Introduction
Choosing the right industrial grating has huge implications for worker safety, maintenance budgets, and long-term durability. Two front-runners dominate most shortlists—expanded fiberglass grating (often called FRP or GRP grating) and traditional carbon‐steel grating. Both have loyal advocates, but each material excels in different scenarios. This article compares them head-to-head so you can make a confident, data-driven decision.
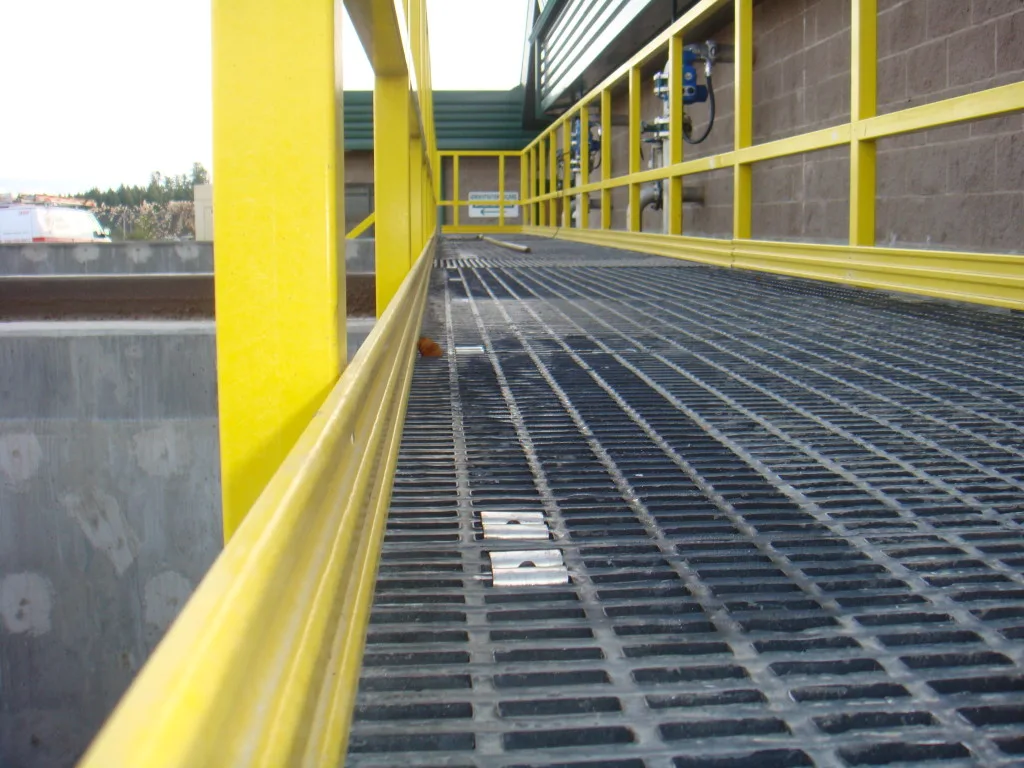
expanded fiberglass grating
Expanded Fiberglass Grating Overview
Expanded fiberglass grating is created by impregnating continuous glass fibers with thermosetting resins, then expanding or pultruding the sheet into a rigid lattice. The result is a non-conductive, corrosion-proof panel that weighs roughly one-quarter as much as steel while matching or exceeding its tensile strength.
Typical open-area ratio: 60 – 70 %
Tensile strength: up to 75,000 psi (depending on resin system)
Density: 1.9 g/cm³ (≈ 70 % lighter than steel)
Steel Grating Overview
Steel grating is usually fabricated by welding or pressure-locking flat steel bars and crossbars into a high-load panel. Galvanizing or painting offers moderate corrosion protection, but the core strength relies on the inherent stiffness of carbon or stainless steel.
Typical open-area ratio: 65 %
Yield strength (mild steel): 36,000 psi
Density: 7.85 g/cm³
Comparison Criteria
Strength & Load-Bearing Capacity
Expanded fiberglass grating delivers impressive load ratings—up to 3,000 lb/ft² for pedestrian platforms—thanks to its continuous-fiber reinforcement. Still, heavy vehicular traffic (forklifts, trucks) favor steel, whose modulus of elasticity (29 Msi) eliminates deflection under concentrated wheel loads.
Quick rule: If deflection under < ¹/₂″ is mission-critical, steel wins. For pedestrian or light-equipment areas, FRP matches required loads with greater safety margins.
Corrosion Resistance & Durability
According to the National Association of Corrosion Engineers, corrosion costs global industry ≈ US $2.5 trillion each year—and grating installed over water or chemicals is a frequent casualty. FRP’s inert glass-fiber/resin matrix laughs at salt spray, acids, and chlorine. Welding-repair cycles common to steel disappear; color-through pigments hide scratches.
Steel can last decades in indoor, low-moisture areas, but even hot-dip galvanizing eventually fails in coastal or wastewater environments.
Weight & Handling
Weight per square foot: FRP ≈ 3 lb | Steel ≈ 9–12 lb
Crew size: FRP panels up to 4´ × 12´ can be carried by one person; steel usually needs two or a forklift.
Installation cost: Field cutting FRP requires only a carbide blade and dust mask; steel demands torches or saws plus post-cut coating touch-ups.
Safety & Slip Resistance
OSHA recommends a minimum coefficient of friction (COF) of 0.5 for walking surfaces. Molded-in silica grit gives fiberglass grating a dry COF ≈ 0.8 and wet COF ≈ 0.6, outperforming serrated steel (≈ 0.55 dry, 0.45 wet). FRP is also non-sparking and non-conductive—critical in electrical substations or offshore rigs.
Maintenance & Lifecycle Cost
Steel’s upfront material cost is lower by 10–20 %, but ongoing expenses—repainting, rust remediation, and potential downtime during repairs—tip the scales. Independent facility audits show that over a 20-year service life, expanded fiberglass grating costs up to 34 % less than painted steel and 18 % less than galvanized steel.
Environmental Impact
Fiberglass grating’s low weight slashes transport emissions, and many manufacturers now offer recycled-glass content. Steel is infinitely recyclable, but its production is energy-intensive. Life-cycle assessments typically credit FRP with a 25 % smaller carbon footprint for installations that avoid corrosion-driven replacement.
When to Choose Expanded Fiberglass Grating
Constant exposure to chemicals, saltwater, or moisture (wastewater plants, marinas, chemical processing)
Platforms where manual handling or rapid retrofits are required
Electrical or explosive environments demanding non-conductivity and spark-free work areas
Facilities seeking low-noise walkways (FRP dampens vibration better than steel)
Owners aiming for long-term lifecycle savings and minimal maintenance
When to Choose Steel Grating
Heavy truck or forklift traffic exceeding pedestrian load ratings
Situations where extreme temperature cycling (cryogenic to high heat) may challenge thermoset resins
Projects with tight capital budgets and readily available corrosion-control programs
Architectural applications where a metallic aesthetic is preferred
Conclusion & Call to Action
Expanded fiberglass grating excels in corrosive, safety-critical, and weight-sensitive environments, delivering lower lifecycle cost and superior slip resistance. Steel grating remains unbeatable for heavy vehicle loads and high-heat scenarios. By weighing your facility’s specific load, chemical, and maintenance conditions, you can select the grating that truly delivers superior performance.
Have questions about specifying or installing expanded fiberglass grating? Leave a comment below, share this guide with your maintenance team, or subscribe to our newsletter for more hands-on insights and cost-saving tips!