Introduction
Fiberglass car molds are at the heart of many automotive customization projects, enabling hobbyists and professionals alike to craft stunning, durable, and lightweight parts. Whether you’re designing custom body kits or restoring a classic vehicle, understanding fiberglass molds is essential for achieving precision and quality. This guide breaks down everything you need to know about fiberglass car molds, making it easy for beginners to get started.
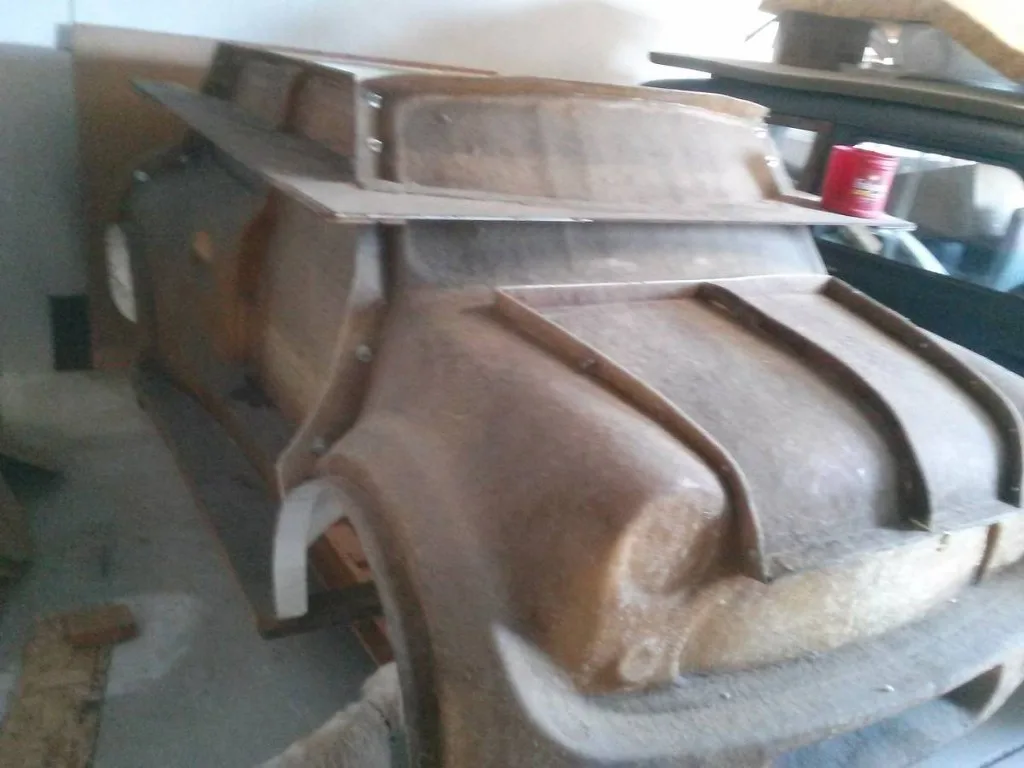
fiberglass car molds
What Are Fiberglass Car Molds?
Fiberglass car molds are specialized forms or templates used to create car parts and panels. These molds act as the negative shape into which fiberglass material is laid and cured to produce a finished component. Commonly used in custom automotive projects, fiberglass molds allow for consistent replication of designs, making them ideal for mass production and one-off customizations.
The molds can be used to create a variety of components, such as hoods, fenders, bumpers, and interior panels. Their versatility and affordability make them a go-to choice for many automotive enthusiasts.
History of Fiberglass in Automotive
The adoption of fiberglass in the automotive industry dates back to the mid-20th century. Initially popularized for its lightweight and corrosion-resistant properties, fiberglass became a preferred material in motorsports and custom car building. Iconic cars, such as the Chevrolet Corvette, showcased the potential of fiberglass construction, setting the stage for its widespread use in mold-making and part fabrication.
How Fiberglass Car Molds Are Made
Creating a fiberglass car mold involves several steps:
- Designing the Model: Begin with a 3D model or a prototype of the desired part.
- Preparing the Plug: The plug is the positive version of the part, made from materials like wood, foam, or existing car parts.
- Applying Release Agent: Coat the plug with a release agent to prevent sticking.
- Laying Fiberglass Layers: Layer fiberglass cloth or mat onto the plug and apply resin to bond it.
- Curing the Mold: Allow the resin to harden, ensuring structural integrity.
- Finishing Touches: Sand and polish the mold to ensure smoothness and precision.
This process requires patience and attention to detail, but the results are well worth the effort.
Advantages of Fiberglass Car Molds
Fiberglass car molds offer numerous benefits, including:
- Durability: Fiberglass is strong and long-lasting.
- Lightweight: Easy to handle and ideal for automotive applications.
- Cost-Effective: Affordable compared to other mold-making materials.
- Customizable: Allows for intricate designs and modifications.
These features make fiberglass molds a cornerstone of both professional and DIY automotive projects.
Applications in Automotive Customization
Fiberglass car molds are versatile tools in the automotive world, serving a variety of purposes:
- Custom Body Parts: Enthusiasts use fiberglass molds to create unique hoods, bumpers, spoilers, and fenders. These parts not only enhance a car’s appearance but also improve aerodynamics.
- Prototypes: Automotive designers rely on fiberglass molds to produce prototype parts during the development phase of a new vehicle. This process allows for testing and refinement before final production.
- Repairs: Damaged car parts, particularly those made from fiberglass, can be replicated and replaced using custom molds.
- Interior Components: Dashboards, door panels, and center consoles are often crafted using fiberglass molds for precision and durability.
Whether you’re enhancing performance or aesthetics, fiberglass molds provide the flexibility to bring your creative visions to life.
Materials Needed for Fiberglass Car Molds
Before you start, gather the necessary materials and tools:
- Fiberglass Fabric: Choose between woven roving, chopped strand mat, or biaxial cloth based on the required strength and finish.
- Resin: Polyester resin is commonly used for its affordability, but epoxy resin offers better durability and adhesion.
- Gelcoat: Applied to the mold’s surface to create a smooth finish.
- Release Agent: Prevents the fiberglass from sticking to the plug or mold.
- Tools: Brushes, rollers, mixing cups, and sandpaper are essential for handling and shaping the materials.
Investing in high-quality materials ensures a more reliable and professional outcome for your project.
Design Considerations for Fiberglass Molds
Precision is paramount when designing fiberglass car molds. Key considerations include:
- Accurate Dimensions: Ensure the mold’s dimensions match the intended part exactly. Small errors can lead to fitment issues.
- Structural Integrity: Reinforce the mold where necessary to prevent warping or breaking during repeated use.
- Surface Finish: A polished mold ensures smooth, high-quality parts.
- Draft Angles: Incorporate slight angles to facilitate the easy removal of parts from the mold.
A meticulous design process reduces errors and ensures a seamless fabrication experience.
Safety Precautions During Fabrication
Working with fiberglass materials requires strict safety measures to avoid health and environmental hazards:
- Ventilation: Always work in a well-ventilated area to avoid inhaling toxic fumes from resins and gelcoats.
- Protective Gear: Wear gloves, goggles, and a respirator mask to protect your skin, eyes, and lungs.
- Fire Safety: Keep flammable materials away from open flames, as some resins and solvents are highly flammable.
- Disposal: Dispose of waste materials according to local environmental regulations to minimize pollution.
Prioritizing safety not only protects you but also ensures a smoother workflow.
Common Challenges and How to Overcome Them
Fiberglass mold-making comes with its own set of challenges. Here are some common issues and their solutions:
- Warping: Reinforce the mold to prevent deformation during curing.
- Air Bubbles: Use rollers to eliminate trapped air between fiberglass layers.
- Cracking: Avoid excessive force when removing parts; use a release agent generously.
- Incomplete Curing: Ensure proper resin-to-catalyst ratios and curing conditions.
With practice and attention to detail, even beginners can overcome these hurdles and produce professional-grade molds.
Maintenance of Fiberglass Car Molds
To extend the life of your fiberglass molds:
- Cleaning: Remove any residue or debris after each use with a soft cloth and cleaning agent.
- Repairs: Address minor cracks or chips immediately using resin and fiberglass patches.
- Storage: Store molds in a dry, temperature-controlled environment to prevent moisture damage and warping.
Regular maintenance keeps your molds in top condition for repeated use.
Comparing Fiberglass to Alternative Mold Materials
Fiberglass molds aren’t the only option for automotive projects. Here’s how they stack up against other materials:
Material | Advantages | Disadvantages |
---|---|---|
Fiberglass | Affordable, lightweight, versatile | Limited heat resistance |
Metal | Extremely durable, heat resistant | Expensive, heavy, harder to work with |
Plastic | Lightweight, easy to shape | Less durable, not ideal for high stress |
Carbon Fiber | High strength-to-weight ratio | Very expensive, complex to produce |
For most DIY and small-scale projects, fiberglass strikes the perfect balance between cost and functionality.
Environmental Impact of Fiberglass Molds
Fiberglass mold-making does pose some environmental concerns, such as waste generation and non-biodegradable materials. However, there are ways to reduce your environmental footprint:
- Recycling Fiberglass: Some companies specialize in recycling fiberglass waste into new materials.
- Eco-Friendly Resins: Opt for low-VOC or bio-based resins when possible.
- Efficient Use: Plan projects carefully to minimize excess material usage.
Sustainable practices ensure a greener approach to automotive customization.
Future Trends in Fiberglass Mold Technology
Innovations in fiberglass mold-making are transforming the industry:
- 3D Printing: Using 3D-printed plugs to speed up mold creation.
- Automation: Robotic systems for precise layering and curing of fiberglass.
- Smart Resins: Development of self-healing and environmentally friendly resin formulations.
These advancements make mold-making faster, more efficient, and environmentally responsible.
Tips for Beginners Starting with Fiberglass Molds
If you’re new to fiberglass mold-making, follow these tips:
- Start small with basic projects to gain confidence.
- Watch online tutorials or take workshops to learn practical techniques.
- Use high-quality materials to reduce frustrations and improve results.
- Practice patience; rushing can lead to costly mistakes.
Every expert was once a beginner, so don’t be afraid to experiment and learn from your experiences.
Frequently Asked Questions (FAQs)
1. How long does it take to make a fiberglass car mold?
The process can take several days to weeks, depending on the complexity and curing times.
2. Can fiberglass molds withstand high temperatures?
Fiberglass molds have moderate heat resistance but are unsuitable for extremely high-temperature applications.
3. Are fiberglass molds reusable?
Yes, with proper care and maintenance, fiberglass molds can be reused multiple times.
4. What’s the cost of creating a fiberglass car mold?
Costs vary based on size, materials, and tools but typically range from $50 to several hundred dollars.
5. Can I make a mold from an existing car part?
Absolutely! Many DIY enthusiasts create molds from existing parts using release agents to prevent sticking.
6. Is fiberglass safe to work with?
Yes, provided you follow safety precautions like wearing protective gear and working in a ventilated area.
Conclusion
Fiberglass car molds are an invaluable tool for automotive customization, combining versatility, durability, and affordability. Whether you’re a seasoned professional or an eager beginner, mastering the art of mold-making opens the door to endless creative possibilities. So, roll up your sleeves, gather your materials, and start crafting your dream car components today!