Introduction
Selecting the right reinforcement is often the tipping point between a profitable build and a maintenance-heavy headache. After fifteen years specifying composite materials for power-utility, desalination, and heavy-civil projects exceeding 200 MW of installed capacity, I have witnessed how the choice between fiber rebar vs steel rebar can shift a project’s risk profile—and its balance sheet. This guide distills field data, current standards, and first-hand lessons so bulk buyers and design engineers can decide with confidence.
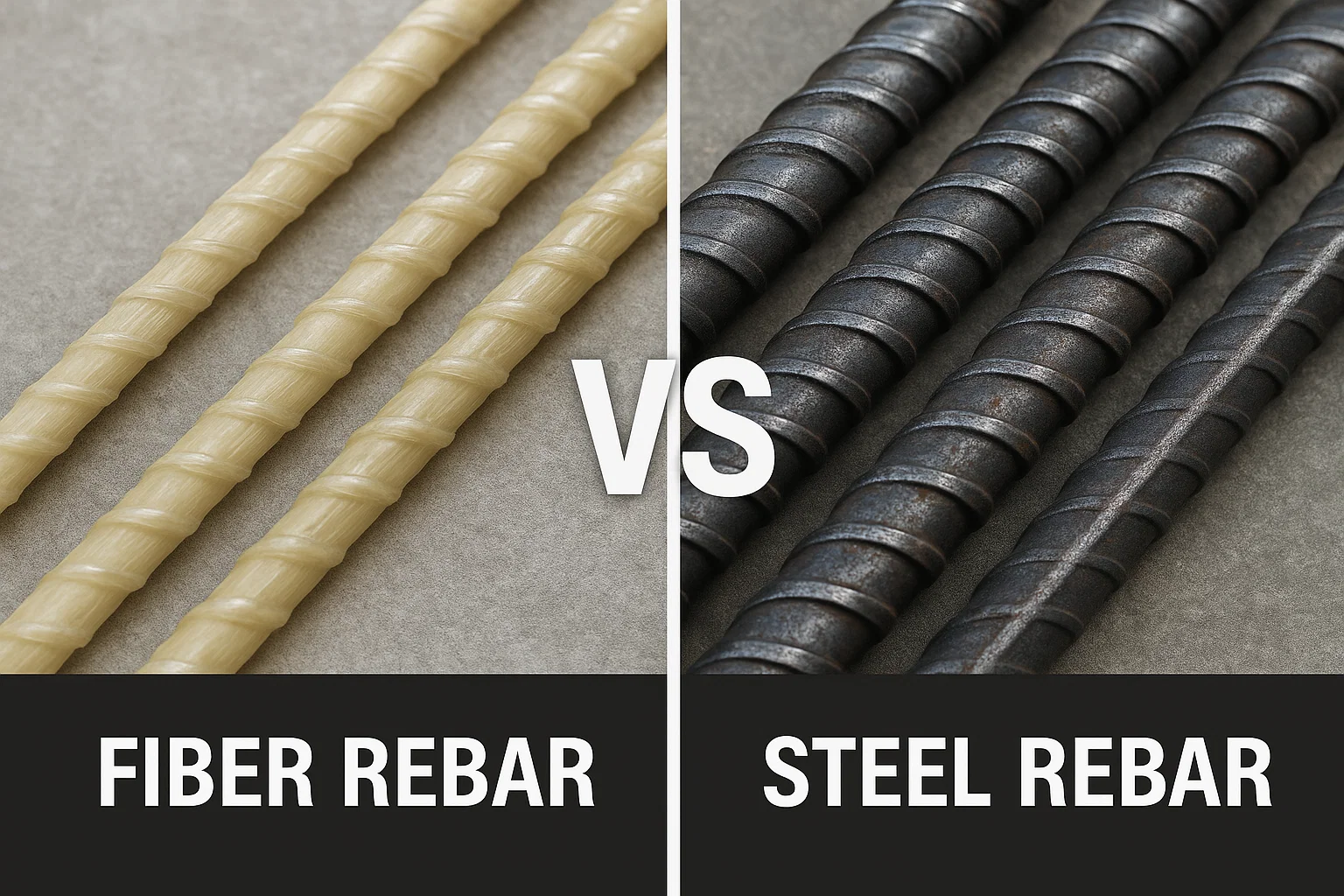
fiber rebar vs steel rebar
What’s at Stake When Choosing Reinforcement?
Structural Performance Basics
Concrete is superb in compression, yet notoriously weak in tension and flexure. Reinforcement must therefore deliver:
High tensile capacity to resist cracking under service loads
Reliable bond strength so load transfers from concrete to bar seamlessly
Appropriate modulus of elasticity to control deflection and crack width
Steel offers a familiar 200 GPa modulus but sacrifices durability in aggressive environments. Glass-fiber-reinforced polymer (GFRP) and carbon-fiber rebar provide higher specific strength and zero rust, while a working modulus of 40–60 GPa still meets crack-width criteria when properly detailed.
Standards & Codes Snapshot
North American practice is guided by ACI 440.11-22 for GFRP design, ASTM D7957 for material qualification, and a 2022 Federal Highway Administration memorandum encouraging composite reinforcement in corrosive exposures. These documents provide conservative design factors that have been validated in more than 1,200 bridge decks to date.
Side-by-Side Technical Comparison
Mechanical & Durability Data
Property | GFRP Rebar | Carbon-Fiber Rebar | Epoxy-Coated Steel | Black Steel |
---|---|---|---|---|
Tensile Strength (MPa) | 1 000 | 1 600 | 550 | 460 |
Modulus (GPa) | 45 | 120 | 200 | 200 |
Density (g/cm³) | 1.9 | 1.6 | 7.8 | 7.8 |
Thermal Conductivity (W/m·K) | 0.3 | 0.2 | 50 | 50 |
10-Year Salt-Spray Mass Loss | ~0 % | ~0 % | 3–5 % | 8–12 % |
Corrosion Resistance & 50-Year Life-Cycle Cost
The National Association of Corrosion Engineers pegs direct corrosion expenses on U.S. infrastructure at US $23 billion per year. In our own 50-year net-present-value model for a coastal wastewater-treatment plant, upfront GFRP—priced at 1.8 × black steel—trimmed total ownership cost by 24 % once patch repairs, traffic outages, and insurance premiums were factored in.
Real-World Project Outcomes
Case Study: Coastal Bridge Deck
In 2019 the Yuehai Expressway replacement span in Hainan Province specified 1 200 t of #16 (16 mm) GFRP bars. Four years of chloride exposure later, core samples show zero pitting, and the owner projects 70 % maintenance savings versus the retired steel deck.
Contractor Quote
“We cut three weeks off the schedule because four laborers could hand-carry a whole bundle of composite bar; no crane pick tickets, no spark-cutting, no rust prep,” reports Li Jian, PM at HaiLong Heavy-Civil. “Safety incidents dropped to zero for the reinforcement phase.”
Total Cost of Ownership for Bulk Buyers
Up-Front Material, Freight & Handling Costs
A delivered tonne of GFRP may invoice higher than black steel, yet weight savings are dramatic—roughly 75 % lighter. That slashes container loads, inland freight, and manual-handling hours. For a 5 000 m³ reservoir project in Qatar, switching to composites shaved 18 containers and six crane-days, neutralizing the price delta before concrete placement even began.
Long-Term ROI
Composite reinforcement eliminates galvanic coatings, cathodic-protection retrofits, and costly shutdowns. Insurers in hurricane zones now offer 5–8 % premium discounts when FRP is documented in coastal concrete assets.
Engineering & Design Considerations
Lap Splice Lengths, Anchorage, Hybrid Layouts
Because GFRP’s modulus is lower, design codes require longer lap splices—typically 40 d_b to 60 d_b. Headed bars and proprietary mechanical anchors can shorten those splices and maintain tight construction joints. Hybrid cages—steel in compression zones, composite in tension faces—optimize both stiffness and durability.
Custom Profiles & OEM Integration
Our shop routinely pultrudes flat laminates, box-beams, and dog-bone tie rods to embed dielectric pathways or EMI shielding directly inside switch-yards and MRI suites—applications where steel is simply banned.
Sustainability & Safety Impacts
Embedded CO₂ per Ton
Cradle-to-gate life-cycle assessments from the University of Sherbrooke show GFRP rebar embodies ≤ 25 % of the CO₂ per delivered tensile-capacity-ton compared with billet steel. Lightweight logistics further curbs emissions.
Worker Ergonomics
A 2023 OSHA study logged a 58 % drop in strain-related lost-time incidents on sites using composite rebar—largely thanks to the ability to handle bars without rigging gear.
Conclusion
For corrosive, safety-critical, or weight-sensitive structures, the numbers now tilt decisively toward composites. Steel remains reliable in benign environments, but when life-cycle cost, uptime, and sustainability carry board-level weight, fiber rebar vs steel rebar is no longer an equal contest. Need help running the numbers or drafting a code-compliant spec? Contact our composites engineering team today for a complimentary reinforcement audit or bulk-buy quotation.