Introduction
Fiberglass mold construction is a cornerstone in industries such as automotive manufacturing, aerospace, and even custom DIY projects. Whether you’re building a small prototype or a large-scale production part, the mold itself is what determines the accuracy, consistency, and overall quality of the final product. In this article, we will walk through five essential steps in fiberglass mold construction—from initial planning to finishing touches—ensuring you have a reliable blueprint for success. By following these steps, you’ll minimize costly mistakes and produce molds that stand the test of time.
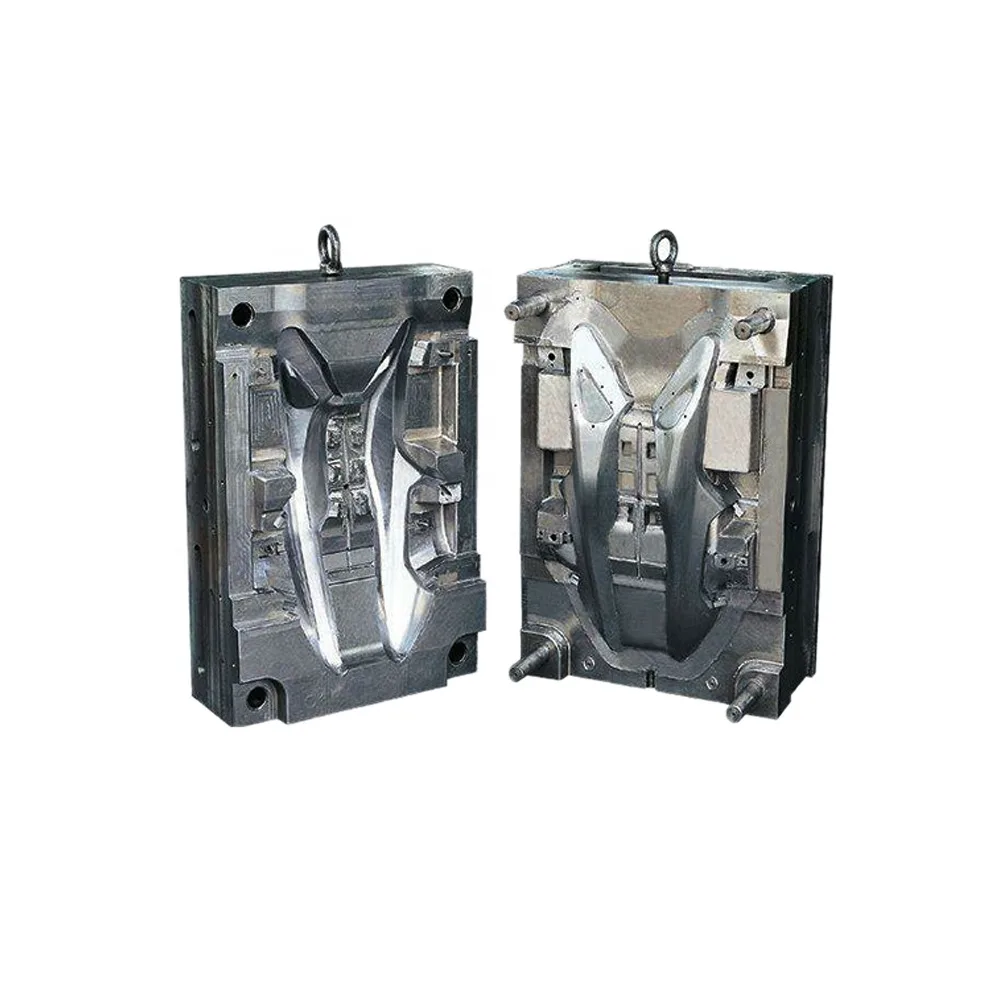
fiberglass mold construction
Step 1 – Planning and Design
A successful fiberglass mold construction project begins with careful planning. Spending time on design work upfront can save you significant labor and material costs later.
Determining Project Scope and Requirements
Before diving in, clearly define what you want the final fiberglass part to look like. Consider:
- Dimensions and shape: Is it a simple flat panel or a complex contoured piece?
- Surface quality: Will the part be purely functional, or does it require a cosmetic finish?
- Production volume: Are you making a single prototype or a large batch?
In addition to clarifying these questions, gather information on any specific performance requirements. For instance, if your part needs to withstand high temperatures, you’ll need resin and reinforcement materials that can handle those conditions. According to a survey conducted by the Composites Manufacturing Association, 60% of fiberglass failures occur due to using the wrong type of resin, highlighting the importance of correct material selection.
Sketches and CAD Models
Once you have your project’s scope, create a visual reference. This can be as simple as hand-drawn sketches or as advanced as computer-aided design (CAD) models. Precise design details help you:
- Accurately measure the mold dimensions
- Identify weak points or complex curves that need reinforcement
- Plan your material usage efficiently
By investing time in detailed plans, you minimize mistakes and wasted resources.
Step 2 – Creating the Pattern or Plug
The pattern or “plug” is the positive form you’ll use to create the negative mold. This part is critical because any flaw in the plug will transfer directly to your mold—and eventually to every part made from that mold.
Choosing the Right Material
Common materials for plugs include foam, wood, or plaster.
- Foam: Lightweight and easy to carve, ideal for complex shapes but may require extra sealing.
- Wood: Durable and readily available, but can be time-consuming to shape for intricate designs.
- Plaster: Good for large, simple forms, though it’s heavier and can be brittle.
Your choice largely depends on budget, complexity, and the tools at your disposal.
Shaping and Refining the Plug
Precision is key. Use shaping tools, sandpaper, and fillers to remove any imperfections.
- Rough cut or carve the general shape.
- Sand and smooth using progressively finer grit papers.
- Fill any gaps or pores with body filler or putty.
The goal is to achieve the exact contours and smoothness you want in the final mold. If you plan to produce parts with a glossy finish, ensure the plug has a mirror-like surface; otherwise, you’ll spend more time fixing issues later.
Step 3 – Preparing the Mold Surface
A properly prepped surface prevents the fiberglass from adhering to the plug, ensuring the mold can be removed smoothly once the fiberglass has cured.
Sealing and Releasing Agents
Begin by sealing the plug’s surface with a protective layer of primer or special sealant if the material is porous (like foam). This step helps achieve an even finish and prevents resin from seeping in.
- Apply a wax-based release agent or PVA (polyvinyl alcohol) release film over the sealed plug.
- Ensure even coverage with no missed spots to avoid sticking.
According to a report by Composite World Magazine, using a high-quality mold release can reduce the chances of part damage during demolding by up to 70%.
Reinforcing the Plug
For larger projects, add braces or a backing structure around the plug. This ensures stability and maintains the shape’s integrity during the fiberglass lay-up. Materials such as MDF (medium-density fiberboard) or metal frames are commonly used to keep the plug rigid.
Step 4 – Laying Up Fiberglass
Once the plug is sealed and reinforced, you’re ready to start the actual fiberglass process.
Layering Strategy
- Choose the right fiberglass cloth or mat based on the required mold strength and complexity. Woven roving or chopped strand mat are popular options, each with unique benefits.
- Mix the resin (often polyester or epoxy) according to the manufacturer’s instructions, paying close attention to temperature and catalyst ratios.
- Apply a thin “gel coat” or resin layer to the plug first, which forms the mold’s inner surface.
- Lay the fiberglass in multiple layers, saturating each layer thoroughly with resin before adding the next.
This step-by-step layering builds thickness and strength. Some professionals recommend at least two or three layers for basic molds; more layers provide better durability for repetitive use.
Curing and Inspection
Allow the fiberglass to cure under recommended conditions (often room temperature or slightly heated settings). Pay close attention to:
- Curing time: Check manufacturer’s guidelines—rushing can compromise the mold.
- Imperfections: Look for air bubbles or resin-starved areas and fix them immediately by adding more resin or smoothing out trapped air with a roller.
Once it’s fully cured, carefully separate the mold from the plug. If you’ve done everything correctly, it should come away smoothly.
Step 5 – Final Touches and Mold Maintenance
With the fiberglass mold separated, you’re in the home stretch.
Trimming and Finishing the Edges
Use cutting tools or a rotary tool to remove any excess fiberglass from the mold edges. Smoothing the edges helps prevent accidental cuts or snags during future use. Spend time polishing or waxing the mold’s internal surface if your final parts require a glossy finish.
Long-Term Care of Your Mold
Proper maintenance can significantly extend the mold’s lifespan, even if you plan to produce hundreds of parts.
- Clean the mold thoroughly between production runs. Leftover resin or debris can cause surface defects.
- Reapply release agents as needed to maintain an easy separation.
- Store the mold in a stable environment, away from extreme temperatures or direct sunlight, which can warp fiberglass over time.
Conclusion
Fiberglass mold construction doesn’t have to be overwhelming. By following a systematic approach—starting with thorough design work, refining the plug, prepping surfaces correctly, layering fiberglass with care, and finishing with proper trimming and maintenance—you’ll set yourself up for success. This methodical process not only saves you materials and money but ensures high-quality, repeatable results.
Now that you have a clear guide, it’s time to put this knowledge into action. Have questions, or want to share your own fiberglass mold construction tips? Leave a comment below and spread the word to fellow creators and enthusiasts. A well-crafted mold is the foundation for any outstanding fiberglass product, and with these five essential steps, you’re ready to tackle your next project with confidence.