Introduction
Custom molded fiberglass has become a cornerstone in various industries due to its unmatched strength, versatility, and durability. Whether it’s used in the automotive, marine, or construction sectors, custom molded fiberglass is the material of choice for many manufacturers looking to produce high-quality, durable products. In this article, we’ll delve into everything you need to know about custom molded fiberglass, from its benefits and applications to the process of creating these custom components. By the end, you’ll have a clear understanding of why custom molded fiberglass is such a valuable resource and how it can be applied to your projects.
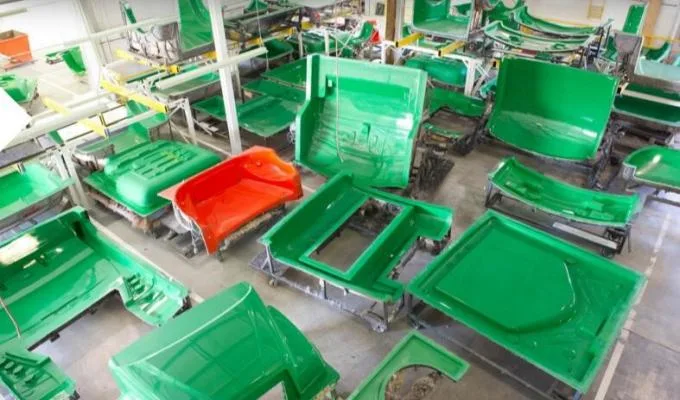
custom molded fiberglass
What is Custom Molded Fiberglass?
Custom molded fiberglass is a type of composite material made from a combination of fine glass fibers and resin, molded into various shapes and forms according to specific requirements. This material is renowned for its high strength-to-weight ratio, resistance to corrosion, and flexibility in design, making it a popular choice across multiple industries. The process of molding fiberglass involves creating a custom mold that matches the desired shape, and then applying the fiberglass material in layers to achieve the final product. Whether it’s for producing complex automotive parts or durable components for marine vessels, custom molded fiberglass offers an ideal solution for creating strong, lightweight, and durable products.
Benefits of Custom Molded Fiberglass
Custom molded fiberglass stands out due to its numerous advantages, which make it an ideal material for a wide range of applications. One of its most significant benefits is its durability and strength. Fiberglass is known for being lightweight yet incredibly strong, able to withstand heavy loads and harsh environmental conditions without deteriorating.
In terms of design versatility, custom molded fiberglass is unmatched. Manufacturers can create virtually any shape or form, allowing for innovative and customized designs that meet specific needs. Additionally, fiberglass is cost-effective, offering a lower cost alternative to metals like steel or aluminum without compromising on quality.
Moreover, fiberglass is highly resistant to corrosion, making it suitable for use in environments where moisture or chemicals are present. Its lightweight nature also makes it easier and less expensive to transport and install, further adding to its appeal.
Applications of Custom Molded Fiberglass
The applications of custom molded fiberglass are as diverse as the material itself. In the automotive industry, fiberglass is used to create lightweight yet durable body panels, hoods, and other structural components that enhance vehicle performance while reducing overall weight.
In the marine industry, custom molded fiberglass is the material of choice for building boat hulls, decks, and other marine structures due to its resistance to saltwater and corrosion. In construction, fiberglass is used for producing architectural elements, roofing materials, and insulation products that provide excellent thermal performance and long-lasting durability.
Industrial and manufacturing sectors also benefit from custom molded fiberglass, using it to create a variety of components and structures that require high strength and resistance to wear and tear. From tanks and pipes to custom industrial machinery parts, the applications are endless.
The Custom Fiberglass Molding Process
Creating custom molded fiberglass involves several steps, each crucial to achieving the desired end product. The process typically begins with the creation of a mold, which serves as the template for the fiberglass component. This mold can be made from various materials, including wood, plastic, or metal, depending on the complexity and size of the part being produced.
Once the mold is ready, the fiberglass material is applied in layers, usually with a resin that bonds the fibers together. Techniques such as hand lay-up, spray-up, or compression molding are used, depending on the specifications of the project. After the layers are applied, the fiberglass is allowed to cure, hardening into the final shape.
Each step in the process requires precision and expertise to ensure the final product meets the required standards of strength, durability, and design accuracy.
Choosing the Right Custom Molded Fiberglass Manufacturer
Selecting the right manufacturer for custom molded fiberglass is crucial to ensuring the quality and longevity of the final product. When choosing a manufacturer, it’s essential to consider factors such as experience, expertise, and the ability to deliver on complex designs.
A reputable manufacturer should have a proven track record in producing high-quality fiberglass products and offer a comprehensive portfolio of past projects. Customer reviews and testimonials can also provide insight into the reliability and professionalism of the manufacturer.
Furthermore, it’s important to assess the manufacturer’s production capabilities, including their ability to handle large-scale orders and deliver within the required timeframes. Ensuring that the manufacturer uses high-quality materials and adheres to industry standards is also key to achieving the best results.
Conclusion
Custom molded fiberglass is a versatile and highly beneficial material, offering numerous advantages across a wide range of industries. Its strength, durability, and design flexibility make it an ideal choice for applications where performance and longevity are paramount. Whether you’re looking to enhance your automotive designs, build durable marine structures, or create innovative architectural elements, custom molded fiberglass is a solution worth considering.
To ensure you get the best possible results, consult with a reputable manufacturer who can guide you through the process and help bring your vision to life. With the right expertise, custom molded fiberglass can provide the perfect balance of strength, durability, and design flexibility for your next project.