Introduction
Creating a fiberglass fuselage mold is a key step in manufacturing lightweight, durable aircraft components—particularly for radio-controlled planes and small experimental aircraft. By using fiberglass, you can achieve a strong, smooth, and aerodynamic shell without adding unnecessary weight. In this article, we’ll explore five essential tips for perfecting your fiberglass fuselage mold, covering everything from initial planning to post-processing. Whether you’re a hobbyist or an industry professional, these insights will help you streamline your workflow and produce top-quality results.
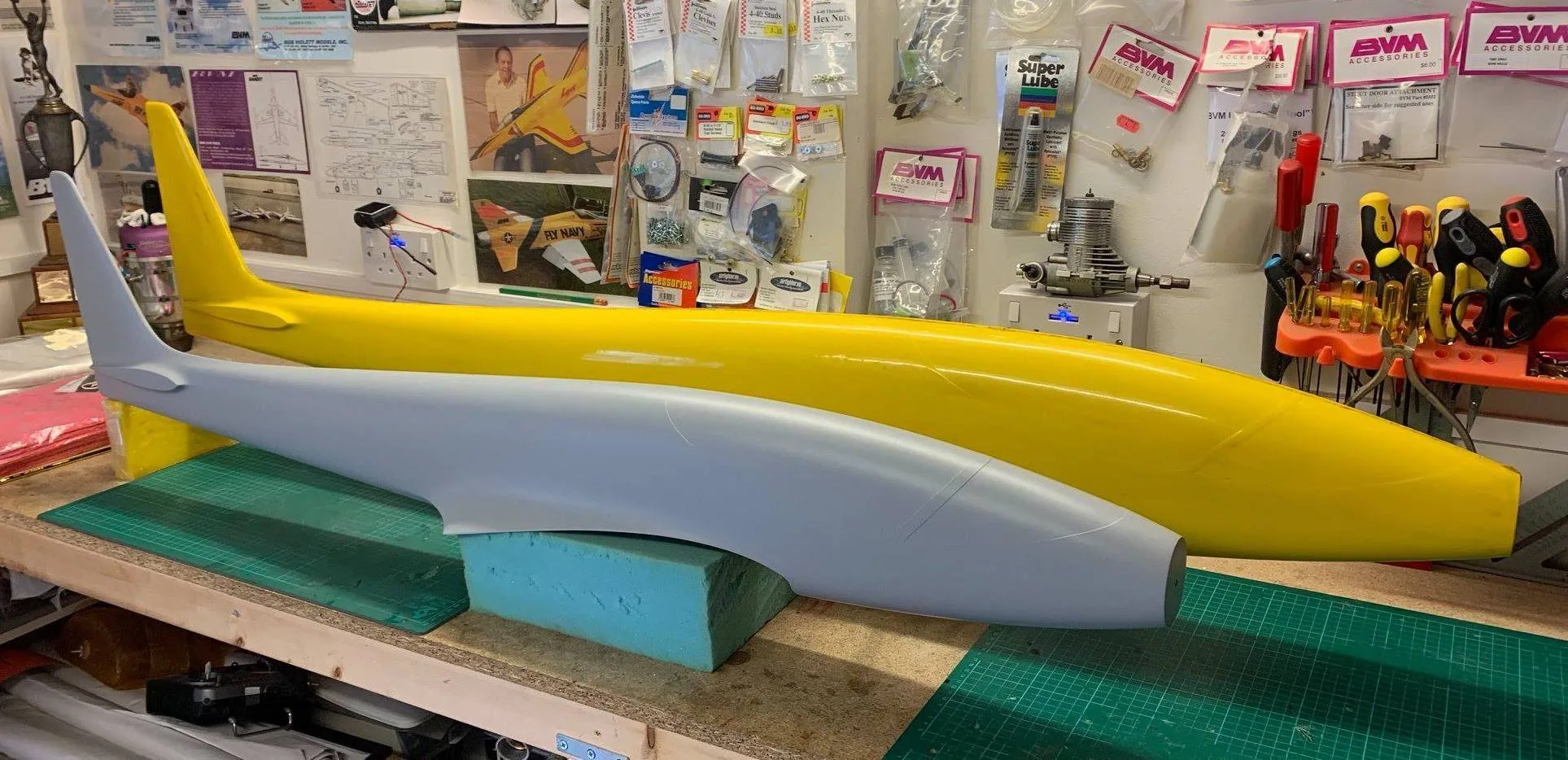
fiberglass fuselage mold
Understanding the Basics of Fiberglass Fuselage Molds
Why Fiberglass Is Ideal
Fiberglass is widely used in the aviation and marine industries for good reason. It’s:
- Lightweight: Minimizes overall mass without compromising on strength.
- High Strength-to-Weight Ratio: Increases structural integrity.
- Corrosion Resistance: Offers longevity even in varying environmental conditions.
- Relatively Affordable: Compared to some carbon fiber applications, fiberglass remains cost-effective.
According to the American Composites Manufacturers Association, fiberglass composites account for over 40% of the composites market due to their versatility and performance. For hobbyists and small-scale aircraft builders, fiberglass molds are an excellent choice, delivering reliable and long-lasting results.
Key Materials & Tools
Before you get started, it’s crucial to gather the right supplies. Here’s a quick checklist:
- Fiberglass cloth or mat (different weights and weaves for strength)
- Resin system (polyester, epoxy, or vinyl ester, depending on project requirements)
- Release agent (wax or PVA to prevent sticking)
- Plug or master model (the shape you want to replicate)
- Safety equipment (gloves, goggles, respirators)
- Measuring tools and mixing cups
- Rollers and brushes for applying resin
- Sanding and polishing materials (various grit sandpapers, polishing compounds)
Ensuring you have high-quality materials and the correct tools will save time, reduce mistakes, and help you get a superior final mold.
Tip #1 – Meticulous Planning and Design
Proper Blueprint & Dimensions
The quality of your fiberglass fuselage mold hinges on precise planning. A detailed blueprint or CAD design is essential to map out the shape, size, and features of your fuselage. Make sure all dimensions are accurate and consider any functional details:
- Scale and Proportion: Maintain the correct ratio for all components.
- Access Ports: If you need openings for internal components, account for these in your design.
- Structural Reinforcements: Identify where extra layers of fiberglass might be required for added strength.
Identifying Potential Challenges Early
Before creating the mold, analyze common problem areas:
- Complex Curves or Undercuts: These can be tricky to lay up with fiberglass and may require multi-part molds or additional bracing.
- Weak Points: Areas where the mold might flex or warp during curing, leading to deformations in the final part.
- Layer Overlaps: Where layers of fiberglass might bunch up, creating uneven surfaces or air pockets.
By anticipating these issues, you’ll be better prepared with the right strategies—such as adding temporary supports or using specialized fabrics—for a smoother, more reliable process.
Tip #2 – Preparing the Plug & Using Release Agents
Achieving a Smooth Plug Surface
The plug, also known as the master model, is your positive form. This is what you’ll be replicating with your fiberglass mold. A high-quality plug is essential to avoid defects later on:
- Fill and Sand: Fill any gaps or imperfections in the plug surface, then sand it smooth with progressively finer grits of sandpaper.
- Polish: Achieve a glossy finish to minimize irregularities.
- Inspect Under Good Lighting: Small imperfections can cause noticeable flaws in your mold, so be thorough.
Applying High-Quality Release Agents
A reliable release agent ensures your fiberglass fuselage mold separates cleanly from the plug. Choose from wax-based or PVA-based agents (or use both for added assurance). Apply multiple coats, following these guidelines:
- Thin Coats: Several thin layers are better than one thick application.
- Buff Between Layers: Buff each layer gently to enhance the glossy finish.
- Adhere to Drying Times: Check the manufacturer’s recommendations for optimal performance.
Tip #3 – Layering Fiberglass for Strength
Resin Selection & Mixing Ratios
Selecting the right resin—polyester, epoxy, or vinyl ester—depends on factors like cost, cure time, and final part requirements. Whichever resin you choose, follow these best practices:
- Accurate Ratios: Use precise measurements of resin and hardener for consistent curing.
- Proper Mixing: Stir slowly to avoid introducing excessive air bubbles.
- Work in Manageable Batches: Large amounts of resin can heat up quickly, reducing your working time.
Layering Techniques for Durability
Layering fiberglass involves laying cloth or mat in overlapping sections with resin in between. To ensure strength and uniform thickness:
- Start with a Gel Coat: If desired, brush a pigmented or clear gel coat onto the plug first, allowing it to partially cure.
- Alternate Cloth Directions: Rotate the orientation of the fiberglass layers (e.g., 0°, 45°, 90°) to distribute stress more evenly.
- Consolidate Each Layer: Use rollers to press out air bubbles and ensure saturation without excess resin.
- Build Up Gradually: Avoid adding too many layers at once, as trapped heat can cause premature curing or warping.
Tip #4 – Precision in Trimming & Finishing
Removing Excess Fiberglass Safely
Once you’ve applied the necessary layers, you’ll need to remove the extra material while the resin is still in a semi-cured state or after full curing. Consider these safety and efficiency tips:
- Wear Protective Gear: Gloves, goggles, and a mask to prevent exposure to fiberglass dust.
- Use Sharp Tools: Utility knives or rotary cutters can be employed for semi-cured materials; diamond blades or tungsten-carbide tools for fully cured parts.
- Plan Your Cut Lines: Mark where you need to cut before the resin hardens to avoid guesswork.
Sanding & Polishing the Mold
After trimming, the mold edges may be rough. To refine:
- Sand in Stages: Start with 80- or 100-grit and progress up to 400- or 600-grit for a smoother surface.
- Eliminate Sharp Edges: Round off any corners to reduce chipping or cracking.
- Polish for Optimal Shine: A polished mold surface makes de-molding easier and yields a cleaner final fuselage.
Tip #5 – Proper Curing and Post-Processing
Monitoring Cure Time & Temperature
Curing is a critical phase. Resin properties can vary significantly based on temperature and humidity:
- Follow Manufacturer Instructions: Each resin system has a recommended curing temperature range.
- Maintain Even Heat: If you’re using heat lamps or an oven, ensure the entire mold receives uniform temperature.
- Allow Full Cure: Rushing this step can result in a weaker mold prone to warping or surface defects.
Post-Processing Checks & Maintenance
Once the mold is fully cured, inspect it thoroughly:
- Look for Cracks or Air Voids: Address these issues before they worsen.
- Reapply Release Agent: A fresh coat of release agent before each use extends mold life.
- Store Properly: Keep molds away from direct sunlight and extreme temperatures to maintain structural integrity.
Conclusion
Perfecting your fiberglass fuselage mold is a combination of careful planning, quality materials, and disciplined technique. By adhering to these five tips—from thorough initial designs to attentive post-processing—you set the stage for producing high-quality, durable fuselages that meet both aesthetic and functional demands. Whether you’re an avid aircraft modeler or a professional builder, every step counts toward achieving that flawless final product.
Ready to put these tips into action? Share your experiences, questions, or success stories in the comments below. Don’t forget to subscribe to our newsletter for more expert insights on fiberglass work, aviation builds, and advanced composite techniques. Let’s continue refining our craft and building better aircraft together!