Introduction
In recent years, molded fiberglass has become a cornerstone material in various industries due to its unique properties and versatility. From automotive parts to construction materials, fiberglass is favored for its strength, durability, and lightweight characteristics. This composite material, made from fine fibers of glass combined with a resin matrix, offers a range of benefits that make it an ideal choice for both industrial and consumer applications. In this article, we’ll explore the wide range of applications for molded fiberglass, delve into its many benefits, and provide an overview of the manufacturing process that brings this material to life.
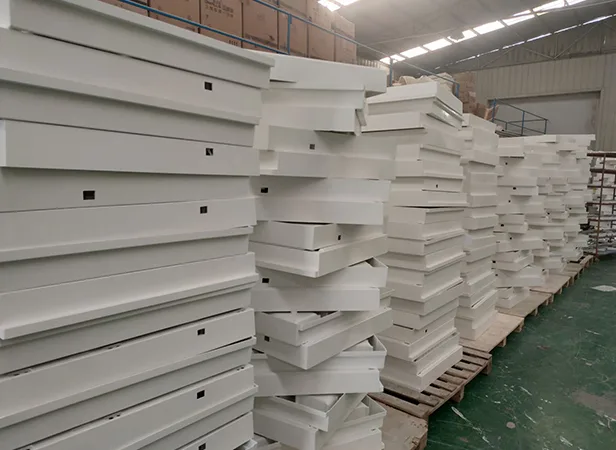
molded fiberglass
Applications of Molded Fiberglass
Molded fiberglass is widely used across numerous industries due to its adaptability and performance. In the automotive sector, it is commonly employed to manufacture body panels, hoods, and other exterior components. The construction industry also relies heavily on fiberglass for products like roofing panels, insulation, and water tanks. Additionally, molded fiberglass is used in the production of marine vessels, sports equipment, and even wind turbine blades. Its ability to withstand harsh environments makes it a preferred choice in these demanding applications.
- Automotive Industry: Molded fiberglass is used to create lightweight yet durable components like bumpers, body panels, and engine covers. Its corrosion resistance makes it particularly suitable for parts exposed to the elements.
- Construction Industry: In construction, fiberglass is utilized for insulation, roofing, and siding due to its excellent thermal properties and durability. It is also used in the production of architectural elements, such as columns and facades, that require both strength and aesthetic appeal.
- Marine Applications: The marine industry benefits from fiberglass’s resistance to water and salt, making it ideal for boat hulls, decks, and other structural components.
- Sports Equipment: Many sports equipment manufacturers use fiberglass to produce high-performance products such as helmets, skis, and surfboards, taking advantage of its strength and flexibility.
Benefits of Molded Fiberglass
One of the primary reasons molded fiberglass is so popular is its impressive list of benefits. Unlike metals, fiberglass does not corrode, making it ideal for use in environments where exposure to moisture and chemicals is common. Its lightweight nature allows for easier handling and installation, which can lead to cost savings in both transportation and labor. Furthermore, molded fiberglass is known for its high strength-to-weight ratio, making it a durable option that can withstand significant stress without compromising performance.
- Durability: Molded fiberglass is highly durable, withstanding extreme temperatures, UV exposure, and mechanical wear and tear, making it suitable for long-term use in various environments.
- Corrosion Resistance: Fiberglass does not rust or corrode, unlike metals, making it a superior choice for applications exposed to moisture, chemicals, or saltwater.
- Lightweight: Despite its strength, fiberglass is relatively lightweight, which reduces shipping costs and simplifies installation processes.
- Customizability: Fiberglass can be easily molded into complex shapes and sizes, allowing for custom designs that meet specific needs.
The Manufacturing Process of Molded Fiberglass
The manufacturing process of molded fiberglass involves several key steps, beginning with the creation of a mold based on the desired shape of the final product. The most common methods include open mold and closed mold processes. In open mold manufacturing, fiberglass layers are manually laid into a mold and then saturated with resin to create a solid structure. Closed mold processes, such as resin transfer molding (RTM), involve injecting resin into a mold that contains a fiberglass mat, allowing for more precise control over the final product’s thickness and strength.
- Open Mold Process: This method involves layering fiberglass mats or fabrics into a mold, which is then saturated with resin. The resin hardens, creating a strong, lightweight structure. This process is typically used for larger components that do not require extremely tight tolerances.
- Closed Mold Process: In the RTM method, resin is injected into a closed mold containing fiberglass reinforcement. This process allows for better control over the material’s properties and is often used for parts that require high precision.
- Pultrusion: A continuous molding process where fiberglass strands are pulled through a resin bath and then through a heated die, creating long, straight parts like rods, beams, and channels.
Custom Fiberglass Molding
For businesses with specific needs, custom fiberglass molding offers a tailored solution. This process allows companies to create unique products that meet exact specifications, whether for industrial use, architectural applications, or consumer products. The flexibility of fiberglass molding makes it possible to produce intricate shapes and complex designs that would be difficult or impossible to achieve with other materials.
- Flexibility in Design: Custom fiberglass molding allows for the creation of complex and unique shapes, providing designers with more creative freedom.
- Cost-Effectiveness: Once the mold is created, producing multiple units of the same design is cost-effective, making it an ideal choice for large-scale manufacturing.
- Versatility: Custom molds can be used to produce everything from small components to large structural elements, depending on the needs of the project.
Conclusion
Molded fiberglass is a versatile and highly beneficial material that plays a crucial role in various industries. From its diverse applications to the numerous advantages it offers, including durability, corrosion resistance, and lightweight properties, fiberglass continues to be a material of choice for many. Whether you’re looking for custom solutions or simply exploring the benefits of this remarkable material, molded fiberglass is sure to meet the demands of modern manufacturing and design.