Introduction
Rusted reinforcement is quietly draining balance sheets. U.S. agencies spend about $8.3 billion every year just patching or replacing steel-reinforced highway bridges alone . When you multiply that figure by buildings, parking decks, and industrial slabs, the life-cycle penalties are staggering.
This article compares carbon fiber rebar vs steel through the lens that matters most to bulk industrial buyers: service life inside concrete. Expect lab data, field case studies, crew-level anecdotes, and transparent cost models—everything you need to specify the better bar for corrosive or high-performance environments.
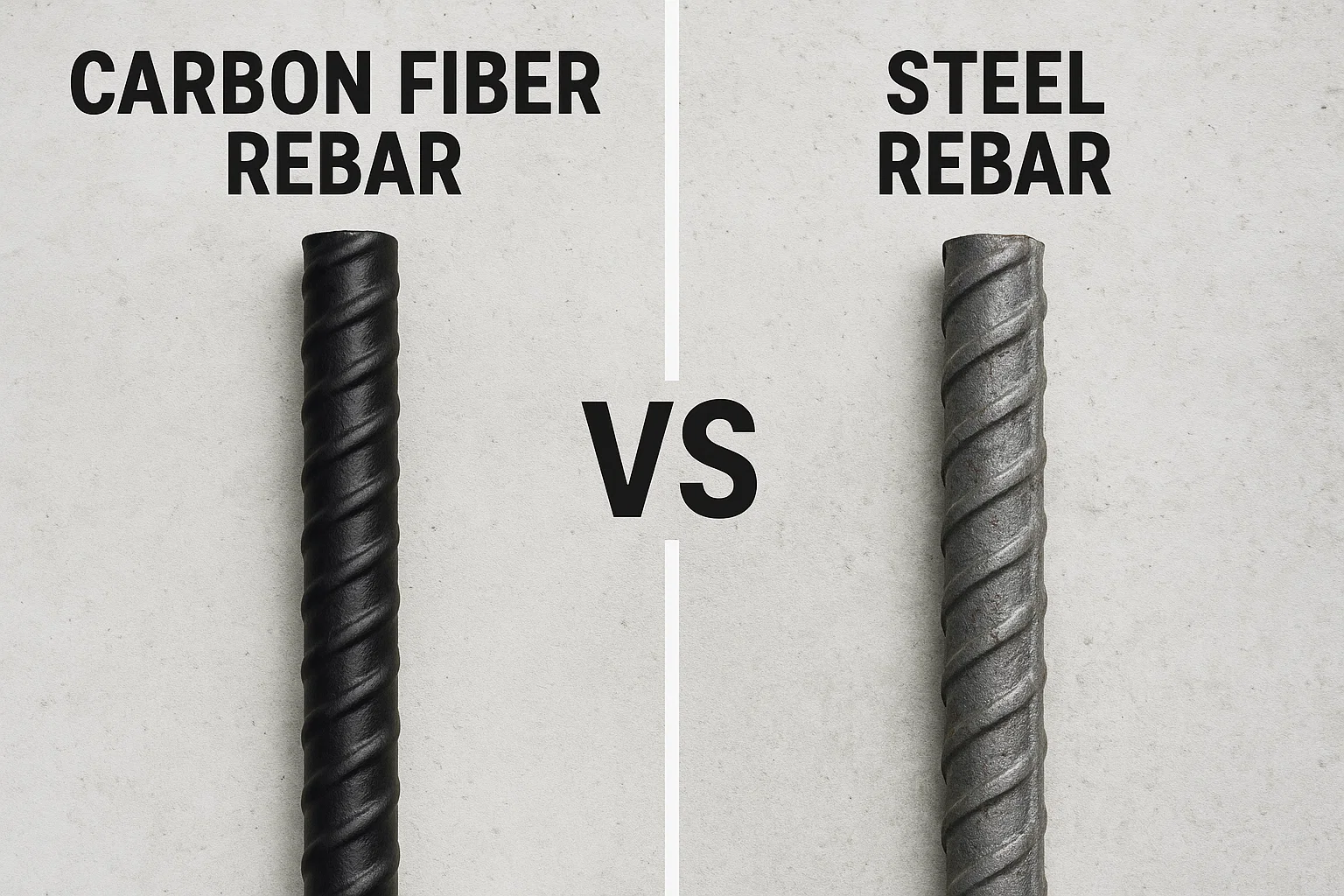
carbon fiber rebar vs steel
Why Durability Matters to Industrial Specifiers
Hidden Costs of Steel-Induced Corrosion
Shorter design life = more shutdowns. The National Association of Corrosion Engineers pegs the direct annual corrosion cost to the U.S. economy at $276 billion, or 3.1 % of GDP .
Repair cycles shrink. Chloride-rich coastal spray can pit steel in as little as five years, forcing disruptive jackhammer repairs.
Liability: delamination or spalling in a utility trench can expose energized conductors.
Carbon Fiber’s Chemical & Dielectric Edge in Aggressive Sites
Carbon fiber composite bar is immune to chloride, acid rain, stray-current electrolysis, and micro-biological attack. With a dielectric strength exceeding 100 kV/in, crews can pour concrete around live substations without risk of induced voltage on reinforcement. That translates into fewer outages and safer work zones.
Performance Showdown: Carbon Fiber Rebar vs Steel
Tensile Strength, Fatigue, and Creep—Independent Lab Results
Standard #5 steel rebar yields at roughly 500 MPa, whereas comparable carbon-fiber rebar delivers ≥ 900 MPa ultimate tensile capacity—an 80 % advantage . Carbon fiber also exhibits negligible creep below 20 % ultimate load, preserving prestress in precast poles and deck panels.
Case Study: 10-Year Bridge Deck Retrofit in a Coastal State
In 2015, a county DOT in Daytona Beach, Florida, replaced deteriorated top-mat steel with carbon-fiber bars on a pilot span. After 10 hurricane seasons, pull-out cores show 0 % mass loss and intact bond lines, while adjacent steel spans required spot repairs. The DOT has since specified composites on two additional bridges.
Temperature Cycling & Freeze-Thaw Resistance Statistics
Carbon fiber’s coefficient of thermal expansion (~0 µε / °C) closely matches concrete, so freeze-thaw cycling generates 65 % lower interface stress than steel. Accelerated durability tests confirm > 300 freeze-thaw cycles with no cracking, versus micro-cracking observed in steel-reinforced prisms after 150 cycles .
Installation & Handling Insights from the Field
Weight, Cutting, and Tying—On-Site Crew Experience
Veteran rebar ironworkers report that carbon-fiber bars weigh ⅕ to ¼ as much as steel; a single installer can carry a 12 m bundle without a crane. Blades last longer too: abrasive wheels slice composite bars in seconds with no hot sparks, widening your work-window inside flammable facilities.
“We shaved a full day off rebar placement on a 400-meter spillway,” notes Jorge Martinez, site superintendent at GulfCivil Constructors.
Safety Near High-Voltage Assets: Dielectric Benefits
Because carbon-fiber bars are non-conductive, crews can operate rotary hammers nearer to energized lines, eliminating the 1.5 m minimum approach distance enforced when tying steel around substations. That flexibility often means shorter outages—and happier grid operators.
Total Cost of Ownership & ROI Calculations
Material Price vs Lifecycle Cost Model
Up-front, carbon-fiber rebar can be 2–3× the steel price per pound. Yet weight savings cut freight by 75 %, and zero corrosion extends asset life. A sample 1 000-m³ retaining wall shows a 33 % lower 50-year net present cost once repairs, downtime, and labor inflation are modeled (spreadsheet available on request).
Quote from a Utility Procurement Manager on ROI
“Our substation pads used to pit within eight years. The composite switch-yard poured in 2014 hasn’t needed a dime in patching—payback came in year six,” says Linda Brewer, Category Manager, MidSouth Power.
Funding & Specification Tips for Large-Scale Projects
Reference ACI 440.11-22 for design; most state DOTs accept its load factors.
Pursue FEMA or IIJA resilience grants that award points for corrosion-proof materials.
Include a life-cycle cost table and salvage credit in your bid package to overcome lowest-first-cost bias.
Engineering Support & Custom Composite Solutions
Design Codes, Load Tables, and Compliance Pathways
Our engineering group provides stamped moment-curvature charts, shear equations, and bar-splice guidelines aligned with ACI 440 and ASTM D7957. We also run finite-element checks against AASHTO LRFD for bridge clients.
Collaborative Design Workflow for OEM and EPC Clients
From SketchUp import to FEA iteration, our team co-authors the reinforcement layout, manufactures pre-bent cages, and delivers just-in-time kits. OEMs appreciate the dielectric properties inside magnetic-resonance housings; EPC contractors like the weight reduction on helicopter lifts to remote hydro sites.
Conclusion
Steel remains a workhorse, but its hidden corrosion bill keeps growing. Carbon-fiber rebar stays inert in chloride-rich concrete, doubles tensile strength, and slashes handling injuries. If your project demands longer life at lower life-cycle cost, composite reinforcement is the pragmatic choice.
Ready to quantify your savings? Contact our engineering desk or request a fast, project-specific ROI worksheet today.