Introduction
Customizing car parts has become an exciting hobby for many auto enthusiasts, and fiberglass molds are a crucial part of the process. One of the most popular applications is creating fiberglass bumper molds, which allow for customized and unique bumper designs that enhance both the style and function of a vehicle.
Fiberglass is often the material of choice for this process due to its durability, lightweight nature, and ease of shaping. Whether you’re creating a mold for a sleek sports car or a sturdy off-road vehicle, the possibilities are nearly endless with fiberglass. By crafting your own bumper mold, you can achieve a personalized look that perfectly fits your vehicle.
In this guide, we’ll walk you through everything you need to know about making a fiberglass bumper mold, from the essential tools and materials to the step-by-step process. Whether you’re a seasoned DIYer or just starting out, this article will equip you with the knowledge to bring your custom car project to life.
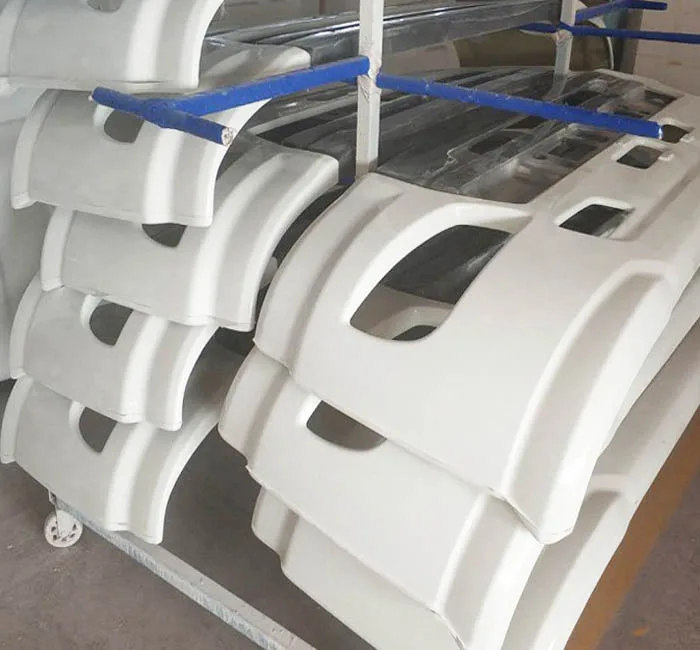
fiberglass bumper mold
1. What is a Fiberglass Bumper Mold?
A fiberglass bumper mold is essentially a negative replica of a bumper’s surface, which serves as a tool for producing multiple identical parts. The mold is crafted by layering fiberglass over the original part or a form, which, once hardened, can be used to shape new bumpers. This is a go-to method for both hobbyists and professionals looking to replicate, repair, or create custom bumpers for cars.
The popularity of fiberglass in mold making stems from its unique properties. It is lightweight, making it easier to work with and handle during the production process. Despite its lightness, fiberglass is incredibly strong and durable, offering the longevity needed for repeated use. Additionally, fiberglass can be easily shaped and layered, which is ideal for the complex curves and details of a car bumper.
Fiberglass molds are particularly common in the auto customization industry. Whether someone is working on a restoration project, designing custom parts, or simply replacing a damaged bumper, a well-made fiberglass mold can save significant time and money in the long run. Once a bumper mold is created, it can be reused multiple times, providing flexibility and cost efficiency.
2. Materials and Tools Needed
Before diving into the process of making a fiberglass bumper mold, it’s important to gather all the necessary materials and tools. Using high-quality materials will ensure a smoother process and more durable results.
Materials:
- Fiberglass Mat or Cloth: This forms the core of the mold. The type of fiberglass (mat or cloth) will depend on the required strength and the level of detail in the bumper.
- Polyester Resin or Epoxy Resin: The resin binds the fiberglass layers together and hardens into a rigid structure.
- Gel Coat: Applied as the outermost layer, the gel coat creates a smooth, high-quality surface for the mold.
- Release Agent (PVA or Wax): Ensures that the fiberglass doesn’t stick to the original bumper or form, allowing easy removal.
- Catalyst/Hardener: Mixed with resin to trigger the curing process.
Tools:
- Mixing Containers: For combining resin with the catalyst.
- Brushes/Rollers: Used to apply resin evenly across the fiberglass layers.
- Sandpaper (Various Grits): For smoothing the surface of the mold once it hardens.
- Cutting Tools (Utility Knife or Shears): To trim excess fiberglass.
- Measuring Tools (Scale or Measuring Cups): Ensures accurate resin-to-catalyst ratios.
Optional but Useful Tools:
- Respirator and Gloves: Fiberglass and resin fumes can be harmful, so safety gear is essential.
- Spray Gun: To apply the gel coat smoothly if aiming for professional-grade results.
Having the right materials and tools in place before starting will make the process smoother and more efficient. While this might seem like a long list, most items are easily accessible at auto supply or hardware stores, and the investment in quality materials will pay off with the durability of the mold.
3. Step-by-Step Guide to Creating a Fiberglass Bumper Mold
Creating a fiberglass bumper mold involves several stages, each requiring attention to detail. Follow these steps to ensure a successful outcome:
Step 1: Preparation
Start by preparing the original bumper or a form that you’ll use to create the mold. Clean the surface thoroughly to remove any dirt, grease, or debris. Once clean, apply a layer of release agent (such as PVA or wax) to the bumper. This is crucial as it prevents the fiberglass from bonding to the surface, making it easier to demold later.
Step 2: Apply the Gel Coat
The first layer to go over the bumper should be the gel coat. This forms the outer surface of the mold and ensures a smooth finish. Using a brush or spray gun, apply an even coat and allow it to cure until tacky but not fully hardened. This usually takes about 20-30 minutes, depending on the specific product used.
Step 3: Lay Down Fiberglass
Once the gel coat is ready, begin laying down strips of fiberglass mat or cloth over the surface. Cut the fiberglass into manageable pieces and apply the resin mixed with a catalyst over each piece. Use a brush to ensure the fiberglass is fully saturated with resin, but avoid pooling, which can cause weak spots.
Apply multiple layers of fiberglass, generally at least three to five layers, depending on the desired thickness and durability. Be sure to press out any air bubbles as you go along, using a roller or brush. Air pockets can weaken the mold and cause imperfections.
Step 4: Curing Process
After the final layer is applied, let the mold cure for several hours (or overnight) until it is completely hardened. This step is critical to ensure that the mold retains its shape and structural integrity.
Step 5: Trimming and Finishing
Once the fiberglass has fully cured, carefully remove the mold from the original bumper or form. Trim any excess material using a utility knife or shears. Use sandpaper to smooth the edges and refine the surface as needed. This will give your mold a professional, clean finish.
Step 6: Demolding
Finally, gently remove the fiberglass mold from the bumper. If you’ve applied the release agent correctly, this step should be straightforward. Inspect the mold for any imperfections or areas that need touch-ups, such as bubbles or uneven surfaces.
4. Common Mistakes and How to Avoid Them
Making a fiberglass bumper mold can be challenging, and there are several common mistakes that beginners should watch out for:
- Uneven Application of Fiberglass Layers: Applying the fiberglass unevenly can lead to weak spots in the mold. Always ensure an even distribution of fiberglass and resin to maintain mold integrity.
- Air Bubbles in the Resin: Air pockets weaken the mold structure and can create imperfections in the final bumper. Use a roller to press out any bubbles and ensure the fiberglass is fully saturated with resin.
- Skipping the Release Agent: Failing to apply enough release agent can cause the fiberglass to stick to the bumper, making it difficult to demold and potentially damaging both the mold and the original part.
By being mindful of these common issues, you can avoid major setbacks during the mold-making process.
5. Benefits of Using a Fiberglass Bumper Mold for Customization
Using a fiberglass bumper mold offers several key benefits, especially for car customization:
- Repeatability: Once you have a mold, you can create multiple identical bumpers without starting from scratch each time.
- Customization Flexibility: Fiberglass allows you to tweak designs, add unique features, or modify the bumper shape to your preferences.
- Cost Savings: Creating your own mold can save money in the long run, especially when compared to purchasing pre-made custom bumpers or having a professional create the mold for you.
- Durability: A well-made fiberglass mold can be used repeatedly without losing its structural integrity, offering long-term value for custom car projects.
Conclusion
Creating a fiberglass bumper mold is a rewarding process for anyone interested in car customization or DIY fabrication. While it requires patience and careful attention to detail, the results can be highly satisfying. By following this guide, you’ll have the knowledge to make your own durable and reusable bumper molds, allowing you to produce custom parts with precision and efficiency.
Ready to get started on your fiberglass bumper mold? Gather your materials, follow these steps, and see how easy it can be to elevate your car customization projects!