Introduction
Slips, trips, and falls remain one of the top causes of workplace injuries worldwide. In the United States alone, they account for nearly 15 % of all accidental deaths—second only to motor‑vehicle incidents. As facilities managers look to minimize these incidents, slip resistant fiberglass grating has emerged as a proven, high‑performance flooring solution. This article unpacks seven key benefits of using fiberglass grating in industrial settings—and shows why it consistently outperforms traditional steel and aluminum options.
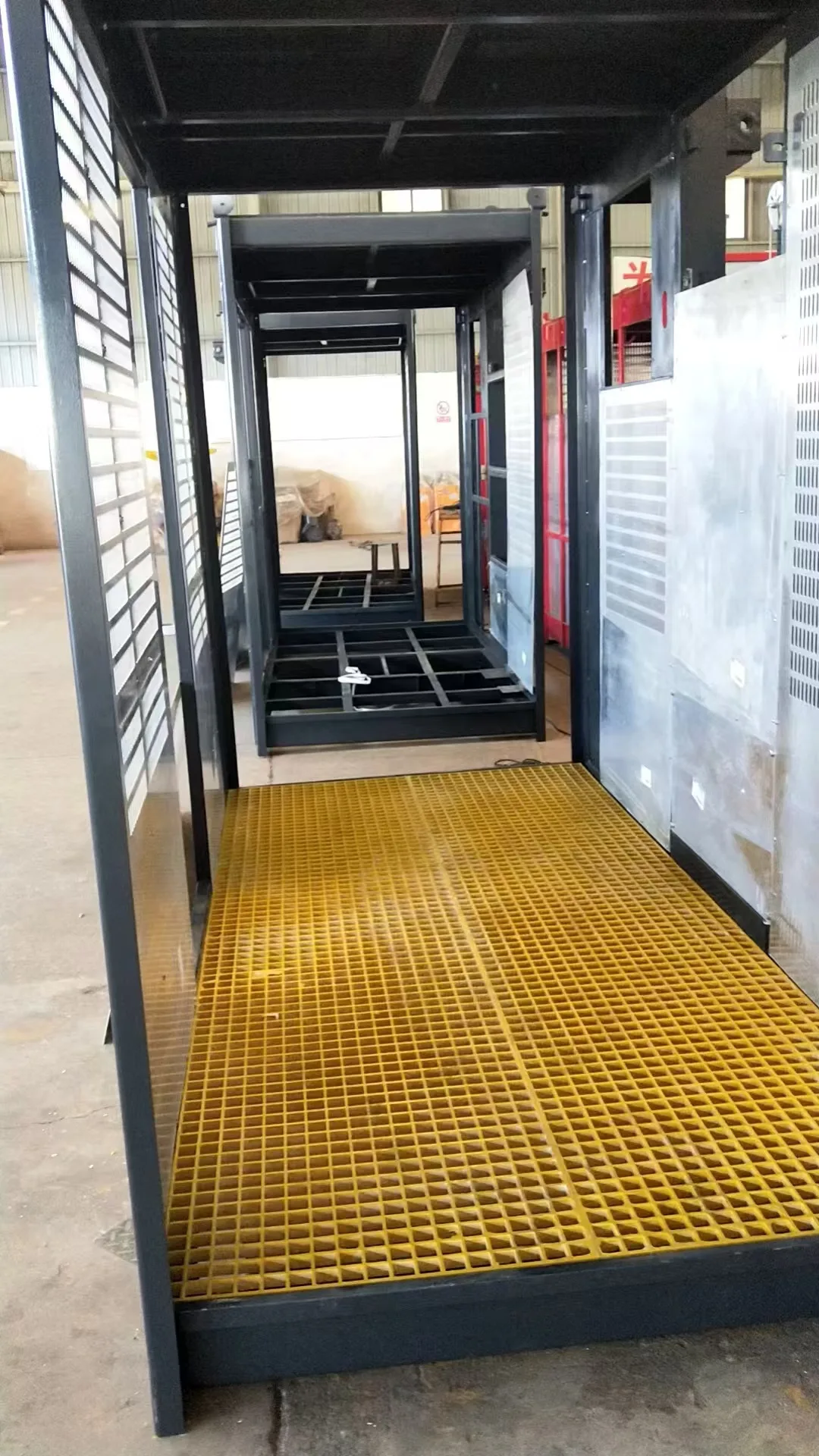
slip resistant fiberglass grating
Benefit 1: Superior Slip Resistance Reduces Accidents
Fiberglass grating panels are manufactured with an aggressive grit‑top surface or molded‑in meniscus profile that delivers traction even when coated with oil, water, or chemical residue. Plant trials show that switching from smooth steel plate to grit‑top fiberglass grating can cut slip incidents by up to 50 % in wet process areas. By embedding the anti‑skid surface into the resin matrix, manufacturers ensure the texture lasts for the life of the panel—no toe‑kicking checker plate or aftermarket tapes required.
Actionable tip: When specifying, ask for ASTM E‑84 tested panels with an average coefficient of friction (COF) ≥ 0.6 under wet conditions.
Benefit 2: Corrosion and Chemical Resistance Extends Lifespan
Steel flooring must be painted, galvanized, or coated—and any scratch becomes a corrosion hot‑spot. In contrast, fiberglass grating is inherently corrosion‑resistant because its glass fibers are encapsulated in a vinyl‑ester or isophthalic polyester resin. In sulfuric‑acid wash bays and coastal wastewater plants, FRP (fiber‑reinforced polymer) grating routinely lasts 20–25 years without recoating, saving thousands in downtime and repainting costs.
“Our chemical tanks used to need new steel walkways every five years. We installed FRP grating a decade ago, and it still looks new.”
— Liang Wei, Maintenance Superintendent, Ningbo Petrochem
Benefit 3: Lightweight Design Simplifies Installation
A square meter of 38 mm‑thick slip resistant fiberglass grating weighs roughly 11 kg, less than half the weight of an equivalent steel panel. Two workers can easily carry and drop‑in full sheets without cranes, speeding shutdown turnarounds. Lower dead‑load also means you can reduce sub‑structure steel, cutting project capex.
Quick checklist
✔️ Single‑person manageable panels (≤ 25 kg)
✔️ No hot‑work permits for on‑site cutting (use carbide blade)
✔️ Lower freight costs for remote mines or offshore rigs
Benefit 4: High Strength‑to‑Weight Ratio Supports Heavy Loads
Don’t let the word “fiberglass” fool you. Molded FRP panels achieve tensile strengths up to 240 MPa, rivaling structural steel on a per‑weight basis. For standard industrial walkways, 38 mm panels safely span 1.5 m under a 500 kg/m² live load with less than 6 mm deflection. Pultruded grating can handle point loads from forklift traffic when properly supported.
Benefit 5: Low Maintenance Cuts Long‑Term Costs
Because FRP does not rust or require repainting, maintenance crews need only perform routine wash‑downs. Over a typical 20‑year service life, lifecycle cost analyses show fiberglass grating delivers 30–40 % lower total cost of ownership versus galvanised steel. Factor in fewer slip injuries—and the savings climb even higher.
Benefit 6: Electrical & Thermal Non‑Conductivity Improves Safety
Fiberglass grating’s glass‑fiber core acts as an insulator, making it an excellent choice around live electrical gear or cryogenic lines. Surface resistivity typically exceeds 1014 Ω‑cm, while thermal conductivity is roughly one‑third that of aluminum. This mitigates shock hazards and keeps walking surfaces comfortable for personnel in extreme temperatures.
Benefit 7: Compliance with Safety Standards and Regulations
OSHA 1910.22 requires walking‑working surfaces to be kept free of hazards. Using a flooring system purpose‑built to prevent slips is a proactive way to satisfy inspectors. In 2024, the Bureau of Labor Statistics recorded 865 fatalities linked to slips, trips, and falls—underscoring the urgency for compliant solutions. Many fiberglass grating products also carry third‑party certifications such as DNV (offshore) and ABS (marine), streamlining global approvals.
Conclusion & Next Steps
From dramatically lowering accident rates to slashing maintenance budgets, slip resistant fiberglass grating offers a compelling safety and economic case for industrial facilities. If your plant still relies on painted steel or slick aluminum plate, consider auditing high‑traffic zones and replacing them with FRP during the next turnaround.
Ready to take the next step?
Assess: Walk your facility and list areas with frequent spills or corrosion.
Specify: Consult a reputable FRP supplier for grit‑top panels matched to your chemical exposure and load requirements.
Implement: Start with a pilot installation—then roll out plant‑wide when you see the results.
Have questions or success stories about fiberglass grating? Share them in the comments, forward this article to your safety team, or subscribe to our newsletter for more actionable insights on industrial flooring solutions.