Fiberglass body molds are a versatile and durable solution for creating custom parts, especially in industries like automotive, marine, and even home construction. Whether you’re crafting a custom car panel or a unique boat hull, fiberglass body molds offer a combination of strength, flexibility, and ease of use that make them ideal for precision work. This article walks you through the step-by-step process of crafting fiberglass body molds, ensuring you can bring your designs to life with professional quality.
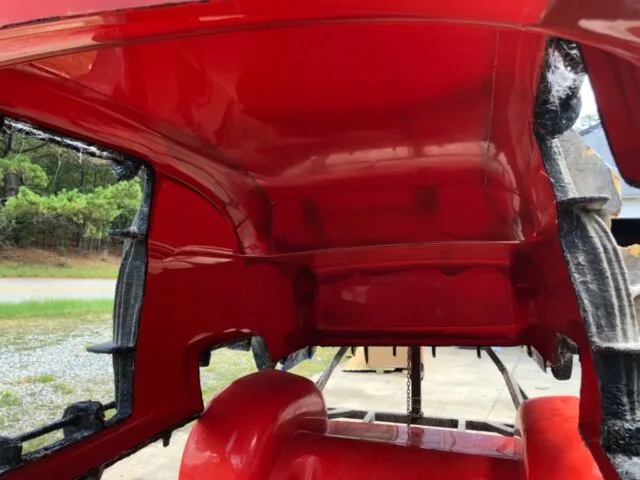
fiberglass body molds
What are Fiberglass Body Molds?
Fiberglass body molds are forms or templates used to replicate parts made of fiberglass, a lightweight but strong material that is widely used in a variety of industries. These molds are typically created from an original design or model, known as a “plug.” Once made, the fiberglass mold can be used to produce multiple copies of a part, making it ideal for custom manufacturing projects.
Applications for fiberglass body molds are vast. They are commonly used in the automotive industry for creating custom car parts, in boat building, and even for architectural components. Due to their strength and durability, fiberglass body molds can withstand repeated use without wearing down, making them an economical choice for custom design work.
Advantages of Using Fiberglass for Body Molds
Fiberglass is a preferred material for making molds because it combines several key advantages:
- Durability and Strength: Fiberglass molds are highly durable and can last through numerous production cycles. This makes them a reliable choice for repeated use in industries like automotive manufacturing and marine construction.
- Cost-Effective: Compared to other mold-making materials such as metal, fiberglass is significantly more cost-effective. While fiberglass molds require an initial investment, their long-lasting nature ensures that the cost per part remains low over time.
- Lightweight Yet Strong: Despite its lightweight properties, fiberglass is incredibly strong. This makes it easy to handle and maneuver while maintaining the structural integrity needed to create precise molds.
- Customizable: Fiberglass can be molded into nearly any shape, making it a highly versatile option for custom parts. Whether you need a mold for a vehicle body panel or a complex boat design, fiberglass can adapt to meet your specifications.
These benefits make fiberglass an excellent material for crafting body molds, especially in custom design projects where precision and durability are paramount.
The Step-by-Step Process of Creating Fiberglass Body Molds
Creating fiberglass body molds requires careful planning and execution. Follow these steps to produce a high-quality, custom fiberglass mold.
Step 1: Design and Planning
Before you can begin creating a fiberglass mold, you need to design and plan your project. This involves creating a detailed blueprint or 3D model of the part you want to replicate. The design phase is crucial because any flaws or inconsistencies at this stage will carry over into the final mold.
Step 2: Creating the Plug or Model
The plug is the original model from which the fiberglass mold will be made. This can be created using materials such as clay, foam, or wood. Ensure that the plug is smooth and accurately reflects the final part’s dimensions and details. The better the quality of your plug, the better the resulting fiberglass mold.
Step 3: Applying Mold Release
Once the plug is ready, the next step is to apply a mold release agent. This substance prevents the fiberglass from sticking to the plug, ensuring a clean separation once the mold is cured. A smooth, even coat of mold release is essential to avoid damaging the plug or mold during the separation process.
Step 4: Laying Fiberglass Layers
The next step is to lay the fiberglass cloth over the plug. You will need to apply several layers of fiberglass to achieve the desired strength and durability. Mix the fiberglass resin and hardener, then carefully apply it to the cloth, ensuring an even distribution over the plug. Use a roller to remove any air bubbles, as these can weaken the mold.
Step 5: Curing and Finishing
Once the fiberglass has been applied, allow it to cure fully. Depending on the resin used, this can take anywhere from several hours to a full day. After curing, gently remove the mold from the plug. The mold may require some finishing work, such as sanding or applying a gel coat, to ensure a smooth surface.
With the mold complete, it is now ready to be used for creating custom parts. Simply apply the mold release agent to the interior of the fiberglass mold, lay new fiberglass cloth inside, and repeat the process for producing your final parts.
Common Challenges and How to Overcome Them
Creating fiberglass body molds isn’t without its challenges, but most issues can be avoided with careful attention to detail.
- Air Bubbles: One of the most common problems is air bubbles forming during the application of the fiberglass layers. These can weaken the mold or result in imperfections. To avoid this, use a roller to press down the fiberglass and push out any trapped air while applying the resin.
- Warping During Curing: If the mold or plug warps during the curing process, it can result in an uneven mold. To prevent this, ensure that the mold is supported evenly during the curing stage. Avoid placing the mold under direct sunlight or high temperatures, as this can cause uneven curing.
- Repairing Imperfections: After the mold is cured, small imperfections may appear. These can be sanded down and filled with additional fiberglass resin to ensure a smooth, finished product. Don’t skip this step, as a smooth surface is key to producing high-quality final parts.
Conclusion
Fiberglass body molds are a powerful tool for crafting custom designs, offering versatility, durability, and cost-effectiveness. By following the step-by-step process outlined above, you can create reliable molds for producing custom vehicle parts, marine components, or any other project requiring precision and durability. Whether you’re a DIY enthusiast or a professional in need of specialized parts, fiberglass molds provide the perfect balance between strength and flexibility.
Ready to start your next project? Take the plunge and create your own custom fiberglass body molds or consult with industry experts to get the perfect design. The possibilities are endless!