Introduction
Duragrid fiberglass grating has become a go-to solution for architects, engineers, and maintenance managers who need a flooring system that’s lightweight, corrosion-resistant, and easy to install. In fact, analysts project the global FRP grating market will climb from USD 623.8 million in 2023 to almost USD 958 million by 2033—a 4.5 % CAGR, underscoring soaring demand for products like Duragrid.Yet, for all its advantages, costly missteps still crop up at the specification stage. Below are five of the most common—and practical ways to dodge them.
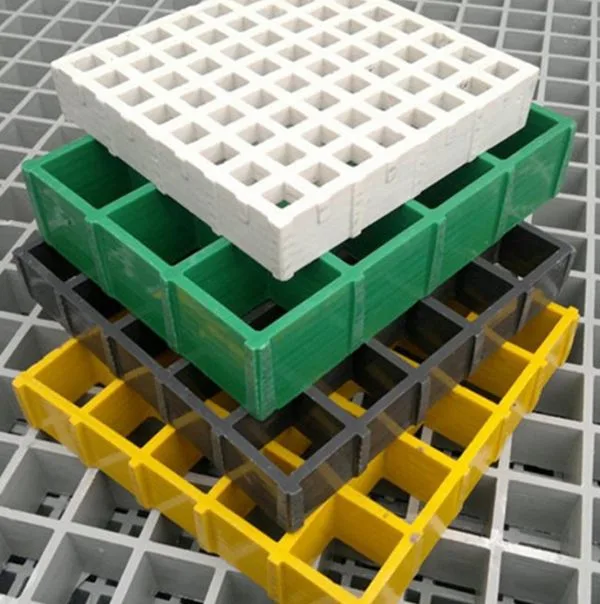
duragrid fiberglass grating
1. Ignoring Real-World Load and Deflection Limits
The mistake: Selecting panel depth and bar spacing based solely on catalog charts without checking live-load conditions or span length.
Why it matters: Excess flex can crack resin bonds, loosen hold-down clips, and create trip hazards. Strongwell, a leading FRP authority, recommends limiting pedestrian deflection to ¼ inch (6 mm) for comfort and clip integrity.
How to avoid it:
Start with the span, not the panel. Calculate maximum unsupported distance first, then refer to Duragrid load tables.
Factor in dynamic loads. Forklifts, pallet jacks, wind, or wave action can double static loads.
Specify allowable deflection in the bid documents. A clear “L/240 or ¼ inch, whichever is less” clause prevents value engineering from eroding performance.
2. Overlooking Corrosion Class and Resin Selection
The mistake: Defaulting to an all-purpose polyester resin when the environment requires vinyl ester or phenolic.
Why it matters: The wrong resin can blister or leach under aggressive chemicals, shortening service life by years.
How to avoid it:
Conduct a chemical exposure audit. List every liquid, vapor, or spill the grating may encounter.
Match pH and temperature. Consult Duragrid’s chemical resistance guide and note that even “neutral” seawater becomes aggressive at elevated temperatures.
Document resin type on drawings. Write “Duragrid I-4000, VE resin” rather than “FRP grating” to lock in the correct material grade.
3. Neglecting Surface Grit and Slip-Resistance Ratings
The mistake: Ordering smooth-top panels to save a few dollars, then discovering the walkway becomes an ice rink in wet or oily conditions.
Why it matters: Lawsuits stemming from slips can dwarf material savings. Duragrid’s factory-applied silicon-carbide grit typically raises the coefficient of friction (COF) above 0.6 — well above OSHA’s 0.5 guideline for ramps.
How to avoid it:
Specify grit grade and coverage. “Medium grit, full-panel” gives installers no room for shortcuts.
Consider color visibility. Safety-yellow panels alert workers to edge locations and ladder openings.
Add a cleaning protocol. High-pressure rinses restore grit effectiveness in food or pulp & paper plants.
4. Skipping Thermal Expansion Allowances
The mistake: Bolting panels tight to structural steel, as one would with steel grating.
Why it matters: Fiberglass expands roughly twice as much as steel. Without ⅛ inch gap per 3 feet of panel length, thermal growth can bow panels or shear fasteners.
How to avoid it:
Use slotted clips or oversized holes. Hardware designed for FRP lets panels “float.”
Gap perimeter panels. Leave a ¼ inch clearance at walls and equipment bases.
Check regional temperature swing. A coastal refinery with −10 °C to 45 °C range may need larger gaps than an indoor plant.
5. Failing to Plan for Field Modifications and Edge Sealing
The mistake: Assuming the installer will fabricate cutouts without guidance, leading to ragged saw edges and unsealed glass fibers that wick chemicals.
Why it matters: Exposed fibers compromise corrosion resistance and can cause skin irritation during maintenance.
How to avoid it:
Specify cutting tools. A worm-drive saw with diamond blade or carbide grit edge reduces chipping.
Include a resin-topcoat kit in the order. Field crews can reseal cut edges immediately, eliminating an extra procurement step.
Provide a shop drawing of all penetrations. Pre-planning stair stringer notches or pipe cutouts saves time and ensures load paths aren’t weakened.
Conclusion
By sidestepping these five pitfalls—load miscalculations, resin mismatches, inadequate slip protection, thermal mis-alignment, and poor edge treatment—you’ll unlock the full 20-plus-year lifespan Duragrid fiberglass grating is designed to deliver. Remember: precise specs on the front end cost far less than retrofits after installation.
Call to Action
Have questions about selecting the right Duragrid panel, resin, or fastener set for your project? Drop your query in the comments or reach out via our contact form. If you found this guide useful, share it with a colleague and subscribe for more FRP insights.