Introduction
Fiberglass injection molding has become a go-to process for manufacturers seeking parts that are both lightweight and exceptionally strong. By combining traditional plastic injection molding with fiberglass reinforcement, it delivers a powerful combination of durability and design flexibility. In this article, we’ll explore what fiberglass injection molding is, how it works, and the five major advantages that make it a standout choice for a wide range of applications. Whether you’re a seasoned professional or just starting to consider advanced manufacturing options, this overview will help you decide if fiberglass injection molding aligns with your project’s goals.
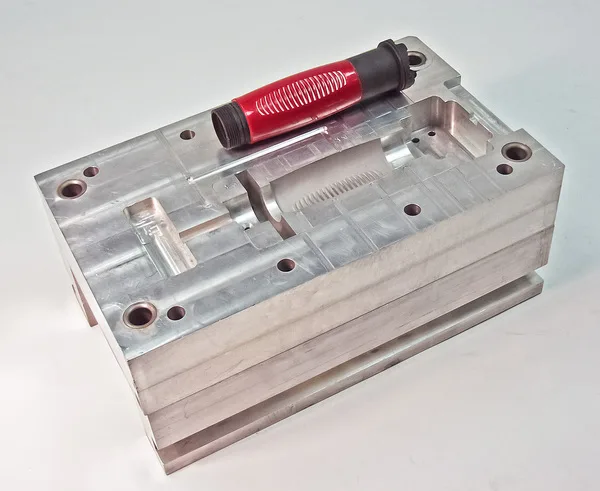
fiberglass injection molding
Understanding Fiberglass Injection Molding
How Fiberglass Injection Molding Works
Fiberglass injection molding is similar to traditional plastic injection molding, but it incorporates fiberglass filaments or chopped strands into the polymer material. Here’s a simplified look at the process:
- Preparing the Material: Thermoplastic resin (e.g., polypropylene, nylon) is mixed with fiberglass reinforcements.
- Heating and Melting: This blend is heated until it melts and forms a uniform consistency.
- Injection into a Mold: The molten material is then injected into a mold cavity under high pressure.
- Cooling and Solidifying: The mold is cooled, allowing the part to solidify and take its final shape.
- Ejection and Finishing: Once the part has cooled sufficiently, it’s ejected from the mold, often requiring minimal post-processing.
By controlling factors such as temperature, pressure, and fiberglass content, manufacturers can achieve consistent, high-quality parts at scale.
The Role of Fiberglass Reinforcement
Fiberglass doesn’t just add bulk to the mix; it significantly enhances the mechanical properties of the final product. The presence of fiberglass strands distributes stress across the part, improving:
- Tensile Strength: The ability of the material to withstand pulling forces without tearing.
- Impact Resistance: How well the part holds up against sudden impacts or stress.
- Thermal Stability: Improved resistance to heat and temperature fluctuations.
This reinforcement feature ensures that components made via fiberglass injection molding often outperform their traditional plastic counterparts in demanding environments.
The 5 Key Advantages
1. Superior Strength-to-Weight Ratio
When it comes to manufacturing, strength and weight often compete: you can get more strength at the cost of more weight—or vice versa. Fiberglass injection molding offers the best of both worlds:
- Strong Yet Lightweight: Fiberglass-reinforced parts can match or exceed the strength of metals, while often weighing up to 70% less.
- High Load-Bearing Capacity: Ideal for applications in automotive, aerospace, and consumer electronics where materials must withstand stress but remain lightweight for efficiency or user comfort.
This unbeatable strength-to-weight ratio not only leads to better performance but also results in potentially lower shipping costs and easier handling during production and assembly.
2. Cost-Effectiveness in Manufacturing
Fiberglass injection molding can be highly cost-effective once the initial setup is complete. According to a 2023 market analysis by MarketsandMarkets, global demand for fiberglass-reinforced components is expected to rise by 5.8% annually, partly due to the process’s favorable cost dynamics.
- Lower Labor Costs: The automated nature of the process reduces the need for manual labor.
- High Production Speed: Once molds are designed and tested, large volumes of parts can be produced quickly.
- Reduced Defect Rates: Thanks to precise temperature and pressure control, scrap rates are often lower than in other manufacturing methods.
Upfront investment in the mold might be relatively high, but when you factor in large production runs and reduced waste, the return on investment can be substantial.
3. Versatility Across Industries
One of fiberglass injection molding’s most appealing qualities is its adaptability to various industrial sectors, including:
- Automotive: Dashboard components, under-the-hood parts, and structural elements benefit from fiberglass’s resilience and lighter weight.
- Aerospace: Cabin parts, seating, and other interior fittings are often made from fiberglass-reinforced thermoplastics to save weight and fuel costs.
- Consumer Goods: Durable, lightweight casings for electronics and household appliances.
- Construction: Panels, ducts, and structural elements for buildings and infrastructure projects.
This broad applicability makes fiberglass injection molding a strong contender for businesses looking to standardize their material choices across different product lines.
4. Reduced Material Waste
In today’s manufacturing landscape, sustainability is more than just a buzzword; it’s a significant factor influencing consumer and corporate decisions. Fiberglass injection molding helps address this concern in several ways:
- Precise Injection: The high-pressure injection process ensures that the exact amount of material needed fills the mold, minimizing excess.
- Reusability of Scrap: Any leftover material or defective parts can often be reground and recycled into future production batches.
- Longevity: Fiberglass-reinforced parts tend to last longer, reducing the need for frequent replacements.
By lowering waste, companies can not only cut costs but also market their efforts toward creating more eco-friendly manufacturing processes.
5. Customization and Complex Design Capabilities
A final key advantage is the process’s ability to create complex shapes with ease. Fiberglass injection molding offers:
- Intricate Geometry: Threads, grooves, and precise details are possible in a single, consistent molding cycle.
- Surface Textures: Mold surfaces can be designed to produce textured or glossy finishes, cutting down post-processing steps.
- Additive Possibilities: Beyond fiberglass, manufacturers can add flame retardants, pigments, or UV stabilizers to fine-tune the material for specific applications.
This flexibility in design and material composition means you can tailor parts to exact performance requirements, aesthetics, and branding, all while maintaining structural integrity.
Maintenance and Quality Control
While fiberglass injection molding is highly efficient, regular maintenance and strict quality control measures keep the process running smoothly. Key focus areas include:
- Mold Care: Proper cleaning and inspection of molds to avoid blockages or deformities.
- Material Handling: Consistent fiber distribution in the thermoplastic resin to maintain uniform part performance.
- Process Parameters: Monitoring injection temperatures, pressures, and cooling times to ensure part consistency.
Setting up a robust quality control plan ensures that each production cycle runs optimally and that end products meet safety and performance standards.
Conclusion
Fiberglass injection molding stands out for its combination of lightness and strength, cost-efficiency, and design versatility. From automotive components to consumer goods, it opens doors to applications demanding high durability without the burden of excessive weight. By investing in the right molds, materials, and quality control protocols, businesses can significantly benefit from its advantages.
If you found these insights valuable, feel free to share this article with your network or leave a comment below. Your feedback helps us tailor our content to better serve your manufacturing and design needs. Stay connected for more industry updates, and don’t hesitate to reach out if you have questions or success stories to share!