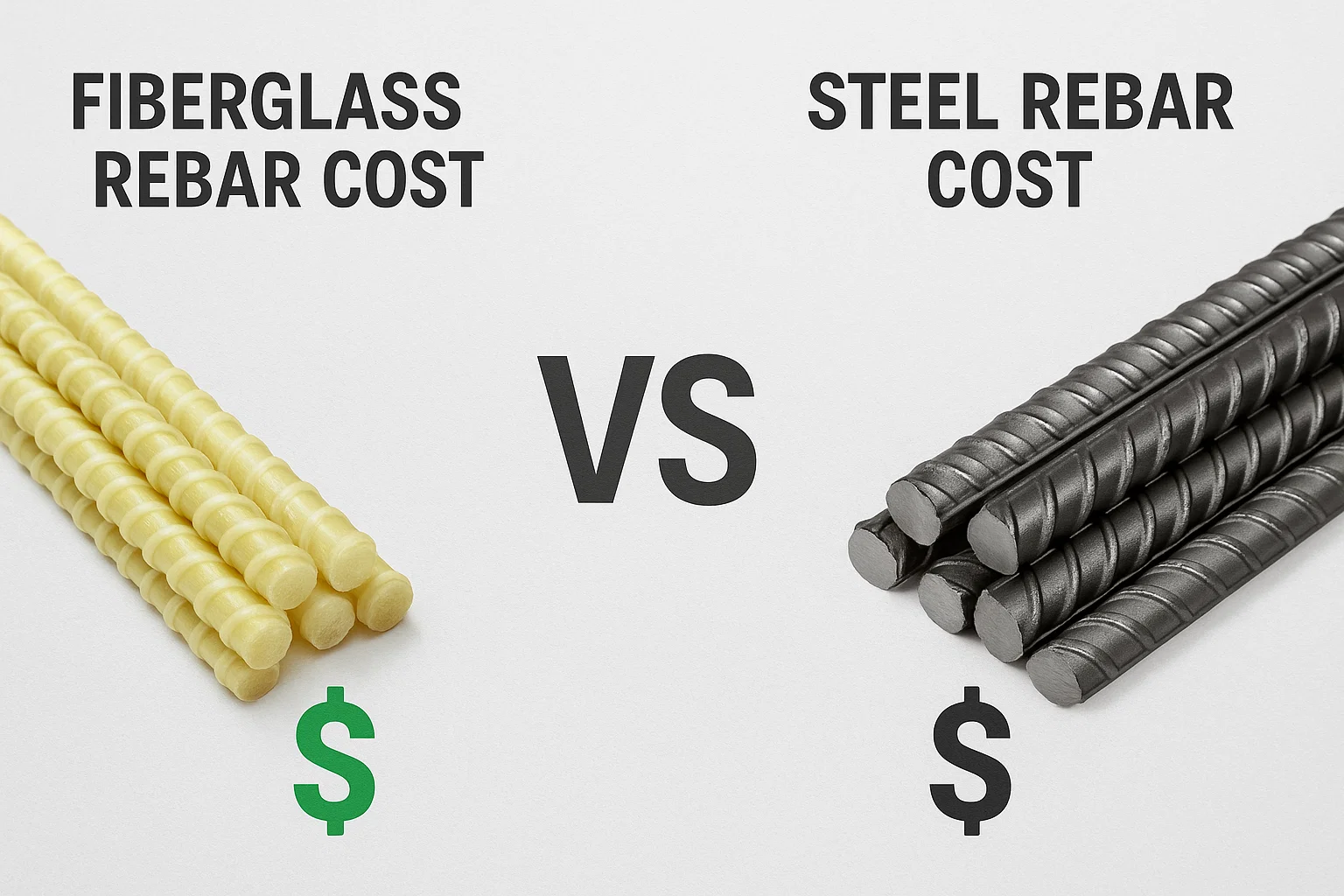
fiberglass rebar cost vs steel
1. Up-Front Cost Breakdown
1.1 Price per Linear Foot
Material | Typical Range (USD/ft) | Mid-Range Example* | |
---|---|---|---|
Steel rebar (#3–#5) | $0.40 – $2.25 | $1.10 | |
Stainless steel rebar | Up to $6.80 | $6.00 | |
Fiberglass (GFRP) rebar | $0.65 – $2.50 | $0.95 |
*Mid-range example is a commonly stocked diameter (#4–#5, ½-⅝″) to keep comparisons fair.
1.2 Bulk & Commodity Pricing
Steel: Spot prices hover around $419/metric ton (≈ $380/short ton) in mid-April 2025, but delivered prices to contractors average $1,300 – $2,000/ton once fabrication, freight, and markup are added.
Fiberglass: Sold by the foot (not ton), but converting typical project bundles shows 35-40 lb of GFRP replaces a ton (2,000 lb) of steel in corrosion-sensitive jobs. Multiplied out, equivalent coverage lands around $1,100 – $1,600 in material—often 5-15 % cheaper than epoxy-coated steel in the same environment.
Key Takeaway: For common diameters, fiberglass is already cost-competitive at the pallet level and beats stainless steel by a wide margin.
2. The Hidden Lifetime Costs You Can’t Ignore
2.1 Corrosion & Maintenance
Steel’s Achilles heel is rust. The Federal Highway Administration estimates corrosion repair costs U.S. bridge owners $8.3 billion annually.ⁱ Every patch, jack-hammered deck, and traffic detour multiplies your true rebar bill. Fiberglass, being non-corrosive, eliminates these future line items—especially valuable in coastal, de-icing-salt, or wastewater applications.
2.2 Labor, Handling & Safety
Weight: Fiberglass weighs ≈ 25 % of steel. Two workers can carry a 20-ft #5 GFRP bar without machinery, cutting crane or skid-steer time.
Cutting: An angle grinder + diamond blade slices GFRP quietly—no sparks, no hot-work permits.
Schedule savings: Jobs using lightweight bar regularly report 10-15 % faster placement, trimming labor budgets by hundreds of crew-hours on mid-size slabs.
2.3 Insurance & Liability
Because fiberglass is electrically non-conductive and non-sparking, it reduces faults when working near live utilities. Many contractors negotiate lower EMR (experience-modification-rate) adjustments after several fiberglass projects, shaving insurance premiums year over year.
“On long-span parking decks, switching to GFRP cut our future maintenance forecast by 30 years.” — David Martin, P.E., senior bridge engineer, ACI 440 committee
3. Project Scenarios Where Fiberglass Wins
Marine & Coastal Concrete
Chloride ingress is relentless; stainless steel is effective but 4-6× the price of GFRP.
DOT Bridge Deck Overlays
Many U.S. states now allow or require fiberglass in the top mat; life-cycle models show $70 k-$150 k savings per 1,000 ft² deck compared with epoxy-coated steel.
MRI & Data Centers
Magnetic neutrality of fiberglass protects sensitive equipment, avoiding extra shielding costs.
Water-/Waste-Treatment Tanks
Eliminates cathodic-protection and coating systems—often a 5-year payback even if steel is cheaper up front.
4. When Steel Remains Economical
Heavily loaded compression members where bar diameters exceed 1″ (fiberglass currently maxes out at #10/#11).
Projects demanding ductile yielding for seismic energy dissipation in plastic hinge zones.
Ultra-short-duration structures (e.g., temporary shoring) where corrosion life-cycle is irrelevant.
Regions with surplus steel or tariffs on imported composite fibers where initial GFRP price is inflated.
5. Beyond Dollars: Code & Performance Checkpoints
Decision Factor | Steel Rebar | Fiberglass Rebar |
---|---|---|
Tensile strength | 60–80 ksi (yield) | 100–150 ksi (ultimate) |
Modulus of elasticity | 29 Msi | 6 Msi |
Magnetic / electric conductivity | Conductive | Non-conductive |
Thermal conductivity | High | Low |
Building codes | ACI 318, AASHTO | ACI 440.11-22, CSA S807 |
Corrosion resistance | Needs coating / CP | Inert |
Note: Lower modulus means larger crack widths can occur with fiberglass; engineers compensate with closer bar spacing or fiber additives.
Conclusion: Which Reinforcement Saves You More Money?
Initial Cost: For #3-#5 bars, GFRP averages 5-15 % cheaper than epoxy-coated steel and orders of magnitude cheaper than stainless.
Lifetime Cost: Zero corrosion + lower labor + lighter handling often delivers 20-40 % total-ownership savings over a 50-year service life.
When to Pick Steel: Very large diameters, seismic ductility zones, or ultra-short service structures.
Ready to Decide?
If your project touches water, de-icing salts, or demands magnetic neutrality, fiberglass rebar is the economical choice in 2025. Have questions about design or local code compliance? Drop a comment below, share this guide with your project team, or subscribe to get our upcoming cost-calculator template delivered straight to your inbox!